Custom plastic trays are vital components in modern packaging, storage, and transportation. These trays provide tailored protection for products, optimize material handling, and enhance operational efficiency. For businesses requiring durable and customizable solutions, understanding the principles behind custom tray design is essential. In fact, learning more about a comprehensive guide on the topic—such as this resource on custom plastic trays—can help you navigate design challenges right from the start.
Key Considerations in Designing Custom Plastic Trays
Designing effective trays begins with assessing the specific requirements of your products and industry.
Product and Industry Requirements
Evaluate the items the tray will hold by considering their size, weight, and shape. Determine if they are delicate or heavy, and whether they need cushioning or impact resistance. It is also important to factor in operating conditions such as temperature fluctuations, humidity, and handling frequency. This assessment will guide decisions on whether the tray needs to be sanitizable, anti-static, or designed for rugged environments.
Safety and Durability
Tray design must balance protection with robustness. Fragile items may benefit from foam inserts that absorb shocks and vibrations, while heavier products might require rigid materials that withstand frequent handling. In these cases, incorporating reliable foam inserts is essential. Additionally, ensuring compatibility with automated systems helps reduce downtime and maintenance costs.
Sustainability and Reusability
Eco-friendly solutions are increasingly important. Opting for materials that facilitate reuse or recycling can lower total costs over time and reduce environmental impact. Reusable trays designed for closed-loop systems support sustainable practices while maintaining high performance.
Materials Commonly Used for Custom Plastic Trays
Selecting the right material affects a tray’s weight, longevity, and overall usability. Commonly used materials include:
Corrugated Plastic
Lightweight yet durable, corrugated plastic offers a high strength-to-weight ratio and resistance to moisture and chemicals. It is favored in industries like automotive and electronics due to its ease of customization and cost-effectiveness.
Foam Inserts
For products requiring extra protection, foam inserts provide targeted cushioning to absorb shocks and vibrations. This approach is especially beneficial for delicate electronic components or medical devices.
Solid Plastics and Metals
Heavy-duty applications might require solid plastics such as high-density polyethylene (HDPE) for repeated use or metal trays for extreme conditions. These materials are selected for their ability to withstand rigorous handling environments.
Design Features to Enhance Functionality
Effective custom tray designs incorporate features that streamline operations while ensuring product safety.
Tailored Compartments
By designing tailored compartments that fit specific product shapes, trays can prevent movement during transit and reduce the need for extra packaging. This customization minimizes damage and helps maintain product orientation and stability.
Stackable and Nestable Designs
Stackable designs optimize storage and workspace usage. Features such as molded edges or raised corners allow for secure stacking, while nestable designs reduce storage space when trays are not in use.
Specialized Options
For industries requiring extra protection, trays can include anti-static properties that shield sensitive electronic components. In addition, integrating ergonomic elements such as built-in handles or rounded edges improves user safety and makes handling more convenient.
Key Benefits of Custom Plastic Trays
Investing in custom plastic trays offers multiple advantages:
- Superior Protection and Precise Fit: A well-designed tray provides a tailored fit that minimizes product movement during transit, reducing the risk of damage and potentially eliminating the need for extra padding.
- Cost Efficiency and Long-Term Savings: Although the initial investment may be higher, reusable trays lower expenses in the long run by reducing disposable packaging, replacements, and product damage.
- Improved Organization and Workflow: With distinct compartments and configurations, custom trays support efficient assembly and packing processes. Organized trays enable quicker picking, packing, and reduced errors—crucial benefits in high-paced manufacturing environments.
- Enhanced Compatibility with Automation: Standardized tray designs integrate seamlessly into automated systems, boosting overall operational efficiency and consistency in handling procedures.
Industry Applications for Custom Plastic Trays
Custom plastic trays serve a variety of industries thanks to their adaptability and performance.
Automotive and Heavy Manufacturing
In these sectors, trays are designed for components ranging from small sensors to large engine parts. Durable trays that include foam inserts or precisely contoured compartments protect delicate components while securing heavier parts, ultimately improving safety and productivity.
Electronics
The electronics industry demands careful handling of sensitive equipment such as circuit boards and microchips. Utilizing anti-static materials helps safeguard these items against damage during production and shipping.
Medical and Pharmaceutical
Medical and pharmaceutical settings prioritize hygiene and precision. Trays made from easy-to-sterilize materials are used to hold items such as instruments, vials, or kits, ensuring these sensitive components remain contamination-free.
Other Applications
Many specialized industries benefit from the same core principles: precision, durability, and ergonomic design. The versatility of custom plastic trays makes them an indispensable asset wherever optimized storage and transportation solutions are required.
The Design Process for Custom Plastic Trays
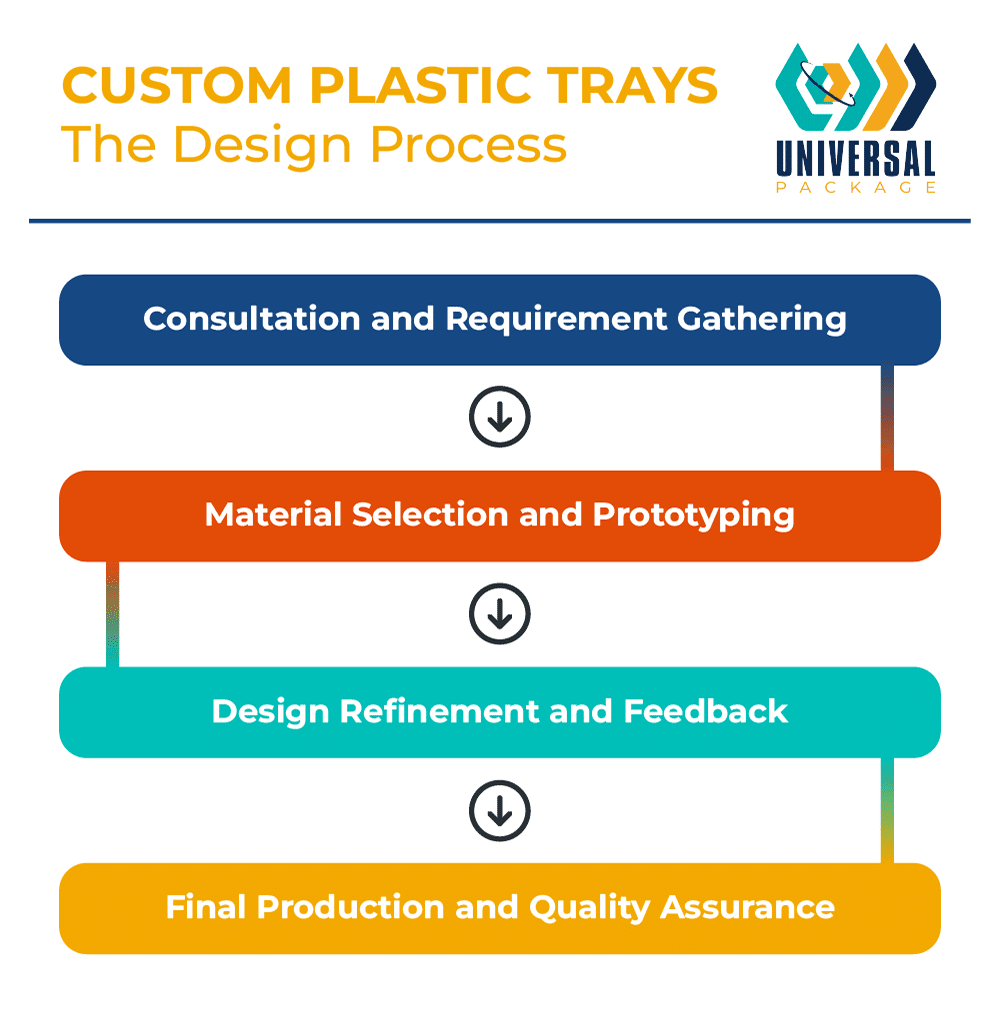
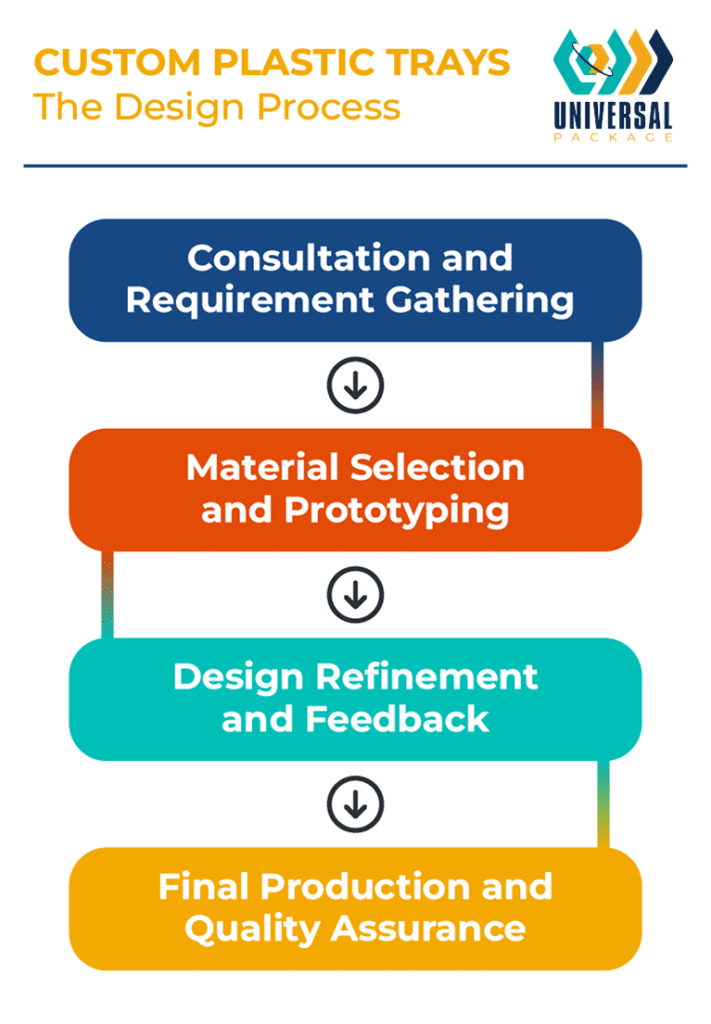
A structured development approach helps ensure trays meet both industry standards and operational demands.
- Consultation and Requirement Gathering: Begin with an in-depth conversation to identify your unique needs. Product dimensions, handling methods, and environmental factors shape the tray’s core design goals.
- Material Selection and Prototyping: Choose suitable materials based on protective needs and operating environments. Early-stage prototyping verifies the tray’s fit, durability, and functionality prior to large-scale manufacturing.
- Design Refinement and Feedback: Incorporate testing feedback to refine the tray’s design. Adjust compartment sizes or stacking features to ensure real-world performance. Input from seasoned manufacturers can further improve accuracy by leveraging precision molds.
- Final Production and Quality Assurance: With the design finalized, production follows strict quality checks to confirm that each tray meets specifications and operational requirements.
Challenges and Practical Solutions in Custom Tray Design
While designing custom trays can present certain obstacles, practical solutions ensure successful outcomes.
Accommodating Complex Shapes
Irregular product dimensions can complicate tray design. Advanced customization methods allow even unusually shaped items to be held securely.
Space Optimization
Confined storage or transport spaces can be addressed with stackable and nestable features. These designs maximize capacity and overall efficiency.
Enduring Harsh Environments
Exposure to extreme temperatures or physical abrasion demands robust material selection. For example, choosing high-density materials such as high-density polyethylene (HDPE) or metals, along with protective coatings, allows trays to operate reliably under demanding conditions.
Balancing Initial Costs
Although custom trays might entail higher initial costs, the long-term gains—including reduced product damage and fewer packaging replacements—frequently justify the investment.
Maximizing Efficiency with Custom Plastic Trays
Custom plastic trays are crucial for businesses seeking enhanced product protection, streamlined operations, and sustainable practices. Their tailored fit, robust materials, and innovative features deliver significant operational benefits and long-term cost savings. When considering custom tray solutions, working with a reputable manufacturer can help ensure every aspect of design and production aligns with your industry requirements.
Contact us at Universal Package today for a custom consultation and find out how our expert team can develop the ideal tray design for your unique packaging, storage, and transportation needs.