The automotive industry is undergoing significant changes in how parts and components are transported and stored, driven by the need for greater efficiency, sustainability, and cost-effectiveness. As global supply chains grow more complex, manufacturers and logistics professionals are seeking forward-thinking packaging methodologies that safeguard products, optimize workflows, and align with stringent environmental requirements. These packaging innovations offer a transformative edge—empowering businesses to reduce waste, lower costs, and stay competitive.
Whether dealing with large engine blocks or delicate electronic sensors, the packaging chosen can be the difference between seamless operations and costly disruptions. Below, we explore eight prominent trends reshaping the world of automotive packaging while providing practical guidance on implementing them for maximum benefit.
Reusable Packaging Materials Driving Efficiency in Automotive Logistics
A major shift in the automotive industry focuses on using packaging engineered for repeated use. Reusable packaging materials like
- corrugated plastic containers,
- durable steel racks,
- textile-based dunnage, and
- other reusable packaging solutions
have become increasingly popular. Their robust construction, standardized dimensions, and resistance to moisture and chemicals allow multiple cycles of use, reducing the frequency of replacement.
Key benefits of switching to reusable packaging include:
- The ability to reuse packaging through numerous shipping cycles, thereby reducing long-term expenses.
- A reduced environmental footprint by diverting large volumes of single-use waste from landfills.
- Better compatibility with automated systems due to consistent shapes and materials.
- Enhanced protection for sensitive automotive parts as a result of solid structural integrity.
- The potential for significant savings on material and labor costs over time.
By integrating a streamlined return process, automotive manufacturers can recapture packaging for refurbishment and reuse, further enhancing sustainability. Such closed-loop models also improve supply chain visibility, allowing companies to track packaging assets and minimize loss or damage.
Custom Packaging Designs for Automotive Parts
Because automotive components differ significantly in shape, size, and fragility, uniform packaging often leads to a mix of overprotection and underprotection. Custom packaging solutions address these inconsistencies by tailoring every detail—from internal compartments to cushioning mediums—to the exact specifications of each part.
Customization often involves:
- Precision-fit foam inserts and molded trays that keep delicate parts in place, mitigating the risk of impact.
- Color-coded trays and kitting totes that expedite assembly by simplifying the identification and retrieval of multiple component types.
- Specialized containers that optimize stacking and cubing in trucks or containers, reducing transportation costs.
Such made-to-order solutions streamline production processes, reduce shipping damage, and ensure a consistent level of quality. Many automotive manufacturers rely on detailed engineering analyses—sometimes leveraging 3D modeling—to finalize custom packaging design before production. This approach helps avoid costly revisions, saving time and resources.
Sustainability-Driven Packaging Solutions
Sustainability has become a major priority across industries, and automotive packaging is no exception. The emphasis now falls on implementing earth-friendly methods with minimal waste and reduced resource consumption. Sustainable packaging not only addresses environmental concerns but also meets consumer expectations and supports regulatory compliance.
A few sustainable packaging strategies include:
- Using recycled or biodegradable materials to lessen dependence on virgin resources.
- Shifting to lighter packaging designs that require fewer raw materials while maintaining durability.
- Establishing a closed-loop recycling framework—retrieving used packaging, processing it, and creating new containers in-house or with supply chain partners.
- Exploring biomaterials with lower lifecycle environmental impacts.
Adopting these approaches can yield a competitive edge. Research indicates that companies investing in sustainable packaging strategies may experience enhanced brand reputation and improved regulatory compliance.
Technology-Enabled Smart Packaging Systems
Rapid digitization has revolutionized logistics, and packaging is no exception. Smart packaging uses embedded technology—like RFID tags and machine-readable codes—to offer real-time information on a shipment’s location, environmental conditions, and handling history. Integrated sensors can immediately alert managers if a package surpasses safe thresholds for temperature, vibration, or humidity.
By providing unprecedented transparency, these systems help reduce product damage rates, improve traceability, and enable proactive interventions. Benefits of smart packaging include:
- Continuous monitoring of critical components such as batteries and delicate sensors in transit.
- Real-time notifications that flag potential delays or mishandling.
- Access to valuable data for analyzing and improving packaging configurations, shipping routes, and handling protocols.
- Preventive maintenance by identifying packaging at a higher risk of wear before it causes operational bottlenecks.
Smart packaging also fosters a data-driven culture. Collected metrics support predictive analytics, guiding the development of more efficient shipment strategies and optimizing resource allocation across the entire supply chain.
Automation in Packaging and Material Handling
Automation addresses some of the most labor-intensive parts of packaging and logistics. By harnessing robotics, modern conveyor systems, and advanced sensors, organizations can significantly reduce human error while accelerating throughput. Examples include:
- Automated packing lines that consistently measure and seal boxes to minimize mistakes and waste.
- Robotic arms that place parts into containers with near-zero error margins, decreasing damage rates.
- Automated guided vehicles (AGVs) or driverless forklifts that safely move containers and pallets through facilities.
- Robotic systems that handle repetitive tasks, allowing employees to concentrate on more strategic responsibilities.
Beyond labor savings, automating packaging lines boosts consistency by creating a standardized process that enhances product integrity, reduces worker injuries, and meets scaling demands without sacrificing quality. Many manufacturers integrate these systems with centralized data analytics to support continuous improvement initiatives based on real-time metrics and performance feedback.
Lightweight Packaging Materials Supporting Efficiency
In the automotive sector—where parts can be heavy and shipping footprints expansive—selecting lightweight yet robust packaging is a game changer. Modern materials like corrugated plastics, composite sheets, and specialized foam inserts provide efficient protection while keeping the total load weight low.
Incorporating lightweight packaging materials offers automotive businesses several advantages:
- Reduced freight costs due to a lower overall shipped weight.
- Lower fuel consumption in transit, which contributes to a reduced carbon footprint.
- More efficient handling that minimizes strain on workers.
- Flexible designs that can accommodate both large and small items without compromising durability.
Additionally, lightweight solutions often integrate seamlessly with automated systems. Easier lifting and movement widen the scope of robotic applications, simplifying transitions between different packaging configurations without excessive downtime.
Protective Packaging for Fragile and High-Value Components
Certain automotive parts—particularly electronic modules, hybrid batteries, or intricate mechanical assemblies—are vulnerable to even minor impacts or temperature fluctuations. Protective packaging is essential in these cases. Many automotive suppliers opt for designs that combine robust outer shells with shock-absorbing inner layers to mitigate external stresses:
- Foam inserts and air cells distribute force evenly to prevent localized damage to sensitive components.
- Textile dunnage envelopes items with durable fabric layers to prevent scratches or contamination.
- Multi-compartment container systems minimize part-to-part contact during transit.
Deploying such protective packaging can substantially reduce returns, replacements, and production downtimes, thereby preserving brand reputation and enhancing customer satisfaction.
Modular and Scalable Packaging Solutions
Automotive production can fluctuate significantly due to seasonal demand shifts, new model launches, or changes in global distribution. Modular and scalable packaging systems provide the flexibility to adapt packaging setups quickly without incurring excessive waste. Key characteristics of modular designs include:
- Interchangeable components—like adjustable dividers or stackable sections—that allow for easy reconfiguration.
- Cut-and-weld containers that can be resized or combined to accommodate evolving part dimensions.
- Collapsible or nestable containers that reduce storage space when not in use.
- Quick conversion between different shipping modes (e.g., sea freight, air cargo, or overland trucking).
By embracing modularity, manufacturers can ramp packaging operations up or down efficiently, reusing packaging assets in response to shifting demands. This approach minimizes idle inventory, keeps warehousing costs in check, and streamlines logistics across various regions.
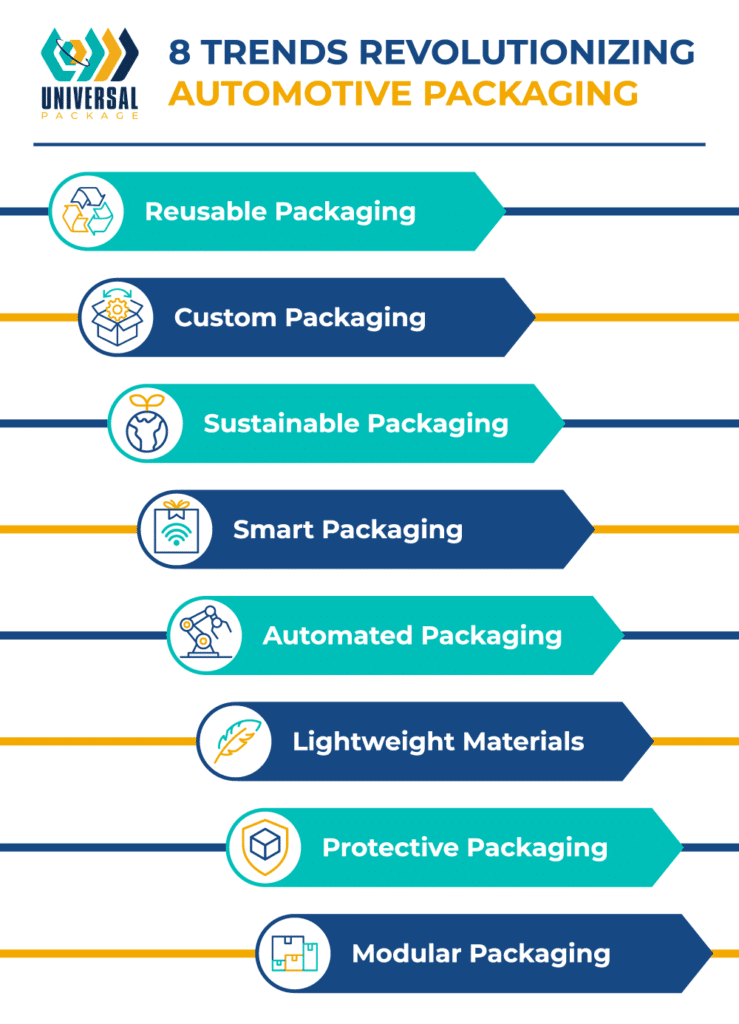
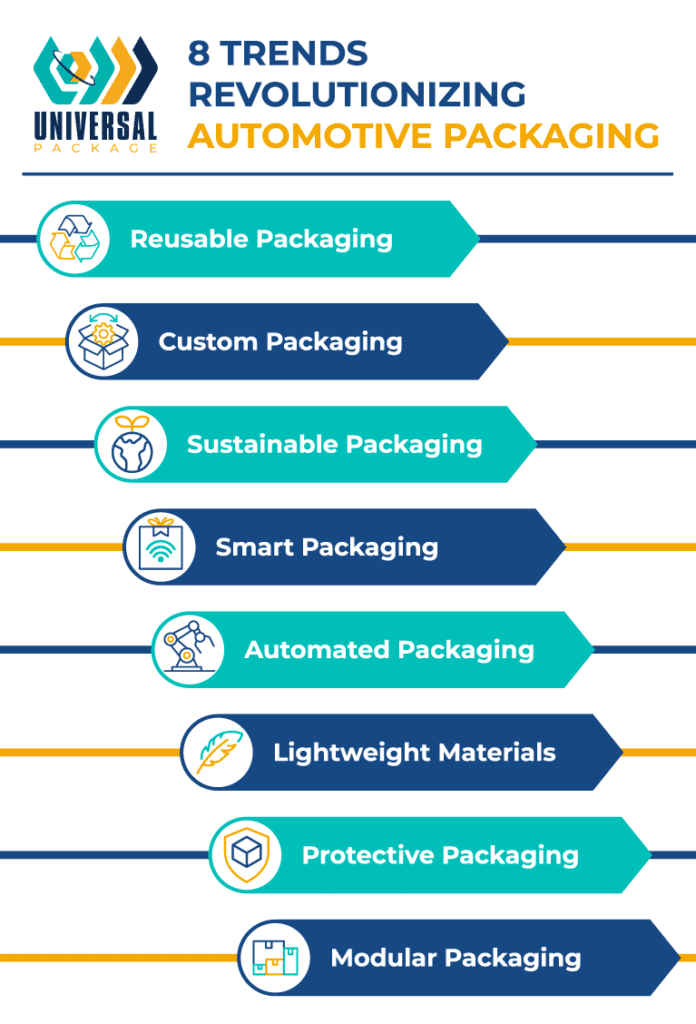
Embracing Cutting-Edge Packaging Innovations for a Sustainable Future
Packaging innovations in the automotive industry have rapidly evolved, tackling both operational challenges and sustainability goals. The eight trends highlighted here—from long-lasting reusable containers to data-driven smart packaging systems—represent the cutting edge of automotive packaging. Collectively, these trends help reduce product damage, optimize material usage, and support more agile supply chains.
Furthermore, forward-thinking manufacturers are exploring short-term or specialized options through lease and rental programs, partnering with packaging providers to manage fluctuating production volumes. Collaborative efforts among suppliers, logistics teams, and packaging specialists continue to drive improvements and integrate new technologies.
If you’re ready to enhance cost savings, boost efficiency, and improve environmental impact through advanced packaging solutions, consider exploring the offerings from Universal Package. With decades of experience in the industry, they assist automotive organizations in navigating complex requirements and crafting solutions that integrate seamlessly into existing workflows. For tailored consultations and pricing details, contact Universal Package today and discover how custom packaging solutions can propel your operations into a more sustainable, high-performing future.