Introducing Universal Package
Universal Package prides itself on delivering high-quality packaging solutions that align with our clients’ specific needs—be it standard or custom. With a strong emphasis on crafting designs and manufacturing packaging that snugly fits any product, our solutions are unparalleled in the industry. We have also amassed a wealth of experience in consultancy and project management, further enhancing the value we offer to our clients.
Our proficiency extended into the automotive sector, with robust industry knowledge and experience serving as our guiding light. We believe in diving deep into our clients’ needs, understanding their industry-specific hurdles, and innovating within those boundaries. A case in point is a northern Indiana-based manufacturer of automotive parts—a customer with a distinct set of problems and a need for our singular expertise.
Capturing the Core of the Problem
An automotive parts manufacturer based in the northern regions of Indiana found themselves at the heart of customer complaints involving the poor performance of fuel rail systems destined for an engine assembly plant in Mexico. Prompted by the complaints, a complex corrective action investigation was put into motion. This initiative unearthed the unexpected – plastic caps, an essential part of the packaging process, were inadvertently decelerating the performance of the fuel rail system.
The complex, original packaging process involved various elements, including a corrugated half-slotted box, an interior partition, a custom die-cut corrugated tray to secure the fuel rails, and a whopping 32 plastic caps. The latter, despite their protective function, morphed into an unanticipated problem. The caps were inserted over the tips of fuel injectors to eliminate dust contamination and damage to highly fragile injector tips but were not being removed during the engine assembly process. This resulted in the fuel being blocked by the caps. Universal Package was consequently entrusted with redesigning the packaging to eliminate these plastic caps which had been flawed from the onset.
The Potential Roadblocks: Retaining Box Size and Keeping Dust at Bay
The client’s demands presented two clear challenges. First, the new packaging should retain the dimensions and unit load of the original corrugated box.
The original packaging consisted of a corrugated expendable half-slotted box measuring 23” x 21” x 10”, an interior corrugated partition, a die cut corrugated tray to hold fuel rails in place, and 32 plastic caps. The boxes were stretch wrapped to a wood pallet measuring 48” x 45”. The density of the individual cartons was 4 parts per carton. The unit load consisted of 4 cartons per layer, 4 layers high totaling 16 cartons per unit load, for a total of 64 fuel rails per unit load. This required adventurous ideation from the Universal Package team, culminating in the critical balance of space and the all-important safety of the rail systems.
The second challenge was the imminent threat of dust contamination, necessitating the need for rails to be kept away from anything likely to release dust particles, including Corrugated partitions, trays, and other paper interiors.
Considering and Rejecting the Idea of Returnable Packaging
The practicality of returnable packaging was tested during the problem-solving process, but it ultimately wasn’t a viable route due to the Mexican government’s imposition of export taxes on pack returns to the United States. The client needed a one-shot approach, which meant the design of a completely new, expendable packaging solution.
The Universal Solution: Reinvented Packaging Design
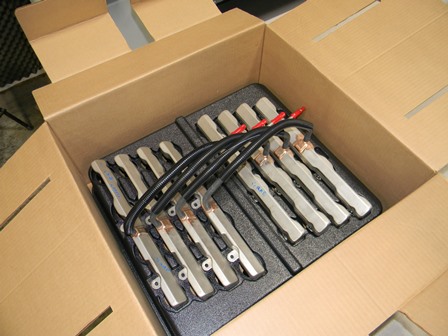
In response to the client’s challenges, Universal Package innovatively redesigned a new corrugated box, maintaining similar dimensions to the original. Notably, this inventive design incorporated a thin wall ABS plastic thermal formed tray, replacing both the problematic plastic caps and the previously utilized corrugated partitions and die-cut tray. This change resulted in an ingenious two-in-one packaging solution.
The new design, containing a common poly bag to hold 1 tray per 4 parts, efficiently resolved multiple issues. It virtually eliminated paper dust contamination, providing a more secure fit for the parts, and simultaneously removing the need for the troublesome plastic caps. The introduction of hold-down flaps to the top of the redesigned box added to its efficacy, eliminating the need for the interior die-cut tray while also making the layer trays redundant.
Throwing Light on Real-life Testing and Implications
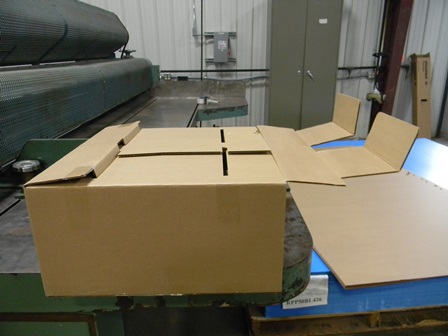
Universal Package left nothing to chance. The team commissioned a prototype tool for the new ABS trays and carton samples. They were subjected to robust testing in an independent packaging lab followed by real-world stress tests. These tests involved shipping unit loads to Texas and back to the manufacturer. The results were unquestionably successful with no issues of damage, contamination, or otherwise arising.
Key Outcomes: Boosted Efficiency, Slashed Costs, and Resolved Dilemmas
The new packaging solution proved to be more efficient and cost-effective, shaving labor costs and unnecessary product wastage. By negating the need for layer trays, interior die-cut trays, and plastic caps, costs were significantly reduced. But most importantly, the new design successfully eliminated the problem at its root, clearing the path for smooth operations. In conclusion, Universal Package not only complied with the client’s requirements but also crafted a creative, optimal solution that saved on cost and improved efficiency.