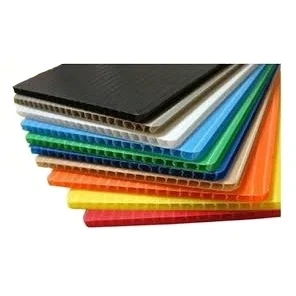
In the world of product manufacturing, the choice of packaging material is as crucial as the product itself. This blog post will delve into two popular types of packaging plastics – polyethylene and polypropylene, comparing their properties, uses, and suitability for different packaging needs. If you’re a manufacturer, wholesaler, or exhibitor looking to make informed decisions about your packaging materials, particularly in the food industry, this comprehensive guide is for you. We will also introduce you to the range of packaging solutions provided by Universal Package, your trusted partner in the packaging industry. Let’s dive in and explore the world of polyethylene and polypropylene packaging.
Understanding Polyethylene and Polypropylene
Polyethylene, often referred to as PE, is a versatile plastic with a wide range of applications. It is known for its high ductility, impact resistance, and low frictional properties. This thermoplastic polymer is made through the polymerization of ethylene, a colorless gas derived from petroleum and natural gas. PE is available in various densities, including high-density polyethylene (HDPE) and low-density polyethylene (LDPE), each with their unique properties and uses.
On the other hand, Polypropylene, also known as PP, is another widely used plastic, particularly renowned for its heat resistance, elasticity, and strength. It is a semi-crystalline thermoplastic produced through the polymerization of propylene. Apart from its excellent physical properties, PP is also resistant to many chemical solvents, bases, and acids, making it suitable for a variety of applications in the packaging industry.
Comparing Polyethylene and Polypropylene
Polyethylene and polypropylene, both belonging to the family of polyolefin resins, share some basic characteristics. They are both lightweight, chemically resistant, and durable, making them ideal for a variety of packaging applications. Additionally, both polyethylene and polypropylene are cost-effective and recyclable, contributing to their widespread use in packaging across various industries.
However, despite their similarities, these two types of plastics have distinct differences that set them apart. Polyethylene is more flexible and softer to the touch, whereas polypropylene is rigid and has a higher melting point. Polyethylene, on the other hand, is known for its excellent moisture barrier properties, making it ideal for packaging products that need to be dry.
In terms of transparency, polypropylene is generally clearer and provides better product visibility, while polyethylene tends to be translucent or opaque. This can influence the aesthetic appeal of the packaging, which could be crucial for certain product presentations.
Detailed Analysis of Polyethylene
Polyethylene is one of the most commonly used packaging plastic materials, renowned for its versatility. From a chemical perspective, it’s a polymer-based material made from ethylene monomers. It’s characterized by its long chains of carbon and hydrogen atoms, giving it distinct properties.
Polyethylene has a low melting point, which means it can be easily shaped and molded into various forms. This makes it an excellent choice for a wide range of packaging applications. It’s also resistant to most acids, bases, and organic solvents, making it suitable for packaging products that may contain or be exposed to these substances.
In terms of advantages, Polyethylene is lightweight, cost-effective, and flexible, making it ideal for creating a variety of packaging solutions. It also exhibits excellent barrier properties, protecting contents from moisture, dust, and other environmental factors.
However, Polyethylene is not without its drawbacks. While it is highly durable and resistant to impacts, it can be susceptible to UV light, which can cause it to degrade over time. Its low melting point, while useful for molding purposes, also means that it can deform under high temperatures.
Polyethylene uses in Industrial Packaging
Polyethylene is widely used in the industrial packaging industry due to its versatile properties. Here are some common industrial packaging applications where polyethylene is used:
- Bags and Liners: Polyethylene bags and liners are used to pack and protect a wide range of industrial products, including chemicals, powders, granules, and liquids. They provide a barrier against moisture, dust, and contaminants, ensuring the integrity of the packaged goods.
- Foam Packaging: Polyethylene foam is used for cushioning and protecting fragile and sensitive industrial products during transportation. It provides excellent shock absorption and impact resistance, reducing the risk of damage.
- Tubing and Sheeting: Polyethylene tubing and sheeting are used for various industrial packaging applications, such as wrapping, covering, and protecting large objects or equipment. They can be easily customized to the required dimensions and provide a protective barrier.
- Drum Liners: Polyethylene drum liners are used to line industrial drums and containers, providing a clean and protective barrier for storing and transporting liquids, powders, and chemicals. They prevent contamination and leakage, ensuring the integrity of the contents.
- Industrial Pouches: Polyethylene pouches are used for packaging industrial products that require individual packaging, such as small parts, hardware, fasteners, and electronics. They provide protection from moisture, dust, and damage during storage and transportation.
- Protective Covers: Polyethylene protective covers are used to protect large industrial machinery, equipment, and components from dust, moisture, and environmental factors. They can be customized to fit specific dimensions and provide a protective barrier.
Overall, the versatility, durability, and protective properties of polyethylene make it a popular choice in the industrial packaging industry. Its ability to provide moisture resistance, impact protection, and ease of customization make it suitable for a wide range of packaging applications.
Detailed Analysis of Polypropylene
Polypropylene, often abbreviated as PP, is a thermoplastic polymer that is recognized for its strength, clarity, and resistance to heat and chemicals. It is a linear hydrocarbon polymer, expressed as CnH2n, with the ‘n’ referring to the number of carbon atoms in the backbone. Its molecular structure gives it a unique property of being semi-rigid and resistant to fatigue.
One of the key advantages of using polypropylene in packaging is its high durability and resistance to fatigue. This makes it ideal for packaging products that need to withstand transportation and handling. Additionally, its high melting point makes it suitable for packaging products that are subject to heat during their lifecycle. However, its resistance to UV radiation is lower than other plastics, which means it can degrade if exposed to sunlight for prolonged periods. This is a disadvantage that needs to be considered when using it for outdoor applications.
Polypropylene is widely used in a variety of packaging applications due to its versatility. It is also used in industrial packaging due to its high chemical resistance. It’s important to note that the use of polypropylene in packaging is governed by certain regulations and standards, especially when used for medical applications, to ensure the safety of the end-users.
Polypropylene uses for Industrial Packaging
Polypropylene is widely used in industrial packaging due to its excellent chemical resistance, durability, and versatility. Its unique properties make it suitable for a variety of applications across different industries.
One of the primary uses of polypropylene in industrial packaging is for storing and transporting chemicals and hazardous materials. Polypropylene containers, drums, and intermediate bulk containers (IBCs) are commonly used to safely store and transport chemicals, oils, lubricants, and other industrial fluids. Polypropylene’s resistance to a wide range of chemical solvents, bases, and acids ensures the integrity of the packaging and prevents any leakage or contamination.
Polypropylene is also used in the packaging of automotive components and parts. Its resistance to oils, greases, and other automotive fluids makes it suitable for packaging components that require protection during storage and transportation. Polypropylene trays, containers, and bins are commonly used to organize and protect automotive parts such as filters, gaskets, and small components.
In addition to its chemical resistance and durability, polypropylene is also known for its heat resistance. This makes it suitable for packaging products that require heat sealing or sterilization processes. Polypropylene pouches are commonly used in the packaging of medical devices and pharmaceuticals. These materials can withstand high temperatures during the sealing process, ensuring a secure and tamper-proof package.
Overall, polypropylene’s chemical resistance, durability, and heat resistance make it a popular choice for industrial packaging. Its versatility allows it to be used in a wide range of applications, providing reliable and cost-effective packaging solutions for various industries.
Making the Right Choice: Factors to Consider
Product type and needs should be the first consideration when choosing between polyethylene and polypropylene packaging. Each material has its strengths. For instance, polyethylene’s flexibility makes it suitable for packaging with a need for durability and impact resistance, while polypropylene’s rigidity and high melting point make it ideal for packaging products that require heat resistance.
Cost-effectiveness is another critical factor to consider. Polyethylene is generally less expensive than polypropylene. However, the total cost should not only account for the initial price but also the long-term durability and the potential need for replacement.
Lastly, consider the environmental impact of your packaging material. Both polyethylene and polypropylene are recyclable, but their recycling rates vary. Polyethylene tends to have a higher recycling rate, making it a more environmentally friendly option. However, advancements in polypropylene recycling technology are closing this gap.
Universal Package’s Solutions
Selecting the right packaging material for your product is a crucial step in the packaging process. At Universal Package, we make this process easier by providing expert guidance and support. Our team of professionals conducts a thorough analysis of your product needs and recommends the most suitable packaging material. This process is driven by factors such as product type, cost-effectiveness, and environmental impact, ensuring that you make an informed and optimal choice for your packaging needs.
Choosing the right packaging material for your product is essential to ensure customer satisfaction. Knowing what suits your product type, cost-effectiveness, and environmental impact are key factors to consider. Universal Package is here to guide you through this decision-making process. With a range of polyethylene and polypropylene packaging solutions tailored to meet your unique requirements, our experts ensure that your products are safe, secure, and well-presented. Let’s start a conversation today about your packaging needs and make the smart choice together.