In the fast-paced world of warehouse management, efficiency is king. Kitting, a streamlined approach to assembly, stands as a beacon of optimization, promising to shave precious time off order fulfillment while minimizing errors.
This blog post delves into the transformative power of kitting, outlining how it redefines traditional assembly lines and offers a competitive edge to businesses in various industries.
From reducing assembly times to enhancing inventory control, we will explore the myriad of advantages in implementing kitting in your warehouse operations.
With Universal Package’s expertise in providing custom packaging solutions, their custom kitting totes are one tool companies can implement to set up efficient kitting practices. Whether you’re a business owner, warehouse manager, or logistics coordinator, this post will equip you with actionable insights to elevate your packaging and assembly process to new heights of efficiency.
Understanding Kitting in Warehouse Assembly
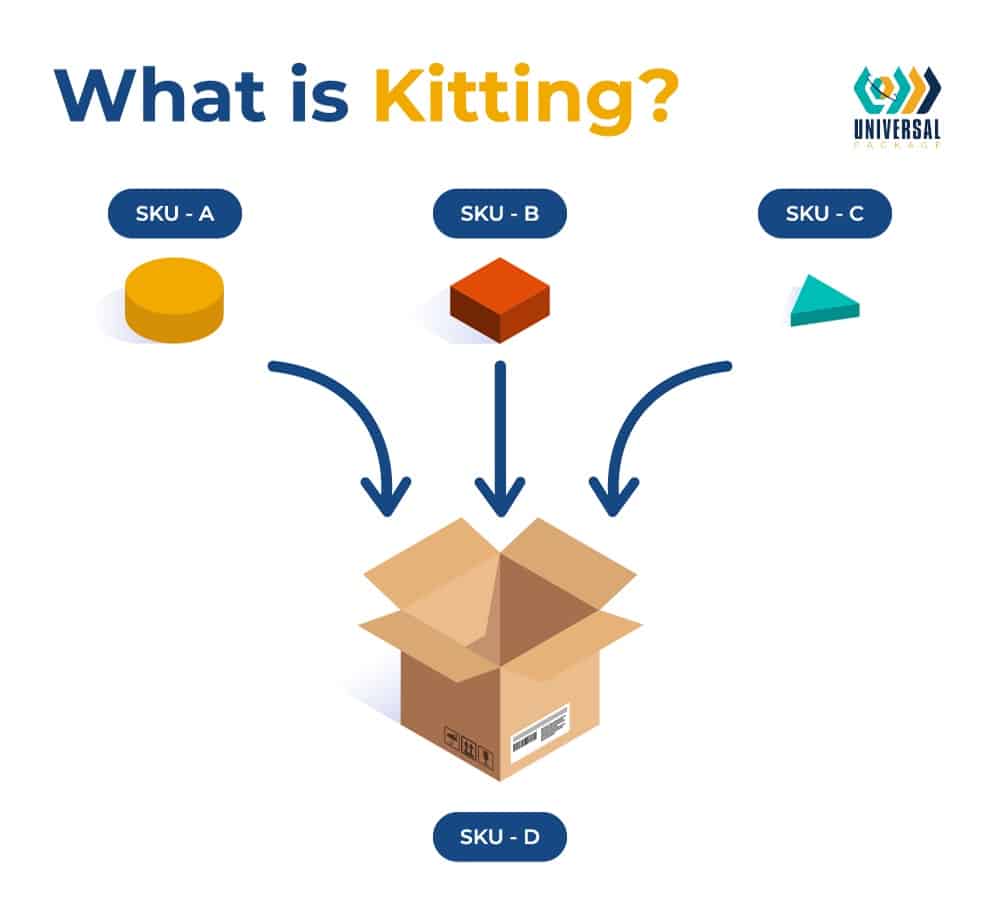
Kitting, a crucial process in warehouse assembly, involves collating individual items together, packaging, and supplying them as a single unit. This approach guarantees that all necessary components required for fabricating a specific product or assembly are compiled in advance, hence enhancing the overall efficiency of picking and assembly operations. Moreover, it allows warehouse employees to focus exclusively on the assembly process without the constant interruptions of gathering parts, thereby significantly increasing productivity and operational efficiency.
Representation of traditional warehouse assembly often shows workers picking individual parts for each order, a labor-intensive and error-prone process. However, kitting presents a more streamlined alternative by organizing all requisite components into pre-packed, ready-for-assembly units. This not only simplifies the assembly line but also mitigates the risk of errors and oversights, consequently improving the quality of operations.
Several industries recognize the immense value of kitting and have effectively incorporated it into their operations. These comprise manufacturing, e-commerce, automotive, and electronics sectors, where the majority of products involve multiple components needing assembly into a finished product.
With its systematic method and demonstrated efficacy, kitting continues to garner widespread acceptance as an integral part of warehouse assembly operations, engendering increased operational efficiency and productivity.
Kitting vs. Bundling
Kitting is the process that entails packaging separate but related items as a single unit, which then becomes a single SKU. Not all items within a kit can usually be sold separately, meaning it may require certain special elements like a unique box or promotional insert that cannot independently be purchased by a consumer. Clients often provide specific instructions surrounding the arrangement and assembly of these kits.
For instance, a client may provide a unique box, promotional insert, and detailed packaging instructions for their product. When a consumer orders this particular package, our warehouse team receives a packing slip listing each piece of the kit as a separate SKU. This indicates that the items together comprise a kit.
Bundling, on the other hand, is the process of gathering individual items together and offering them as one unit, which also results in a single SKU. The critical aspect of bundling is that each SKU in the bundle can still be sold individually, unlike kits.
Bundles don’t typically require special boxes or promotional inserts. Since bundling involves simply packing established products together in a box, clients usually do not have specific packing requirements, in contrast to kits.
For example, if a consumer purchased two separate kits together, this would be considered a bundle since each kit could also have been sold separately.
Therefore, while both kitting and bundling group items together for sale, they differ in their assembly and the independent availability of the items involved.
Advantages of Implementing Kitting
Kitting streamlines the assembly process by grouping all the components needed for a single product or a series of products together in advance.
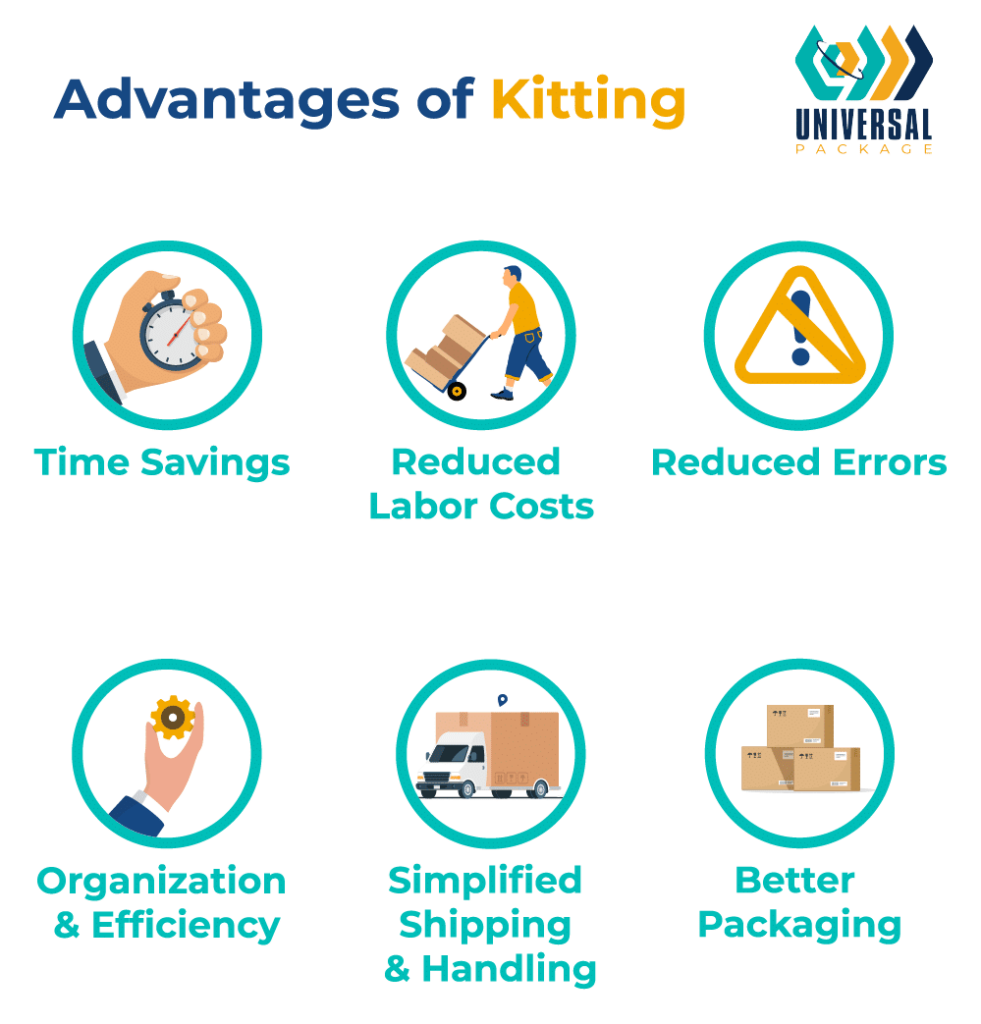
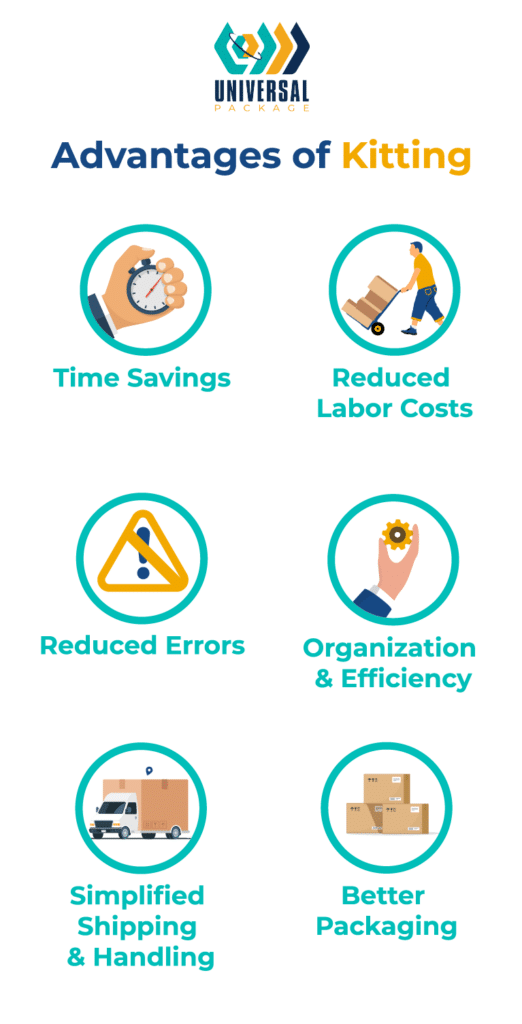
Time Savings
This pre-assembly method reduces the time spent by workers searching for individual parts, as everything required is readily available in one package. The efficiency gained from this approach can significantly quicken the order fulfillment cycle and increase throughput in the warehouse. Quicker fulfillment and delivery not only can save the company money but can also improve customer satisfaction.
Reduced Labor Costs
By reducing the time spent on picking and packing individual items, labor costs can be significantly reduced. Furthermore, less staff is needed for picking, processing, and shipping orders, enabling the redirection of labor resources to other areas of need in the warehouse. With a nationwide staffing shortage, 548,000 workers short to be exact, labor efficiencies are critical.
Reduced Errors
Implementing kitting also decreases the likelihood of errors during assembly. With all components of a product pre-selected and bundled, there’s a reduced chance for workers to pick the wrong parts, which minimizes the risk of sending incomplete or incorrect orders to customers.
Organization & Efficiency
Kitting significantly improves the organization and efficiency of the order fulfillment process. By creating pre-packaged bundles of frequently combined items, it reduces the overall SKU count, making inventory management easier and optimizing warehouse space usage which is critical when warehouse space costs have risen over 50% over the past 5 years. This streamlined approach reduces the time taken to assemble orders, preventing potential shipping delays. The ease of locating needed items for popular combinations through kitting enhances the overall efficiency and productivity of the entire fulfillment process.
Simplified Shipping & Handling
Shipping one kit, rather than multiple individual items, simplifies the process, making it less costly and time-consuming. Additionally, with fewer packages to handle, there’s reduced risk of shipments being lost or misplaced, further streamlining the logistics process.
Better Packaging
Kitting significantly improves the packaging process, thereby reducing costs and improving product safety. Instead of packing each individual SKU separately in standard boxes that might be too large, kitting enables you to pack items together in custom-sized boxes suited to their dimensions. This not only reduces package size and dimensional weight, but also saves on material costs such as packing fillers and tape.
Additionally, kitting enhances product protection during shipment, as items packaged together in custom packaging tend to be safer. Using customized packaging materials tailored to the items’ size and nature reduces the chance of damage during transit, providing an additional layer of product protection. The combined benefits of improved packaging and better product safety through kitting provide a strong boost to the overall profit margin.
The Kitting Process
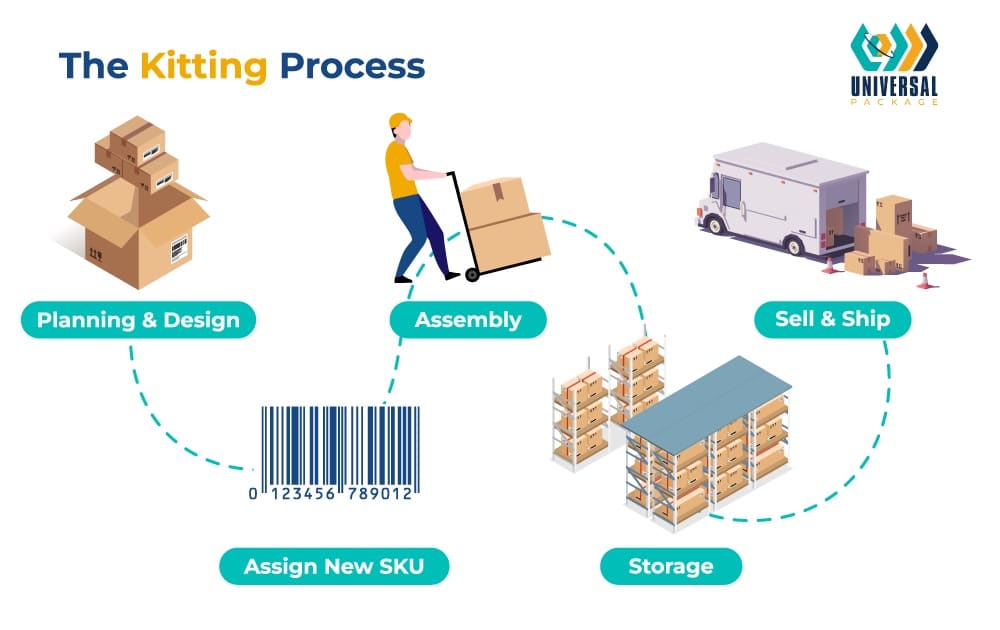
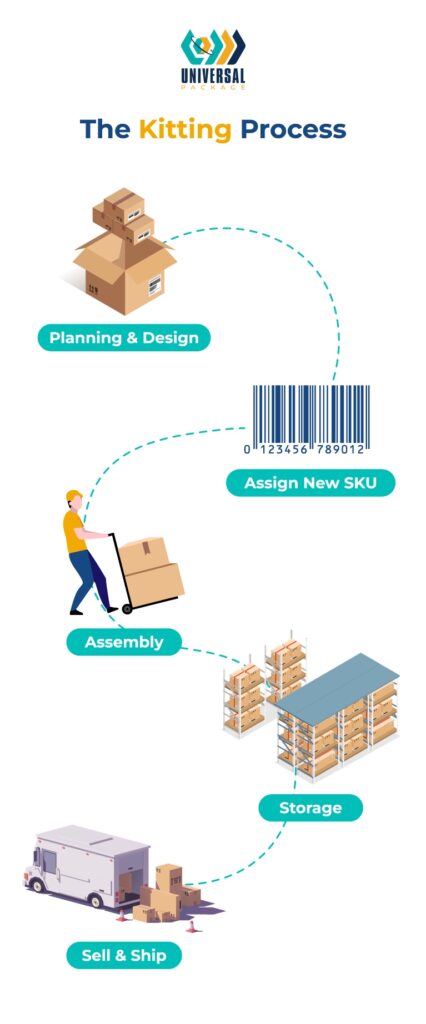
Although the process appears straightforward, it’s important to meticulously follow a sequence of steps to execute it correctly.
1. Planning & Design
The initial step involves determining which items should be grouped together in a kit. This is often based on customer buying patterns and preferences.
2.) Assign New SKU
A new SKU is created for each unique kit. Creating new SKUs for kitted items allows for easier management of inventory and more efficient order fulfillment.
3.) Assembly
After the new SKUs are developed, the assembly of the kits begins. This step includes gathering all individual items that are part of each kit and packaging them together. Ensuring efficient and accurate kit assembly is essential to avoid errors and maximize productivity.
4.) Storage
Once the kits pass quality control, they are stored in the warehouse and ready for shipment. This is where custom kitting containers can play a significant role. These specially designed containers provide secure and efficient storage for the kits, saving space and enhancing organization within the warehouse.
5.) Sell & Ship
When an order for a kitted item, identifiable by its unique SKU, is received, the relevant kit is retrieved from storage, prepared, and instantly dispatched in a single, streamlined fulfillment process. Because kitted items are packed together in one tote, it ensures quicker order fulfillment and higher level of product protection during transit.
Best Practices for Effective Kitting
Here are the optimal strategies and suggestions that constitute the best practices for efficient and effective kitting:
Optimize Warehouse Layout
Analyzing and organizing warehouse layout for optimal kitting flow is crucial in establishing an effective kitting system. By evaluating the current setup and making adjustments, businesses can ensure that materials move seamlessly from storage to the assembly area. Analyzing workflow can highlight inefficiencies or bottlenecks that should be addressed before implementing kitting.
Implement a Detailed Inventory Tracking System
Implement a robust Warehouse Management System (WMS) to monitor components required for each kit, optimize stock levels, enhance accuracy, and manage the reordering of parts and packaging supplies to avoid shortages. A sophisticated WMS not only enhances inventory management, but it also boosts the efficiency of order fulfillment, thereby significantly improving your kitting process.
Training
Training staff on kitting procedures is another key practice for maximizing efficiency. Employees should be well-versed in the kitting process, understanding how to compile kits quickly and accurately. Regular training sessions keep staff updated on the best handling practices and familiar with any changes to the kitting lineup.
Start Small
If it’s a new concept, start small. Don’t start with massive SKUs. Begin with small SKU runs that are affordable and marketable. A trial run will give you ample time to detect pitfalls before scaling up.
Continual Review, Update, and Result Tracking
Regularly review and update your kits to ensure they reflect the current product changes and market demands. Proactively updating can prevent delays in order processing and avoid the build-up of obsolete inventory. Simultaneously, keep track of the kitting process by storing relevant data to monitor the efficiency and accuracy of your system. This ongoing tracking, coupled with frequent updates, helps you make informed decisions when adjusting your kitting system and streamlines operations.
Overcoming Common Challenges in Kitting
Kitting, while transformative for warehouse assembly lines, can present its own set of challenges. Primary among these is space constraints, multiple component management, inventory tracking, and quality control. Below is a deeper look at each of these common challenges with tips on how to resolve these issues.
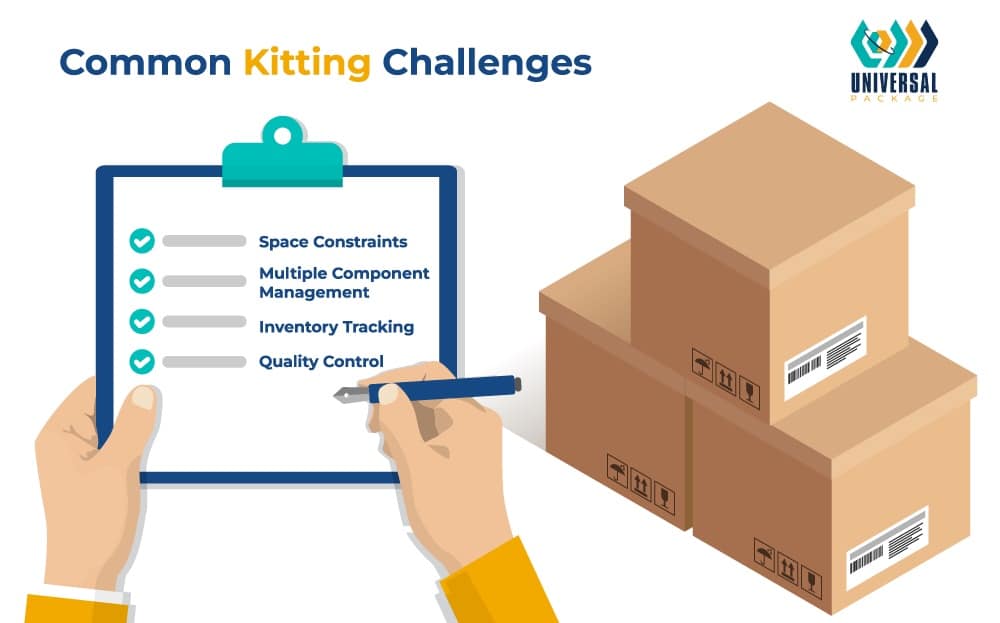
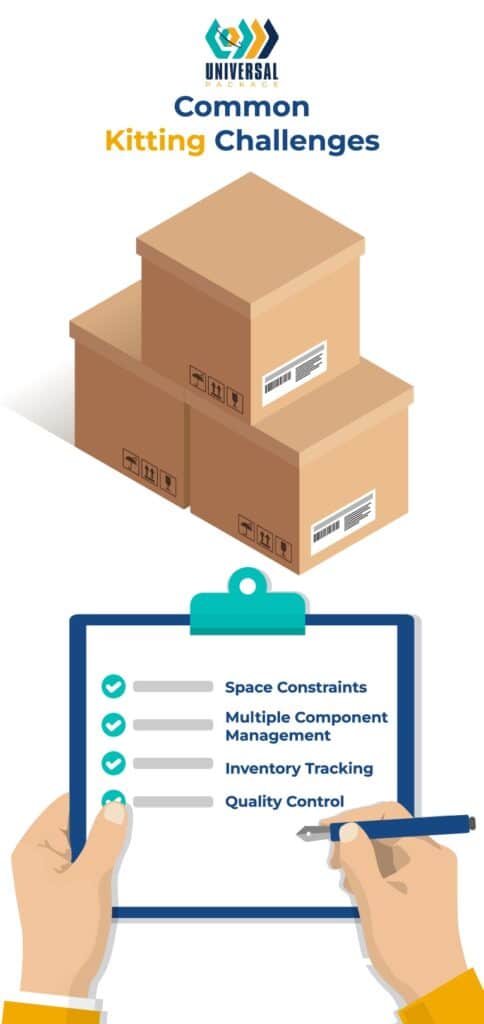
A common issue warehouses face when implementing kitting is the lack of space. Kitting typically requires a specific area for organizing and storing pre-assembled kits. By employing custom-made kitting containers, boxes, and totes, warehouses can optimize their existing space and accommodate an efficient kitting system. These custom solutions can be precisely tailored to the sizes of the kits, making them highly space-efficient.
Another common issue arising in kitting is the complexity of managing multiple varying components within kits. Each kit may contain numerous parts of different sizes, shapes, and handling requirements, complicating the picking and assembly process. Once again, custom kitting containers can come with compartments designed to fit the specific components, helping streamline the picking and assembly operations.
Implementing a meticulous approach to planning and inventory tracking is also crucial. This ensures all components are readily available and accurately accounted for in every kit, eliminating mismanagement.
Quality control is a paramount aspect, essential to maintain the integrity of the kitted items. Implementing a robust quality assurance protocol can prevent the inclusion of incorrect or defective components in kits, ensuring the delivery of perfect kits every time. Techniques such as regular inspections and an accountability system for tracking and rectifying errors should be established.
With custom-made kitting totes, boxes, and containers, alongside diligent planning and stringent quality control methods, many of the obstacles in the kitting process can be resolved effectively.
How Universal Package Can Enhance Your Kitting System
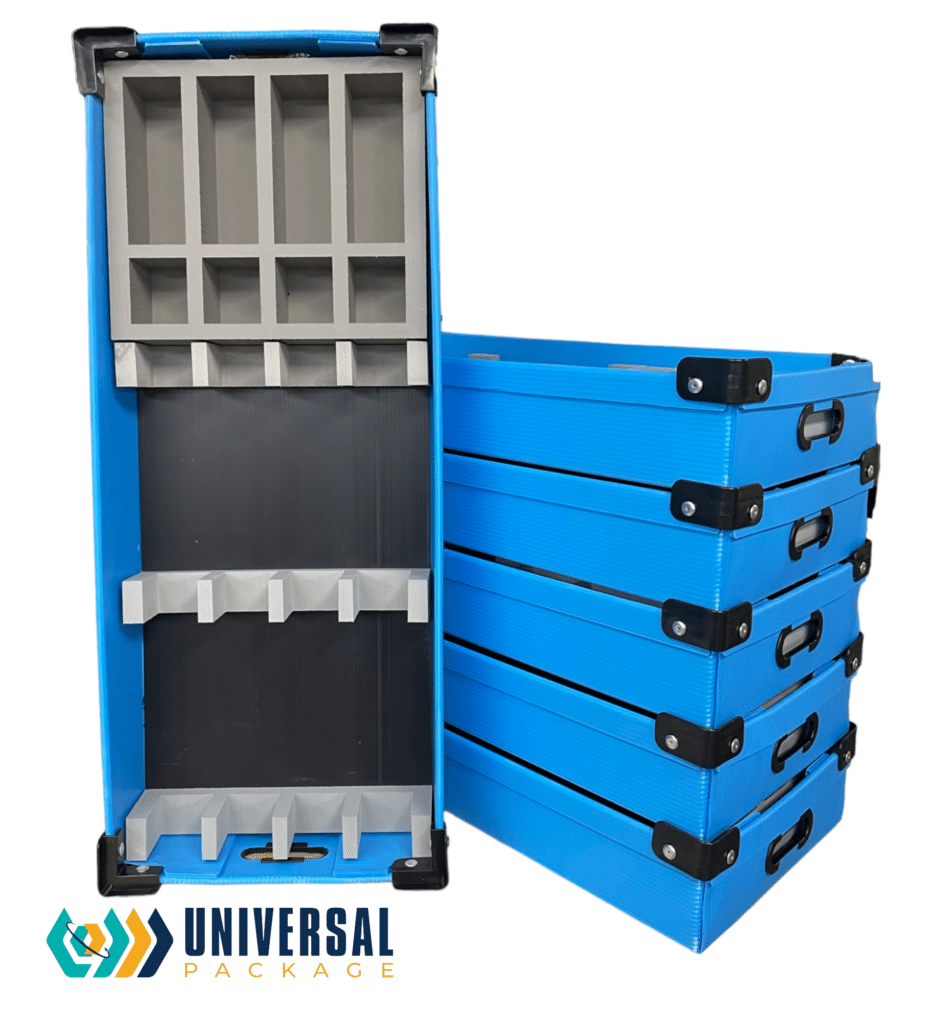
Universal Package specializes in delivering customized packaging solutions that are specifically designed to meet the unique requirements of customers across various industries. By offering a range of durable packaging and storage solutions such as custom made kitting totes, Universal Package ensures that different kit sizes and shapes are easily accommodated, contributing to an efficient kitting process. The adaptability of their products allows businesses to precisely fit components, thereby reducing wasted space and enhancing protection during storage and transit.
Beyond providing physical packaging products, Universal Package boasts a talented and skilled design and engineering team delivering innovative kitting container design services tailored to simplify the kitting process.
The team’s creativity shines especially when confronted with stringent restraints, always able to envision and craft solutions that perfectly meet customer needs. Universal Package ensures every component of a kit is readily accessible, and that the packaging fosters time-efficiency during assembly.
With our unwavering commitment to quality and efficiency, Universal Package represents a valuable resource for clients seeking to optimize or enhance their kitting systems. Therefore, Universal Package serves as a steadfast partner for businesses aiming to implement or boost their kitting strategies.
Taking the Next Steps Towards Kitting in Your Warehouse
Assessing your current assembly process for kitting potential begins with a thorough analysis of your existing workflow. Identify areas where time is lost, errors are frequent, or inventory management is challenging. This will help determine the suitability of kitting for your operations and pinpoint the kinds of changes needed to implement the strategy effectively.
Identifying the right partner for packaging and kitting solutions is critical for a smooth transition. Look for a provider like Universal Package that not only offers a range of durable and versatile containers but also understands the intricacies of kitting. Their expertise can be invaluable in customizing solutions that fit your specific needs.
Planning a phased approach to integrate kitting into your operations can mitigate risk and make the transition manageable. Start with pilot programs on select product lines to refine the kitting process, gather feedback, and make necessary adjustments before scaling up across your warehouse.
Optimize Your Assembly Line Today!
As we’ve explored the transformative power of kitting in warehouse assembly, it’s clear that the right strategies can lead to substantial gains in efficiency and accuracy. From compressing assembly times to enhancing inventory control, kitting offers undeniable benefits for businesses in rapidly changing industries.
With the right planning and execution, it’s a strategy that can deliver competitive advantages. Remember, the success of implementing kitting is largely influenced by the quality and suitability of the packaging solutions you choose.
Universal Package stands ready to support your journey towards a more efficient assembly process. Our range of customized packaging solutions, including Corrugated Containers, Hand Totes, and Plastic Bulk Containers, are designed to integrate seamlessly with your kitting system.
With our expertise in engineered packaging solutions and a suite of services from lease and rental to clean and repair, we’re here to ensure that your transition to kitting is smooth and beneficial.
Let’s take the next step together. Reach out to Universal Package today and let us tailor a packaging strategy that fits your unique kitting needs. With our durable and versatile containers, along with our experienced team’s support, your warehouse can achieve the next level of operational excellence.