In the bustling world of manufacturing, efficiency isn’t just an advantage; it’s a necessity. Work-in-Progress (WIP) carts stand out as pivotal tools in the quest to streamline production processes. These specialized carts play a crucial role in managing and moving materials through various stages of production, directly impacting operational efficiency and productivity.
This article explores how integrating custom WIP carts, particularly those offered by Universal Package, can transform production lines across multiple industries, from automotive to electronics.
We’ll delve into the benefits of implementing these carts, the importance of industry-specific customizations, and provide real-life examples illustrating their impact on manufacturing efficiency. By understanding how tailored WIP carts can address unique challenges, operations managers and production supervisors can unlock new levels of organizational excellence and workflow optimization. Join us as we unpack the transformative potential of WIP carts in enhancing manufacturing landscapes.
Understanding the Role of WIP Carts in Manufacturing
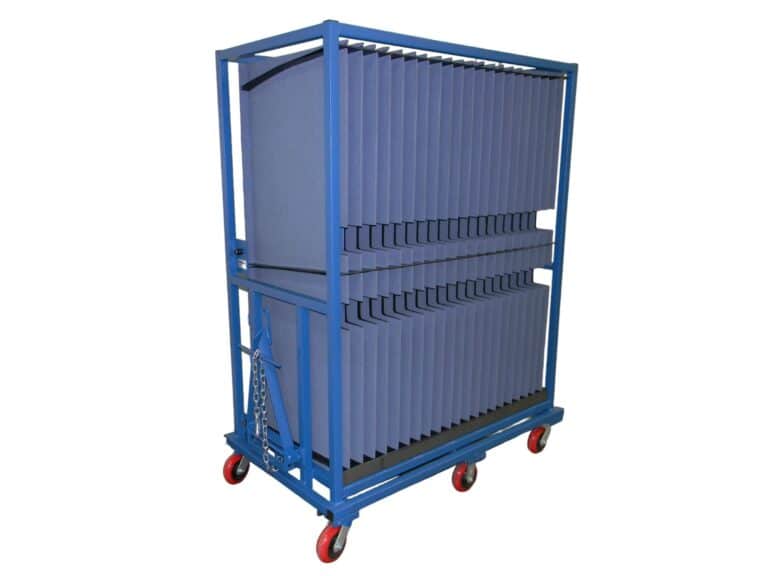
Work-in-Progress (WIP) carts, also referred to as steel racks, are crucial tools in the manufacturing industry, serving as mobile storage units that facilitate the flow of materials and semi-finished products between different stages of the production process. By enabling the smooth transition of items along the production line, WIP carts help keep materials organized and readily available, significantly reducing the time and effort involved in materials handling.
The importance of WIP carts in manufacturing environments cannot be overstated. They are designed to streamline production lines by minimizing unnecessary movement and organizing workflow. This organization is critical in reducing clutter on the shop floor, which can lead to improved safety and efficiency. By using WIP carts, factories can optimize their floor space and reduce the risk of damage to parts and components, leading to a more streamlined and cost-effective production process.
These carts play a pivotal role in ensuring that items are not only easy to locate but also safely and efficiently moved throughout the manufacturing process, reducing cycle times and increasing the overall throughput of the production system. This efficiency is essential in high-volume manufacturing settings where even small delays can lead to significant production bottlenecks.
Benefits of Implementing WIP Carts in Production Settings
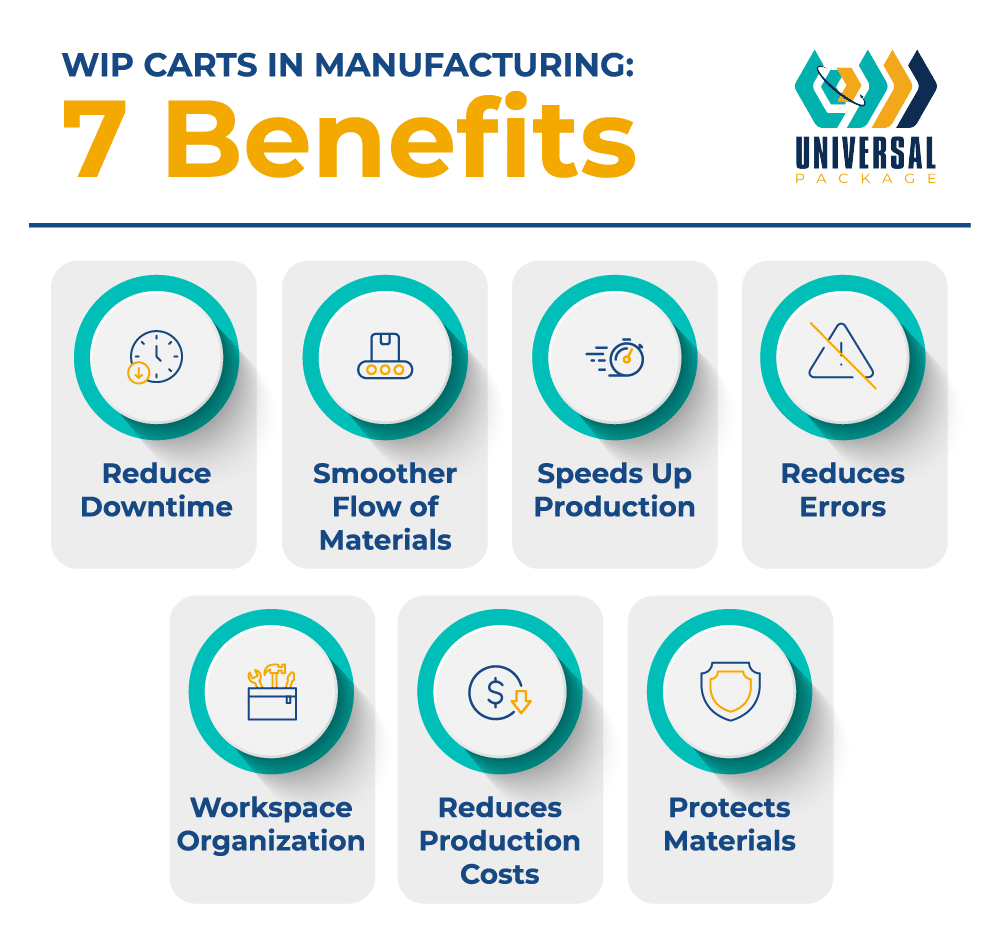
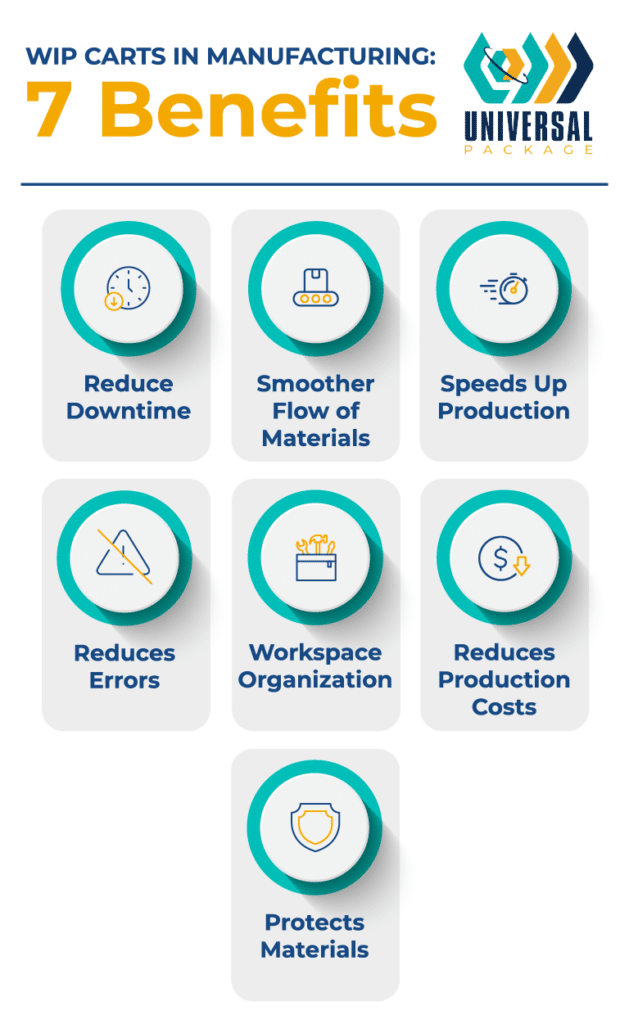
Implementing Work-in-Progress (WIP) tools such as carts and steel racks in manufacturing environments offers a range of benefits that address key operational challenges and enhance overall efficiency:
- Reduce Downtime: WIP carts minimize the time spent searching for materials and tools, leading to decreased transition times between production stages and enabling more continuous operations. By minimizing downtime, WIP carts contribute to improving overall productivity and throughput.
- Facilitates a Smoother Flow of Materials: These carts ensure that the right materials are readily available at the right place and time, facilitating a smooth flow of materials and allowing for easy movement. This organized approach speeds up production and reduces the likelihood of errors, ultimately enhancing overall output quality.
- Speeds Up Production: By streamlining the movement of materials along the production line, WIP carts contribute to accelerating the production process, enabling quicker turnaround times and improved efficiency.
- Reduces the Likelihood of Errors: The organized and accessible nature of WIP carts minimizes the risk of errors in material handling and staging, contributing to higher precision and quality in manufacturing operations.
- Organizes Manufacturing Space: WIP carts provide designated locations for various components and tools, helping maintain a tidy and uncluttered environment. This organization is critical for efficiency and safety, reducing the risk of accidents and fostering a better working environment.
- Reduces Production Costs: By minimizing downtime, optimizing workflow, and reducing the risk of material damage, WIP carts contribute to cost reduction through increased productivity and minimized rework or associated costs.
- Minimizes the Risk of Material Damage: The durable construction and organized movement facilitated by WIP carts help minimize the risk of material damage, contributing to higher overall efficiency and cost-effectiveness in the manufacturing process.
Custom WIP Carts vs. Standard Off-the-Shelf Carts: A Comparison
When evaluating the choice between standard off-the-shelf carts and custom Work-in-Progress (WIP) carts, it’s important to consider the specific needs and operational challenges of your manufacturing environment. Here’s a comparison to help you make an informed decision:
Standard Off-the-Shelf Carts
- Limited Flexibility: Off-the-shelf carts often lack customization options, resulting in limited adaptability to the unique requirements of different industries and production processes.
- Generalized Design: These carts may not be ideal for specific material handling needs, potentially leading to inefficiencies in workflow and space utilization.
- One-Size-Fits-All Approach: Standard carts might not address industry-specific challenges, such as handling delicate electronic components or heavy automotive parts, leading to potential risks and limitations in functionality.
Custom WIP Carts
- Tailored Solutions: Custom WIP carts are designed to address the specific material handling and transportation requirements of diverse industries, offering tailored features to optimize workflow and space utilization.
- Industry-Specific Customizations: These carts can be customized to accommodate the unique needs of industries like automotive, aerospace, electronics, and pharmaceuticals, providing solutions for handling specialized components and materials.
- Enhanced Efficiency and Safety: By integrating client-specific features such as adjustable shelving, specialized coatings, and ergonomic design, custom WIP carts offer improved efficiency, safety, and cost-effectiveness in material handling.
By comparing these options, it becomes clear that custom WIP carts offer a level of flexibility, functionality, and industry-specific customization that can significantly enhance manufacturing efficiency and productivity.
The Importance of Industry-Specific Customizations for WIP Carts
When it comes to customizing Work-in-Progress (WIP) carts in manufacturing, addressing industry-specific challenges is paramount. These customizations play a crucial role in enhancing operational efficiency and productivity by tailoring the carts to meet the unique material handling and transportation requirements of different industries, such as:
- Automotive Industry: The size and capacity of WIP carts can be customized to accommodate heavy automotive components, ensuring they can hold items like engines and transmissions without being too bulky, thus maximizing space in the production environment.
- Aerospace Industry: Customized WIP carts may require features for transporting large and delicate aerospace components, such as specialized tool holders to secure sensitive parts during movement.
- Electronics Industry: In the electronics sector, WIP carts may need specialized interiors with antistatic coatings to protect delicate components during transport, as well as labeling and identification features to track sensitive electronic parts throughout the production process.
- Textile Industry: WIP carts customized for the textile industry might require ergonomic features such as easy-grip handles to improve worker comfort and safety during the movement of fabric rolls and materials.
- Pharmaceutical Industry: Custom WIP carts can include organizational features like dividers to facilitate the movement of pharmaceutical products and medical supplies, ensuring proper segregation and storage during transportation.
These tailored solutions allow companies to maximize the impact of WIP carts on their production processes, leading to significant improvements in efficiency, productivity, and safety across diverse industrial sectors.
Universal Package’s Expertise in Custom WIP Carts
Universal Package has established itself as a leader in the design and implementation of custom Work-in-Progress (WIP) carts, catering specifically to the nuanced needs of various manufacturing sectors. Their deep industry knowledge is reflected in the bespoke solutions they provide—each WIP cart is tailor-made to enhance functional efficiency and fit seamlessly into an existing production environment.
The company’s expertise stretches beyond simple manufacturing solutions. They offer a comprehensive analysis of a client’s operations to ensure that each WIP cart maximizes space utilization and optimizes workflow. This approach is significantly different from standard, off-the-shelf products that may not address specific operational challenges. Universal Package’s ability to integrate client-specific features—such as customized dimensions, and specialized material choices—into their WIP carts makes them a preferred partner for many in the industry.
How to Integrate Custom WIP Carts into Your Manufacturing Process
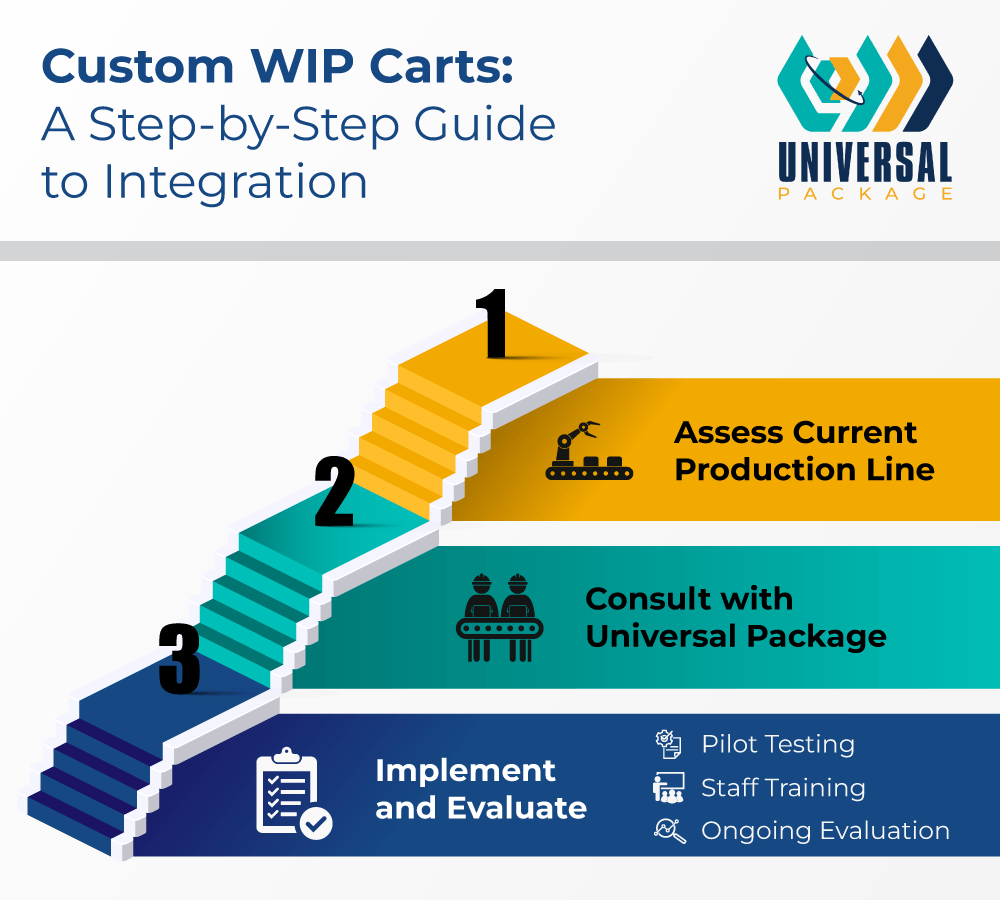
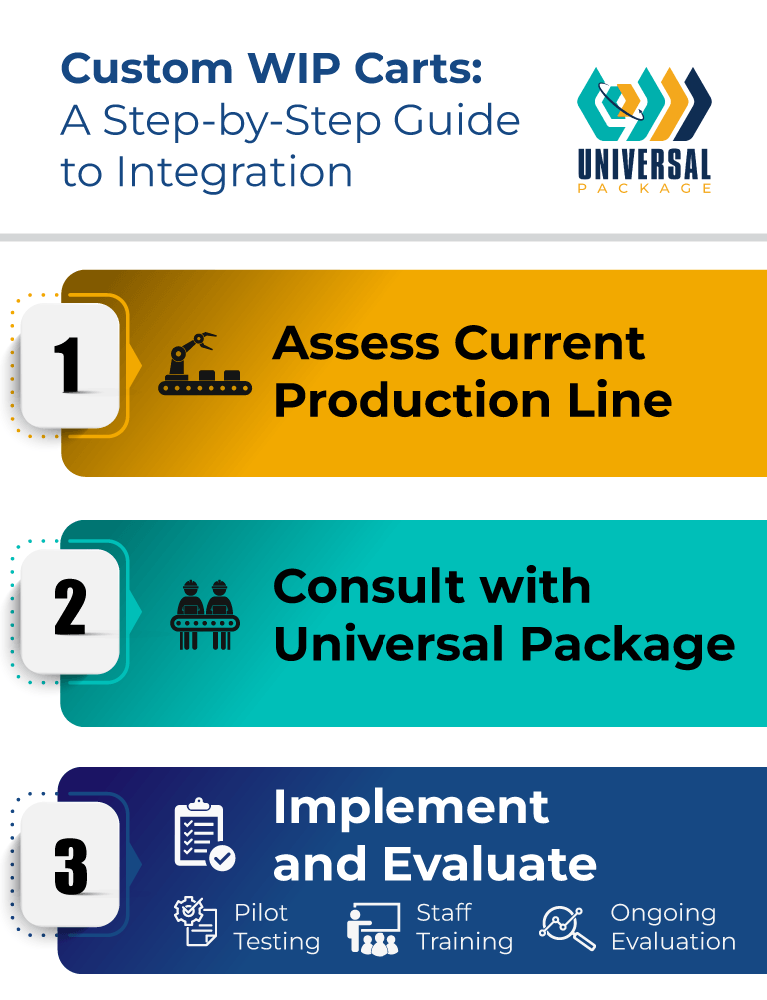
When considering the integration of custom Work-in-Progress (WIP) carts into your manufacturing process, it’s essential to understand the benefits and practicalities involved. By recognizing how these specialized carts enhance efficiency, streamline workflow, and address industry-specific challenges, operations managers and production supervisors can make informed decisions about their implementation.
Let’s explore how to effectively integrate custom WIP carts into your manufacturing environment.
1. Assessment of Current Production Line and Identification of Needs
To effectively integrate custom WIP carts into your manufacturing process, start by thoroughly assessing your current production line. Identify bottlenecks, frequent sources of delays, and specific areas where material handling inefficiencies occur. Analyze the layout of the production floor to understand the flow of materials and the logistic needs of various workstations. This step ensures that the customization of WIP carts directly addresses the identified inefficiencies.
2. Consult with Universal Package for Tailored WIP Cart Solutions
Once the needs are clearly identified, consult with Universal Package, leveraging their expertise in industrial packaging and material handling solutions. Discuss the specific challenges your production line faces, and explore how customized WIP carts can solve these issues. Universal Package offers a variety of customization options that can tailor carts to the size, capacity, and mobility requirements specific to your industry and individual workspace.
3. Implementation Steps and Best Practices for Integration
Implementing custom WIP carts involves several best practices to ensure smooth integration and maximum impact on productivity:
- Pilot Testing: Begin with a pilot test of the customized WIP carts in a small section of your production line to monitor their effectiveness and make necessary adjustments before a full-scale rollout.
- Training Staff: Educate your workforce on how to use the new carts efficiently. Highlight the benefits and demonstrate proper handling techniques to ensure safety and maximize usage.
- Continuous Evaluation: Regularly evaluate the performance of the WIP carts and the impact on the production process. Gather feedback from employees and make adjustments as necessary to optimize the workflow.
Transform Your Manufacturing Environment with Custom WIP Carts from Universal Package
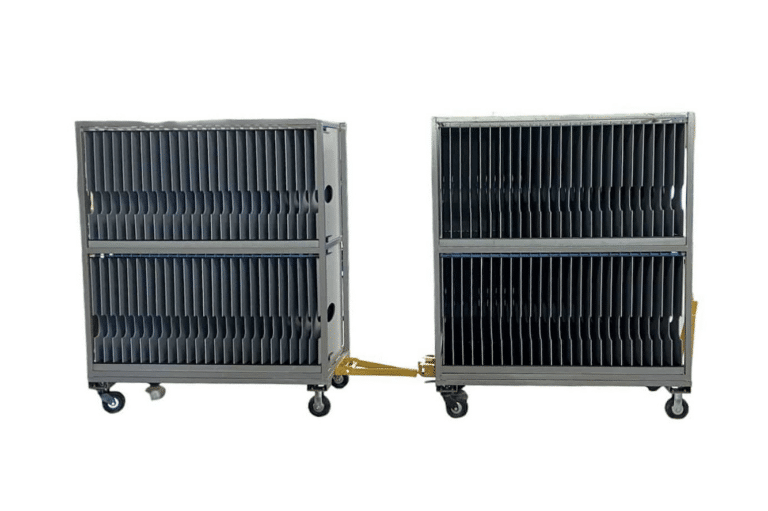
As we’ve explored the transformative impact that custom Work-in-Progress (WIP) carts can have on manufacturing environments, it’s clear that the efficiency of your production line hinges on the effectiveness of your material handling solutions.
Let’s discuss how we can tailor a solution that fits seamlessly into your production environment, reducing downtime and enhancing workflow. By partnering with Universal Package, you ensure not only an improvement in your manufacturing efficiency but also a competitive edge in your industry.
Reach out to us today to see how our custom WIP carts and comprehensive material handling solutions can transform your manufacturing processes. Together, we can achieve a more organized, productive, and efficient workspace.