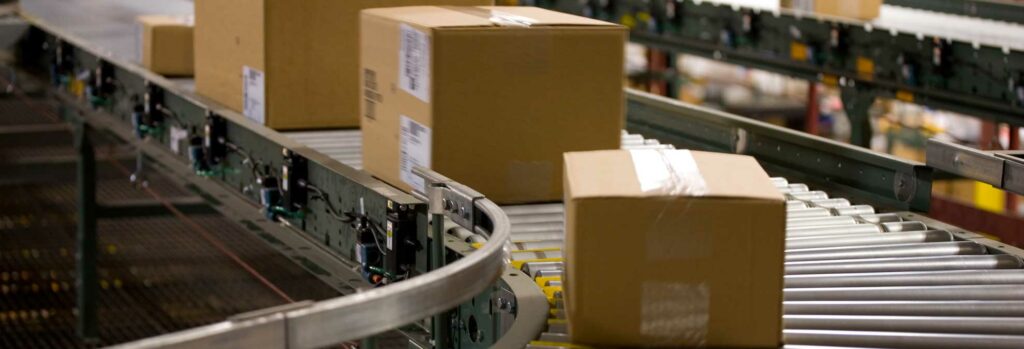
Providing quality packaging solutions and plastic containers is our job, but our goal is to make sure our WIP (work in progress) clients are also operating as efficiently as possible. By supplying materials, other than containers, clients have seen great improvements in their processes, WIP hurdles, and manufacturing bottlenecks.
Heavy Equipment Remanufacturing Client
This client makes money processing and remanufacturing heavy truck equipment by tearing down air compressors, rebuilding them completely and then painting. Universal was originally asked to quote paper paint masking templates for use during the parts painting process. The client’s original process required die cut paper templates and wire attachment ties to cover machined areas so paint would not touch.
Process & Engineered Solutions for WIP
After learning the client’s process and discussing with paint booth operators, we found the time to tie the masks in place was double that of the actual painting process. Further discussion revealed all parts being painted were made of steel. We suggested switching the paper mask templates to flexible, die cut magnetic sheets, the same material used for refrigerator doors magnets.
Client Efficiencies & Gains
The time to it took to place the magnetic masks on the steel parts versus wiring the paper masks in place was reduced dramatically. The client reported throughput of parts increased 10 times more than what they could originally process. An added benefit, the plastic magnets can also be reused a minimum of 8 times. This bonus, coupled with the increased output virtually eliminated the entire previous cost associated with this process, thus saving our customer both time and money.
Contact us to discuss streamlining your processes or for help designing your next custom solution.