When it comes to protecting your products during transport or storage, choosing the right packaging material is crucial. Foam packaging offers a versatile and effective solution to keep items safe from damage, but with various types available, selecting the perfect one can be a daunting task.
This guide aims to demystify the process, providing you with the insights you need to make an informed decision tailored to your product’s specific needs.
From understanding the insulating qualities of foam to considering its environmental impact, we’ll explore the different foam materials such as polyethylene, polyurethane, and polystyrene, and their unique benefits. Whether you’re a supply chain professional, a procurement manager, or involved in production, this how-to guide will equip you with the knowledge to design foam packaging that combines protection, sustainability, and cost-effectiveness.
The Fundamentals and Applications of Common Foam Packaging Materials
Foam packaging materials, with their lightweight, cellular structures derived from polymers, hold a crucial role in the packaging sector. These materials, available in sheets, rolls, and custom-molded inserts, offer a diverse variety catering to diverse packaging needs. The most popular types of foam materials in packaging encompass polyethylene, polyurethane, and polystyrene.
Polyethylene and Cross link Foam
Polyethylene foam, or PE foam, is a robust contender in this realm, known for its closed-cell, lightweight nature, and remarkable cushioning and shock-absorption qualities. Its resistance to moisture and chemicals, combined with its range of densities, gives it an edge in safeguarding products exposed to stringent environmental conditions during transit or storage.
Cross-link Foam is chemically cross-linked polyethylene foam. It is an extremely fine-celled foam, ideal for projects and applications that require thicker foam. With a smooth, cushioned feel, combined with superior physical and chemical properties, cross-linked polyethylene foam is the solution for an array of applications that demand thicker sections of closed-cell foam. With its closed-cell density, XLPE works well for many packaging applications and is Class-A protective. Cross link foam can be die cut, water jet cut and routed and comes in a wide variety of densities, from a 2# which is very cushioning up to 8# or more which is very structurally sound as well as protective.
Cross link Foam can be sheeted very thin and used as a lamination on plastic corrugated, up to 12” thick blocks used to house products.
Long-term storage, transportation, and industrial applications have also embraced polyethylene foam for its capacity to protect heavy items and its customizable attributes promoting product-specific packaging and ecological solutions.
Polyurethane Foam
However, polyurethane foam flaunts flexibility and a unique soft texture, gaining favor for its outstanding shock absorption capabilities. Its resilience allows it to regain its original shape swiftly post-compression, making it ideal for products vulnerable to drops or vibrations. Furthermore, it can be seamlessly molded into custom shapes, proving beneficial for products with singular shapes and sizes.
Various industries, especially those handling electronics, medical devices, furniture, and household goods, use polyurethane foam for its versatility and high resistance to abrasion.
Polystyrene Foam
Polystyrene, or styrofoam, celebrated for its insulation abilities and lightweight properties, stands as a go-to option for shipping lightweight goods requiring temperature insulation. Despite environmental concerns associated with traditional styrofoam, it maintains its popularity for effective temperature-sensitive product protection.
However, the industry’s drive towards sustainability has resulted in alternatives such as expanded polystyrene (EPS) and biodegradable polystyrene. These promising successors possess the typical features of polystyrene but offer added benefits as they are biodegradable and recyclable, significantly curbing their environmental footprint.
Benefits of Using Foam for Packaging (or Unpacking the Multitude of Advantages Offered by Foam Packaging)
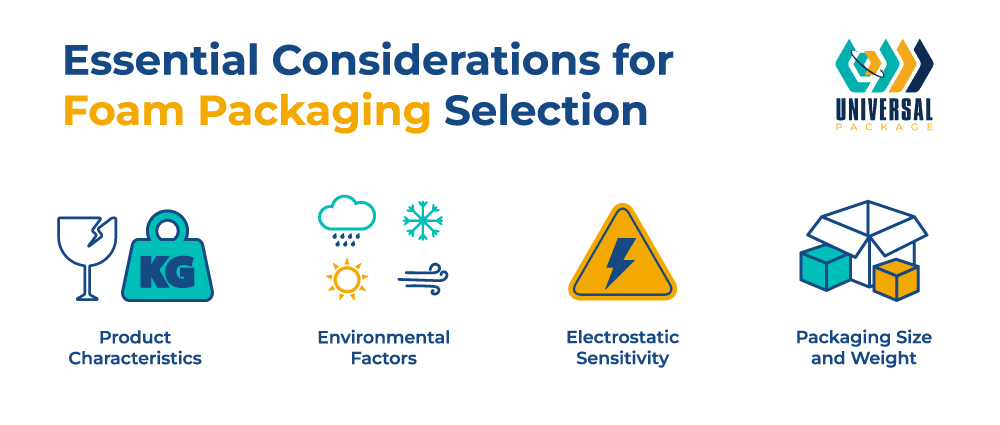
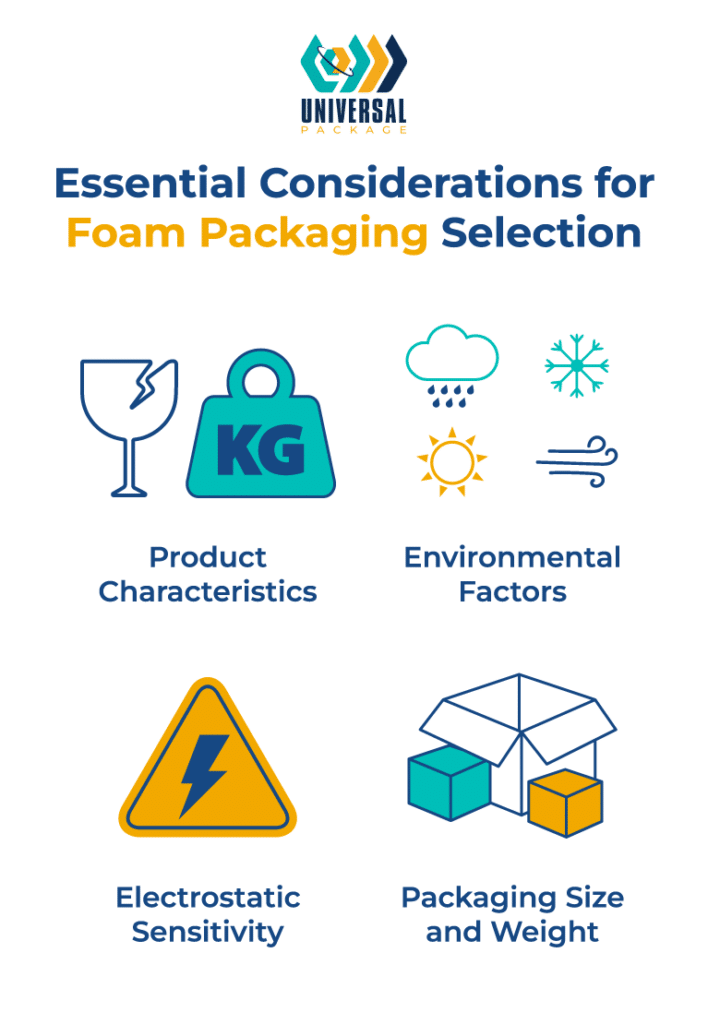
The use of foam for packaging brings a host of benefits steeped in protection, cost-effectiveness, and sustainability. Here are some of the key advantages that enhance its value in the packaging sector:
Exceptional Cushioning and Shock Absorption
Foam packaging safeguards the contents impeccably through the shipping and handling process with its superior cushioning characteristics. It’s adept at absorbing shock and impact, eliminating the stress of transit, especially crucial for delicate or fragile items that mandate extra care to evade breakage.
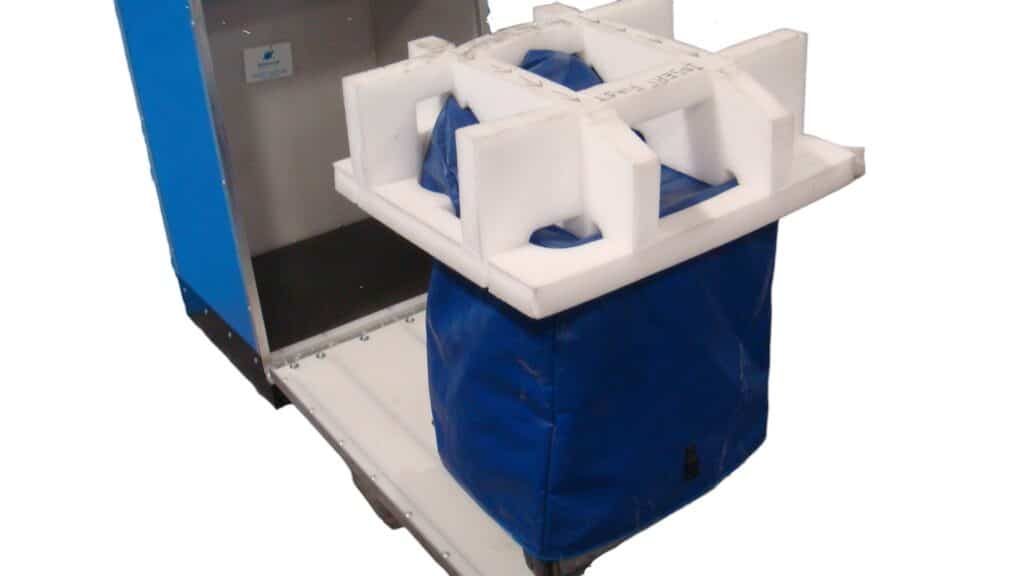
Lightweight Nature
The remarkable lightweight quality of foam packaging contributes significantly to reducing overall shipping costs. As transportation fees often rely on package weight, utilizing foam can lead to substantial savings, particularly important for businesses that operate with high-volume product shipments.
Insulating Properties
The insulating features of foam make it an optimal choice for temperature-sensitive goods. By maintaining a stable environment, foam packaging prevents spoilage or damage resulting from exposure to heat or cold, which establishes it as a favored choice for shipping perishable items like food and pharmaceuticals.
Customizability
Foam packaging materials exhibit high customizability, accommodating products of diverse shapes, sizes, and weights. Its flexible nature makes foam an ideal choice for a vast range of products – from electronics and medical supplies to delicate home decor items.
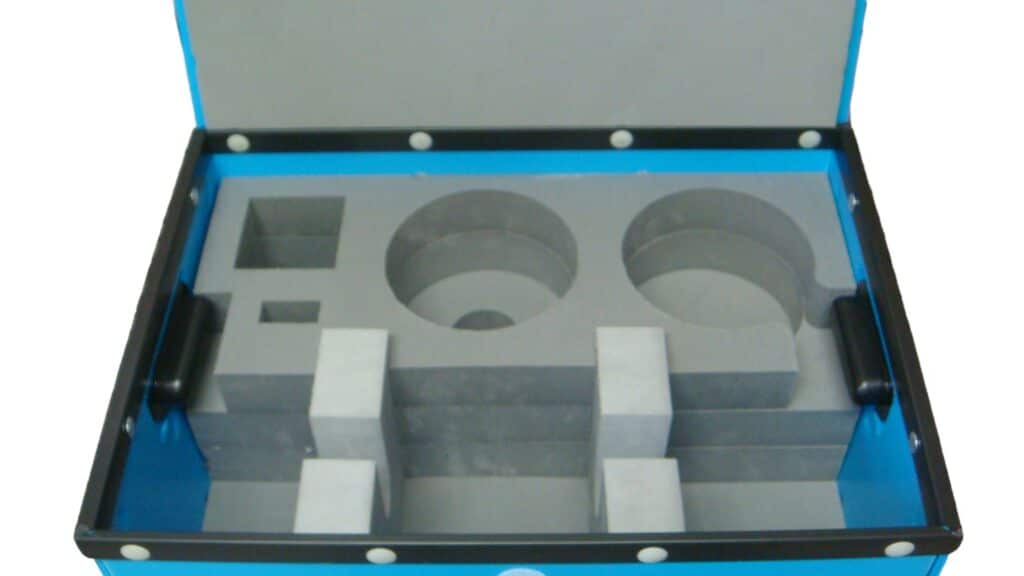
Cost-Effectiveness and Environmental Friendliness
Foam packaging offers excellent cost-effectiveness, making it an attractive packaging choice for businesses aiming to cut costs without compromising on quality. Its lightweight attribute also aids in reducing fuel consumption and carbon emissions during transport, framing it as a greener choice.
All in all, with such myriad benefits, foam packaging stands as a reliable and versatile choice for robust product protection during shipping and storage.
Key Factors to Consider when Selecting Foam Packaging
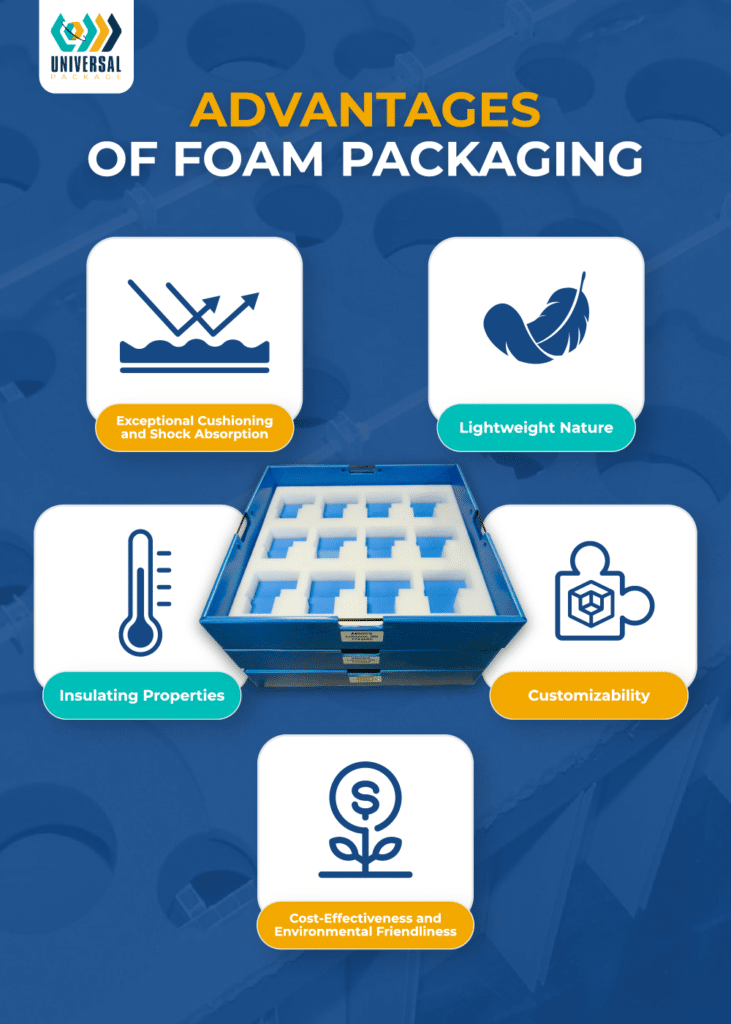
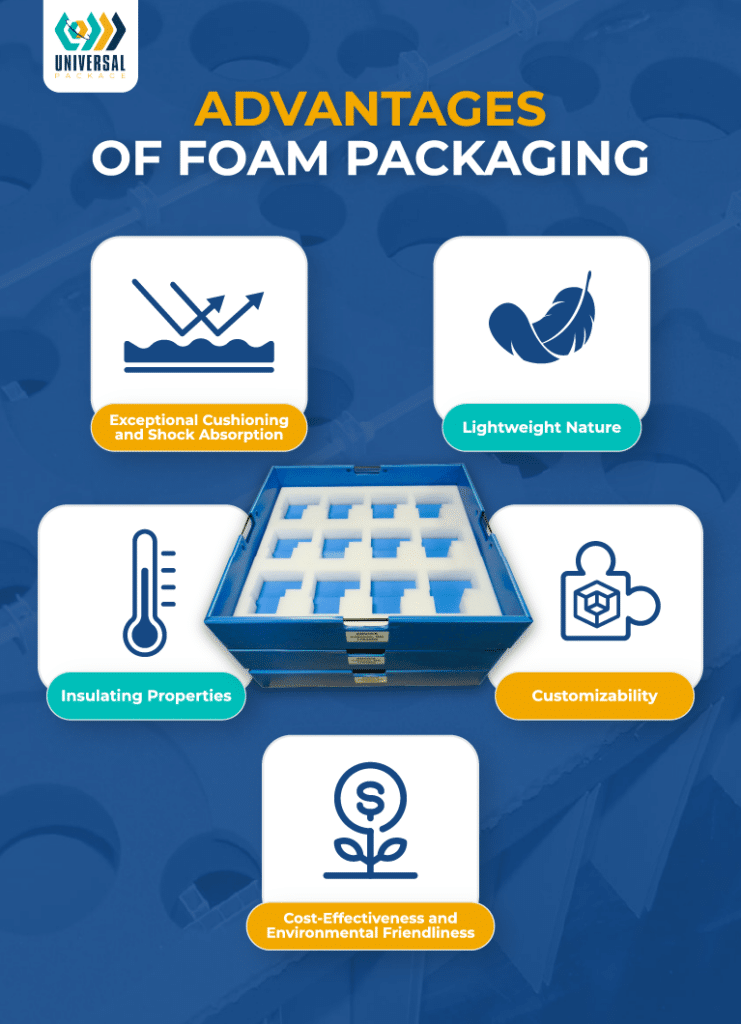
Choosing the right foam packaging calls for a well-considered evaluation that prioritizes the product’s characteristics. It’s a process that requires careful planning and attention to detail, considering key factors such as product characteristics, environmental factors, electrostatic sensitivity, and packaging size and weight.
Product Characteristics
Central to this process is understanding the product’s fragility and weight as they dictate the density and thickness of the protective foam. If a product is vulnerable to damage from falls or vibrations, a foam of higher density might be the right choice for its potent shock-absorption capabilities.
Environmental Factors
Environmental factors during shipping and storage warrant considerable attention when choosing foam packaging. If there’s a probability that the product may be exposed to elements like moisture, extreme temperature variations, or chemicals, it’s essential to select foam material that’s resilient to these conditions. Ensuring your foam can withstand these environmental stresses helps guarantee that the packaging choice aptly suits the product’s particular needs and the hurdles it may face during transit and storage.
Electrostatic Sensitivity
When dealing with products sensitive to static electricity, it becomes exceedingly important to select an anti-static foam packaging. Static electricity can cause significant damage to certain products, and this specific type of foam packaging is crucial for preventing potential harm caused by electrostatic discharge. A thorough assessment of the product’s static sensitivity can help ensure the foam packaging material chosen provides suitable protection against electrostatic risks.
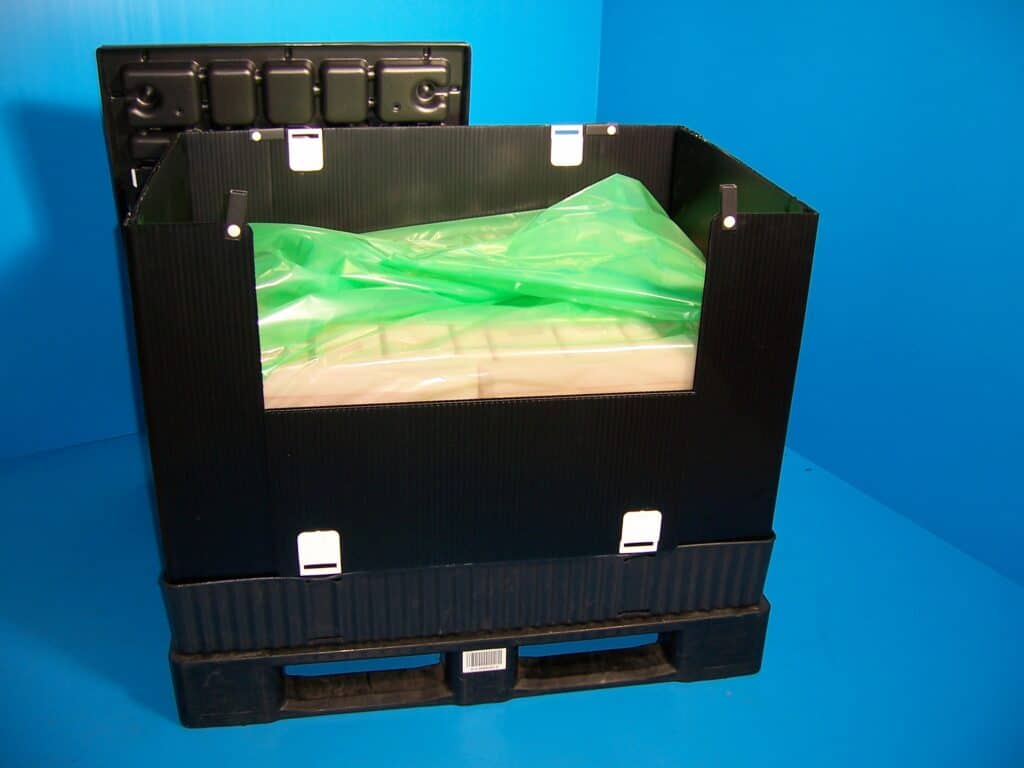
Packaging Size and Weight
The size and weight of the package itself also deserves attention, considering their impact on shipping costs. More voluminous or heavier packaging necessitates more foam material, leading to an increase in overall costs. By comprehending these determinants, businesses can strike a balance between effective product protection and cost-efficiency, resulting in sustainable and highly effective foam packaging solutions.
Environmental Impact and Sustainability Options
Foam packaging, while effective for protection, has faced scrutiny due to its environmental impact. Traditional foam materials can take centuries to decompose, posing a challenge for waste management and sustainability. In response, the industry has been exploring alternative materials and innovative solutions to mitigate these concerns.
Eco-friendly foam packaging options are gaining traction as businesses seek to reduce their carbon footprint. Biodegradable foams, made from plant-based materials, decompose more quickly and minimize environmental harm.
Additionally, some companies are adopting recycled foams, which make use of post-consumer waste, contributing to a circular economy. To further support sustainability efforts, businesses can educate customers on how to recycle foam packaging correctly, ensuring it doesn’t end up in landfills unnecessarily.
Custom Foam Packaging Solutions
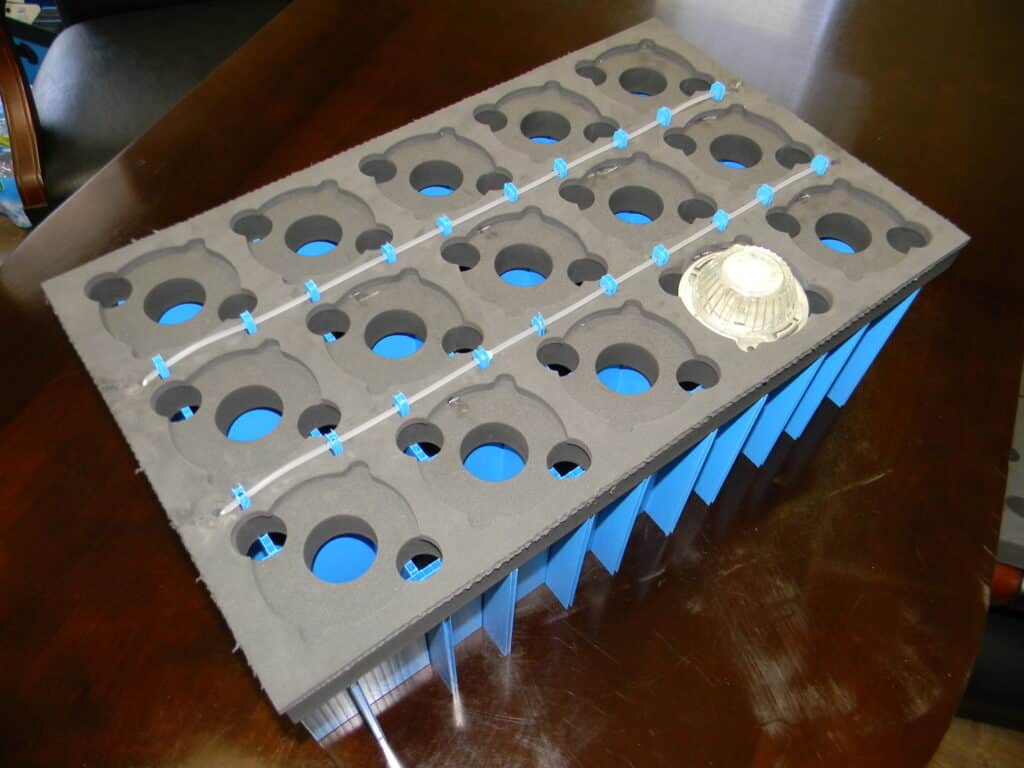
Custom foam packaging solutions are indispensable when dealing with products that have unique shapes, are exceptionally fragile, or require precise placement within their packaging. These customized inserts cradle items securely, preventing movement and providing tailored cushioning where it’s needed most.
The process of creating custom foam packaging often involves detailed assessments of the product’s dimensions, weight, and vulnerability to damage, ensuring a perfect fit and optimal protection during transit. Custom foam packaging inserts not only protect products but also provide an aesthetically pleasing packaging solution, enhancing brand image and customer satisfaction. This level of customization can also reduce the need for additional packaging materials, streamlining the packaging process and reducing waste.
Factors influencing the design of custom foam packaging can include the product’s size, shape, and the level of protection required. Designers may use computer-aided design (CAD) software to model the foam inserts accurately, while advanced cutting technologies such as waterjet or die-cutting are employed to produce the foam with precision.
Real-world examples demonstrate the effectiveness of custom foam packaging, such as electronics encased in precision-cut polyurethane or medical equipment secured in high-density polyethylene, underscoring the value of a bespoke approach to packaging design.
Foam Packaging Design Guide
Foam packaging design begins with understanding the specific needs of the product it’s intended to protect. This involves analyzing the product’s size, shape, and fragility to determine the right type and amount of foam. The design process should ensure that the foam packaging snugly secures the product, minimizing movement and the potential for damage during transit. It’s critical to select a foam material that not only fits the product but also provides adequate cushioning and support.
To ensure the foam packaging performs as expected, testing is an essential step. Simulated transit tests, such as drop tests, vibration tests, and compression tests, help evaluate the resilience and protective qualities of the foam design. These tests can reveal potential weaknesses before the product is shipped, allowing for design adjustments that enhance safety and reliability.
For businesses without in-house testing capabilities, partnering with a professional design service can offer access to specialized testing equipment and expertise, ultimately leading to a more secure and effective foam packaging solution. By partnering with experts in foam packaging design, businesses can also tap into the latest materials and techniques, leveraging innovation to optimize product protection and sustainability.
Click Here to Learn About the Custom Packaging Options from Universal Package
It's worth taking the time to carefully consider and select the most suitable packaging for your fragile products. Learn about our custom product capabilities.
Partnering with Universal Package for Your Foam Packaging Needs
Universal Package stands at the forefront of foam packaging solutions, offering a wealth of expertise and experience to businesses seeking reliable and efficient packaging options. With a deep understanding of the diverse needs across various industries, Universal Package tailors its approach to meet the specific requirements of each client, ensuring the highest level of product protection and packaging performance.
Custom design and engineering services are a cornerstone of Universal Package’s offerings. Whether clients require standard packaging options or intricate, custom-designed solutions for uniquely shaped or fragile items, the team at Universal Package is equipped to deliver. Utilizing advanced design tools and materials, they work closely with businesses to develop foam packaging that aligns with their objectives and logistics demands.
For those interested in exploring the possibilities of foam packaging with Universal Package, the company invites inquiries and consultations. With a collaborative and consultative approach, Universal Package works with clients every step of the way to develop foam packaging that satisfies their unique needs. Contacting Universal Package opens the door to a partnership that prioritizes innovation, customer service, and a commitment to excellence in protective packaging solutions.
Crafting Your Ideal Foam Packaging Solution: Connect with Universal Package Today
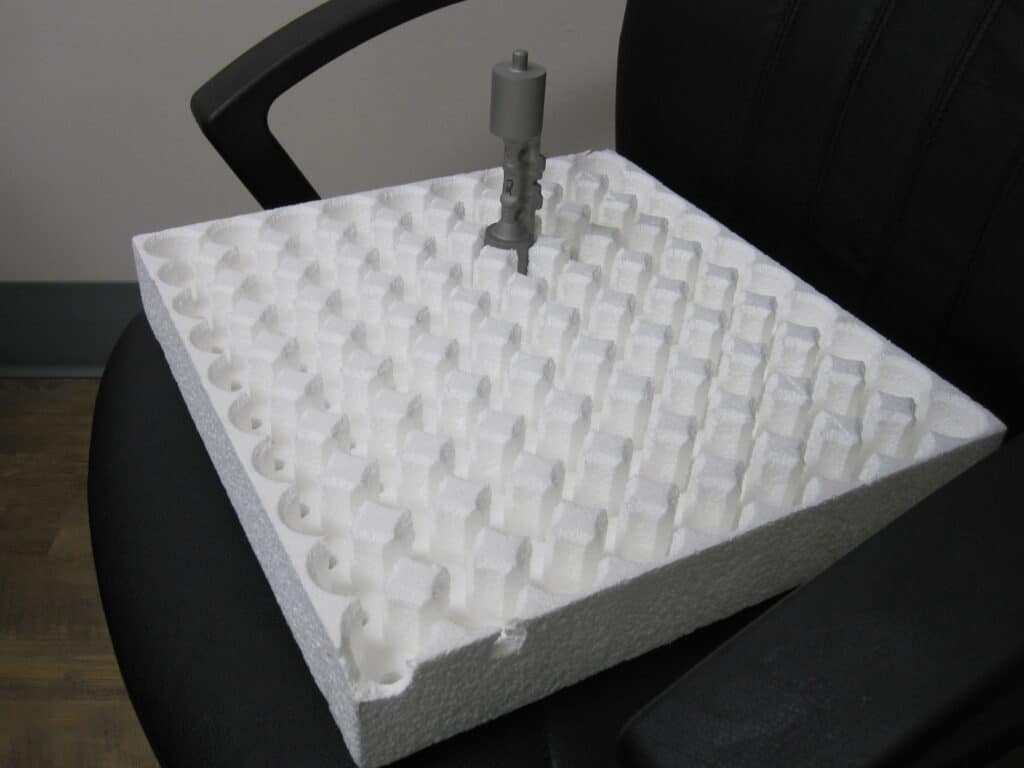
With the myriad of options and considerations laid out in this guide, selecting the right foam packaging material may seem daunting. Yet, the choice becomes simpler when you partner with a trusted provider who understands your unique needs. Universal Package stands ready to lend our expertise in designing and manufacturing foam packaging that promises the utmost protection for your products.
We know that protecting your products is a top priority for you and it’s our goal to design foam packaging solutions that meet or exceed these expectations. Our tailored approach ensures your items are securely wrapped in the most suitable foam material, reducing your shipping costs and environmental footprint while safeguarding your valuable products.
I invite you to reach out to us for a personalized consultation. Together, we can create a packaging strategy that aligns with your product specifications, budget, and sustainability goals. Let us help you enhance your packaging process with solutions that are as innovative as they are effective. Contact Universal Package today and let’s package your success.