Selecting a packaging vendor is a pivotal decision for businesses in specialized industries such as appliance, automotive, electronics, medical, military, and pharmaceutical sectors. The choice of vendor can significantly impact not only the safety and integrity of products but also the efficiency of supply chain operations. In this blog post, we will explore the essential attributes that businesses should consider when choosing a packaging vendor, ranging from the quality of materials and customization options to industry experience and customer support.
1) Quality of Materials
Selecting the right packaging vendor involves careful consideration of various factors, including the quality of the materials used. High-quality materials are crucial for ensuring the durability and effectiveness of packaging solutions, ultimately protecting products during shipping and handling.
Importance of High-Quality Materials
The materials used in packaging directly impact the protection your products receive. High-quality materials can withstand the rigors of transport, reduce the risk of damage, and maintain the integrity of the contents. Furthermore, superior materials enhance the handling efficiency, enabling easier and safer loading, unloading, and storage.
Impact on Product Protection and Handling Efficiency
Using robust materials in packaging solutions minimizes the chance of product damage during transit, which is especially important in industries such as electronics, pharmaceuticals, and automotive. Efficient handling supported by quality materials also speeds up operation processes, potentially reducing labor costs and time spent on manual handling.
Examples of Materials Used in Industrial Packaging
Different industries may require specific types of materials suited to their unique needs. Here are a few commonly used materials in industrial packaging:
- Corrugated Fiberboard: Lightweight yet strong, ideal for a wide range of products.
- Plastics: Versatile and durable, plastics are used for both primary and secondary packaging.
- Metals: Such as aluminum and steel, used for heavy-duty or sensitive equipment.
- Foam: Provides excellent cushioning and is often used in packaging delicate electronic components.
- Wood: Ideal for heavy-duty or irregularly-shaped products.
By prioritizing the quality of packaging materials, businesses can significantly enhance the safety and efficiency of their product handling and transportation.
2) Customization Options
While standard packaging solutions have their place, businesses often need customized packaging to meet their specific product and logistical needs. Partnering with vendors that offer comprehensive customization options can help businesses address these unique challenges and maintain consistency and quality in their packaging operations.
Benefits of Customizable Packaging Solutions
Customized packaging solutions offer numerous advantages. First, they ensure that products are snugly and securely packed, reducing the risk of damage during transit. This is particularly important in industries where goods are delicate or hazardous. Secondly, tailored packaging can significantly enhance brand perception by aligning the packaging design with corporate branding and aesthetics, thereby enhancing customer experience and satisfaction.
Available Customization Options
Packaging vendors typically offer a wide range of customization options to address specific logistical and branding needs. These include:
- Size Customization: To accommodate products of any size and shape.
- Material Choice: Options like sturdy cardboard, flexible plastics, or eco-friendly materials to match product needs and sustainability goals.
- Design Customization: Including logo placement, color schemes, and structural design, which are essential for brand recognition and consumer appeal.
Meeting Specific Customer Needs
The capacity to adapt packaging solutions as per the unique requirements of a business is what sets a vendor apart. This involves more than just physical adjustments; it means understanding the client’s market, the sensitivities of their products, and the most effective ways to enhance product visibility and protection. Whether it’s creating compact packaging to reduce shipping costs or developing robust packages for heavy machinery, customization plays a pivotal role in addressing these precise needs effectively.
In essence, selecting a vendor that offers comprehensive customization options is indispensable for businesses looking to maintain product integrity, elevate customer satisfaction, and uphold brand identity through their packaging solutions.
Christopher
Manufacturing Engineer
3) Industry Experience
The experience of a packaging vendor is a critical aspect to consider when selecting a partner for your business. A vendor with a diverse portfolio of clients across industries can offer valuable insights and expertise in addressing varied packaging needs and challenges.
Depth of Knowledge
A vendor that has served multiple sectors understands the logistical, environmental, and compliance challenges unique to each. This multifaceted experience means they can efficiently troubleshoot potential issues and adapt quickly to industry-specific requirements. For instance, a vendor familiar with the pharmaceutical industry will know the importance of moisture control and tamper-evident packaging, which might be less critical in the automotive sector.
Compliance with Industry Standards
Each industry has its own set of standards for safety, quality, and environmental impact. A packaging vendor with broad industry experience will be more likely to have an in-depth understanding of these standards and how to meet them. For instance, packaging for military use often needs to meet stringent durability tests and lightweight specifications, which might not be as critical in consumer electronics.
Industry-Specific Solutions
Experienced vendors often offer tailored solutions that address particular challenges of diverse industries. These vendors have a toolkit of varying materials, designs, and prototypes tested across sectors, enabling them to offer sophisticated and industry-specific solutions swiftly. Whether it’s shock-proof packaging for delicate electronics or sterile, contaminant-free packaging for medical devices, a seasoned vendor can provide optimized packaging solutions that newer market players might not.
By evaluating a vendor’s experience across various industries, businesses can gauge their ability to deliver informed, efficient, and compliant packaging solutions that address specific operational needs. Selecting a vendor with comprehensive industry experience can lead to enhanced product safety, better regulatory compliance, and more efficient packaging operations, aligning well with the overall strategic goals of a business in any field.
4) Customer Support
Choosing the right packaging vendor goes beyond just the products they offer; it significantly depends on the quality of customer support provided. Effective support ensures any issues are resolved quickly, minimizing downtime and potential disruptions in the supply chain. Moreover, a vendor capable of offering comprehensive consultations reflects their commitment to tailor solutions specifically to your business needs.
Key Support Services
Here are some critical examples of support services you might expect from a top-notch packaging vendor:
- Consultation and Customization: An initial comprehensive discussion about your packaging needs, assessing aspects from design to logistics, ensures the solutions are tailored precisely for your operations.
- Troubleshooting and Problem Resolution: Quick and efficient handling of any issues that arise after delivery. This could range from damaged packaging materials to logistical bottlenecks.
- Training and Guidance: Providing training for your staff on how to best use and handle the packaging materials can greatly enhance efficiency and safety.
The Benefits of Ongoing Support
Continuous customer support pays off in multiple ways for your business. Here’s how:
- Enhanced Efficiency: With reliable support, you can streamline your packaging operations by reducing the time spent dealing with product-related issues.
- Strengthened Reliability: Consistent help from your vendor builds trust and reliability, ensuring that you can depend on your packaging to perform as needed.
- Adaptability to Changes: Effective support prepares you to adapt swiftly to emerging challenges or changes in market demands without significant setbacks.
This level of customer support is instrumental in maintaining efficient and uninterrupted packaging operations, turning a vendor from a simple supplier to a strategic business partner.
5) Range of Products and Services
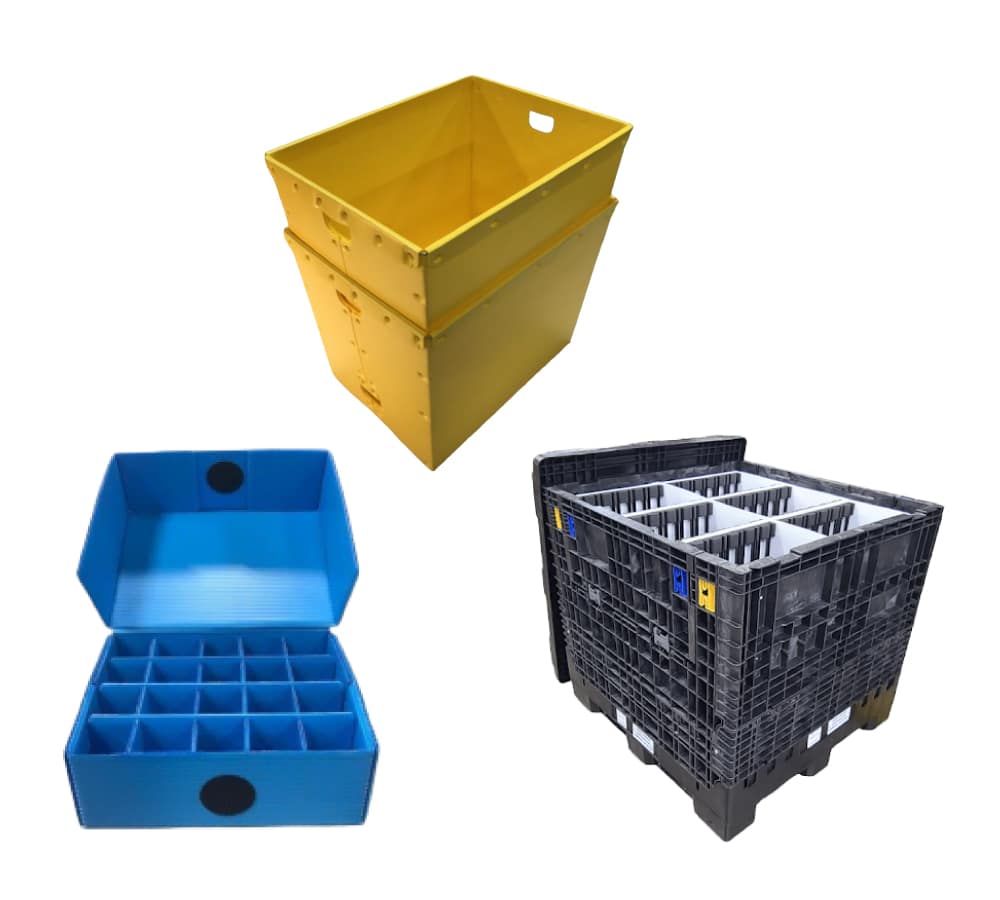
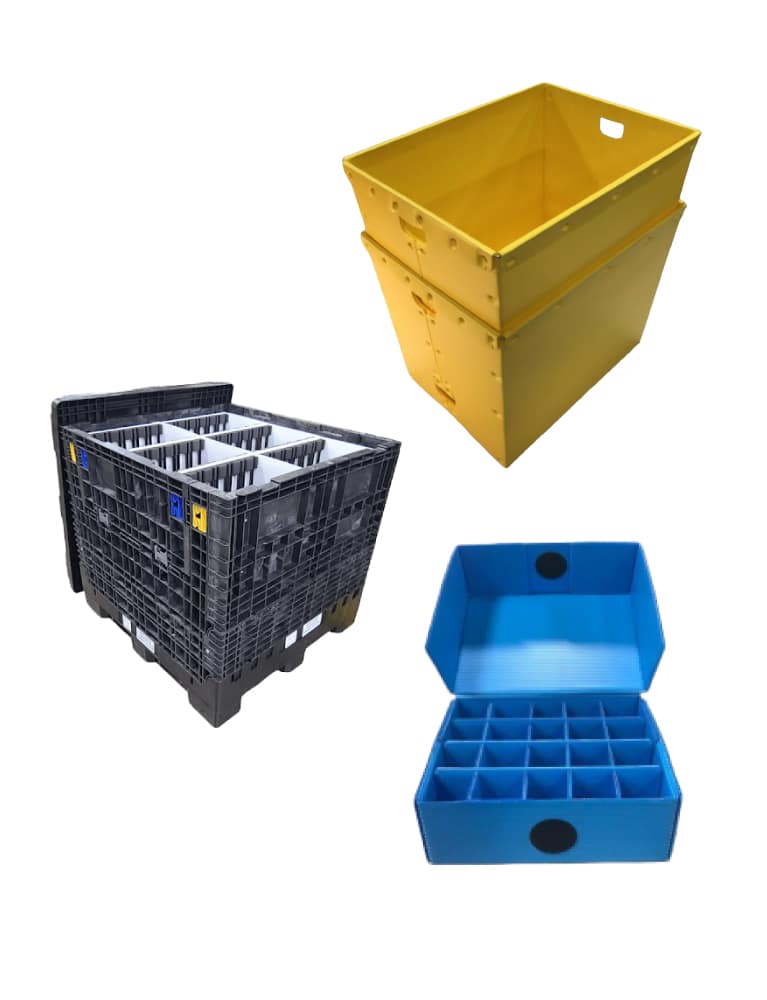
Selecting a packaging vendor with a comprehensive range of products and services is crucial for businesses to address their varied packaging needs effectively. This selection enables companies to find solutions that are both standard and custom, ensuring that all requirements, regardless of their complexity or specificity, are met precisely.
Vendor’s Ability to Offer Both Standard and Custom Products
A vendor that provides a versatile product offering that includes standard options alongside custom solutions caters to a broader spectrum of client needs. Standard products are essential for common packaging requirements and help companies keep costs down while maintaining quality. However, custom products are invaluable for meeting specific challenges, such as unusual dimensions, unique protective needs, or brand-specific aesthetics. This duality in product offerings ensures that every packaging challenge can be addressed competently.
Significance of a Wide Product Range
A wide product range is not just about having numerous options; it’s about the significance of these options in solving specific industrial needs. For instance, businesses in the electronics sector require anti-static packaging solutions, while pharmaceutical products need sterile and secure packaging. Having access to a diverse range of packaging types, from rugged industrial cartons to delicate custom foam inserts, means businesses can rely on a single vendor for all their packaging needs, simplifying logistics and procurement processes.
The Advantage of Additional Services
Beyond just products, top-notch vendors provide additional services that enhance the value they offer to their clients. These services can include packaging design consultation, prototype development, and even packaging system evaluations. Moreover, some vendors offer cleaning, repair, lease, and rental services—extending the lifecycle of packaging materials and providing flexibility and cost-effectiveness. This comprehensive service approach ensures businesses have consistent support throughout their packaging lifecycle, from initial design to ongoing maintenance.
Offering an extensive range of products and services enables packaging vendors to act as full-service partners, adapting to client needs as they evolve and ensuring packaging operations are as efficient and effective as possible.
6) Reputation and Reliability
Selecting a packaging vendor with a solid reputation and consistent reliability is crucial for businesses requiring top-quality packaging solutions. A reputable vendor not only ensures product safety and quality but also enhances a company’s own reliability in the eyes of its customers.
Evaluating Vendor Reputation
When assessing potential packaging vendors, consider their market standing. Look for published testimonials, online reviews, and case studies which provide insights into their operational history and client satisfaction levels. A vendor that enjoys high regard in the industry is likely to offer more dependable and high-quality services.
Indicators of Reliability
Reliability can be gauged through several indicators such as the promptness and accuracy of their service, the consistency in product quality, and their ability to meet delivery deadlines. Reliable vendors often have robust processes and systems in place to ensure that they consistently meet or exceed client expectations.
Importance of Consistent Performance
Lastly, consistent performance over time is a hallmark of a trustworthy vendor. Businesses should seek vendors that have not only performed well in the past but also show a steady commitment to quality and improvement. This continual evolutionary process in services and products assures businesses that the vendor will remain a valuable and stable partner in the long term.
Brandon K.
Universal Package Customer
7) Cost-Effectiveness
When selecting a packaging vendor, cost-effectiveness is a crucial factor that balances affordability and quality. Businesses should not only focus on the initial price but also consider the long-term value and potential cost savings that high-quality, durable packaging solutions can provide.
Assessing Pricing and Quality
It’s important to examine how a vendor prices their packaging solutions compared to the quality offered. Higher upfront costs might lead to lower long-term expenses due to reduced damage rates and less frequent replacements. Companies should request detailed breakdowns of costs and assess the material used, the durability of the packaging, and its expected lifecycle.
Long-Term Cost Savings
Investing in reusable and durable packaging can significantly reduce the overall cost over time. For example, sturdy containers that can withstand multiple shipments or storage scenarios can decrease the need to purchase new packaging frequently. Businesses should query vendors on the expected lifespan of their offerings and consider how these products could reduce costs in operational, shipping, and storage processes.
Hidden Costs
Beyond the initial purchase price, additional costs such as maintenance, repairs, and service fees can affect the total cost of ownership. Prospective buyers should inquire about any extra fees associated with the packaging solutions. Understanding these costs upfront can prevent unexpected expenditures and help in making a more informed decision about the vendor’s cost-effectiveness.
By considering the longevity and reliability of a packaging vendor’s products, businesses can ensure that they are receiving long-term value rather than short-changed savings.
8) Innovation and Sustainability
Recognizing the progressive demands in the packaging industry, astute businesses seek vendors that prioritize innovation and sustainability. These aspects not only enhance packaging efficiency but also reflect a company’s commitment to responsible practices. By selecting a vendor adept in these areas, businesses can solve complex packaging challenges while adhering to environmental standards.
Role of Innovation in Advanced Packaging Solutions
Innovative packaging vendors use cutting-edge technology to develop solutions that improve the safety, manageability, and aesthetics of packaging. Advanced features, such as temperature-control mechanisms and smart indicators for product integrity, cater to the unique requirements of sectors like pharmaceuticals and food services. By investing in such state-of-the-art features, companies ensure that their packaging solutions are prepared for future market trends and consumer demands.
Emphasis on Sustainability and Eco-friendly Materials
Sustainability is a critical criterion in the selection of a packaging vendor, reflecting a growing global emphasis on environmental responsibility. Vendors that incorporate sustainable practices, such as using recyclable materials and minimizing waste, contribute to a lower ecological footprint. Opting for packaging solutions made from biodegradable, recycled, or easily recyclable materials can significantly impact a brand’s image and its alignment with the values of environmentally-conscious consumers.
Case Studies: Highlighting Cutting-edge Solutions
To illustrate the effectiveness of combined innovation and sustainability, consider vendors that offer modular packaging systems which can be easily adjusted or repurposed for different products. Another example is the integration of QR codes into packaging designs, allowing for improved traceability and consumer engagement. These examples show how advanced packaging solutions can revolutionize product delivery, enhance user experience, and support sustainability goals.
By prioritizing these modern approaches in packaging solutions, businesses not only comply with regulatory demands but also leverage competitive advantages. This aspect of vendor selection is crucial for companies looking to maintain relevance and responsibility in their operations.
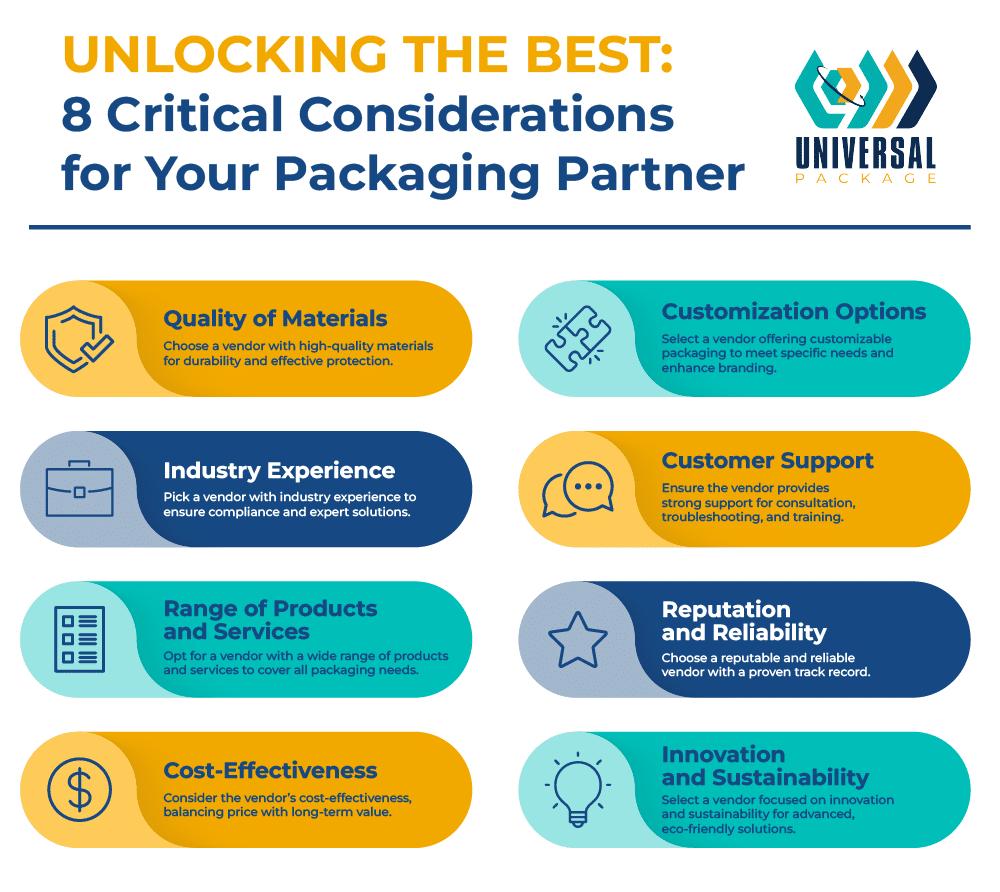
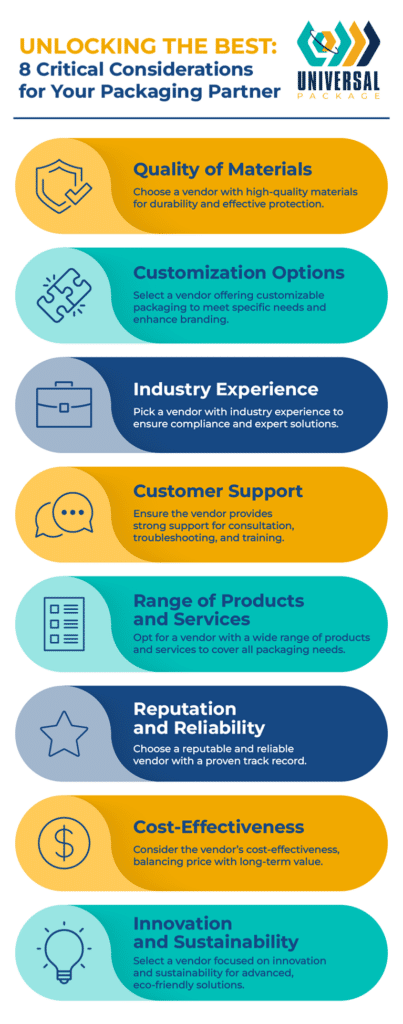
Universal Package: Your Partner for Optimal Packaging Solutions
Choosing the right packaging vendor is crucial for ensuring your products are protected and handled efficiently across various industries. Universal Package stands out as a partner that not only understands the diverse needs of industries like appliance, automotive, electronics, and pharmaceutical but also offers tailored solutions to meet these specific requirements. With our extensive range of custom and standard products, from corrugated plastic containers to foam packaging assemblies, we are equipped to offer packaging solutions that align with your business’s needs for durability, functionality, and cost-effectiveness.
Let us help you enhance your packaging strategy. Explore our products and services today and experience what effective, reliable, and customized packaging solutions can do for your business. Connect with Universal Package to discuss your packaging needs and learn how we can assist you in achieving operational excellence with our innovative, sustainable packaging solutions.