Imagine a material so versatile that it could redefine industries and transform our daily lives. The unassuming corrugated plastic holds secrets that are sparking a revolution in programmable materials. By unlocking the principles hidden within this commonplace material, scientists and engineers are pioneering innovations that could reshape our world.
“Understanding the structural ingenuity of corrugated plastic opens up new horizons in material science,” notes a leading expert in materials engineering. These insights are propelling the development of programmable materials that adapt, respond, and perform in ways once thought impossible.
In this journey, we investigate how the ingenious design of corrugated plastic is transforming the field of programmable materials, unleashing remarkable benefits across various industries.
Understanding Corrugated Plastic
Corrugated plastic, often recognized by brand names like Coroplast®, is a lightweight yet durable material composed of twin-wall plastic sheeting made from high-impact polypropylene or polyethylene. It’s manufactured through an extrusion process that forms fluted channels—called ribbing—between two flat layers. This structure resembles corrugated cardboard but offers enhanced resilience and versatility.
Key Properties and Advantages
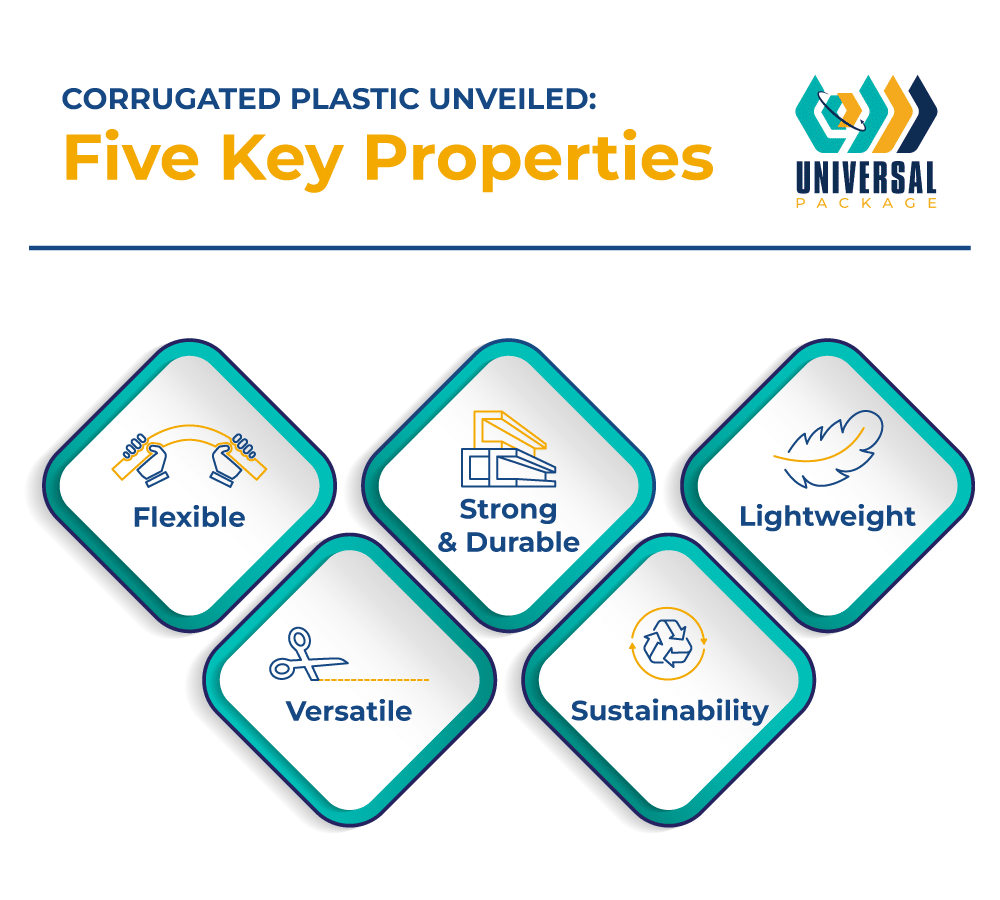
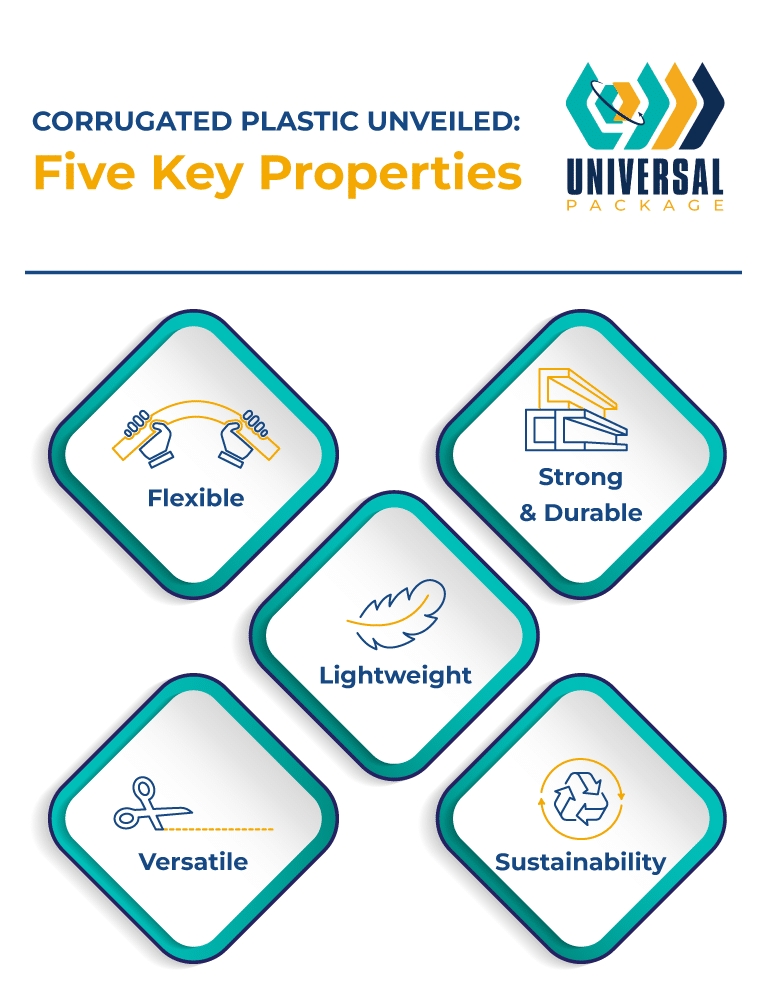
Let’s explore the remarkable properties that make corrugated plastic a material of choice in many applications:
- Flexibility: Thanks to its fluted structure, corrugated plastic can bend and fold without cracking. This flexibility allows it to adapt to various shapes and uses, making it ideal for custom packaging and creative design applications.
- Strength and Durability: The ribbed design significantly enhances the material’s strength-to-weight ratio. Much like how beams support a building without adding unnecessary weight, the flutes provide structural integrity while keeping the material lightweight.
- Lightweight: The hollow fluted design reduces material usage, resulting in a lighter product without sacrificing durability. This is crucial for industries where weight reduction leads to cost savings and increased efficiency.
- Versatility: Easily cut, shaped, and printed upon, corrugated plastic’s adaptability makes it suitable for packaging, advertising displays, construction, and more.
- Sustainability: Made from recyclable plastics and reusable in multiple applications, corrugated plastic supports environmental sustainability by reducing waste and promoting resource efficiency.
Programmable Materials: An Overview
Programmable materials are engineered substances that can change their properties, shape, or function in response to external stimuli like temperature, light, or mechanical stress. These materials have built-in abilities to sense, move, and respond—all within the material itself.
Current Advancements and Trends
- Shape-Memory Alloys: Metals that return to a predefined shape when heated. Used in medical devices such as stents that expand within arteries, improving patient outcomes.
- Self-Healing Polymers: Materials that can repair themselves after damage, extending product lifespans and reducing maintenance costs.
- 4D Printing: An extension of 3D printing where objects are designed to change shape or function over time when exposed to specific stimuli.
Building on these advancements, the innovative design principles of corrugated plastic are propelling the field of programmable materials forward.
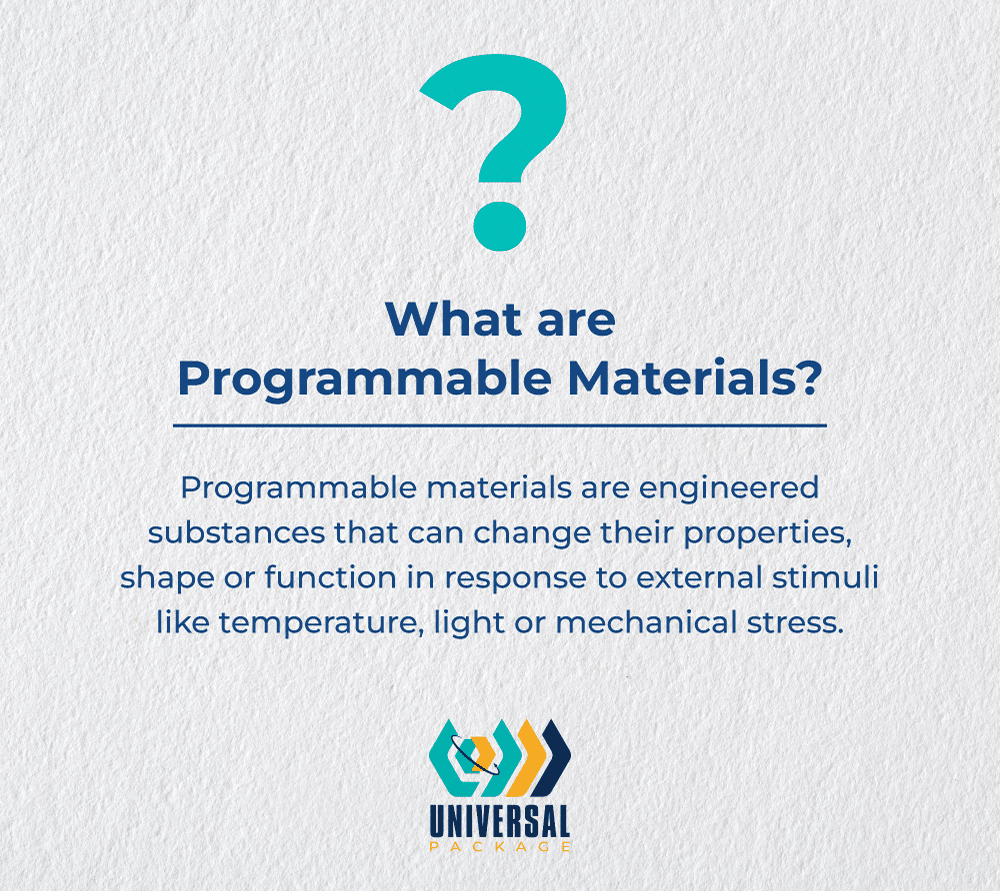
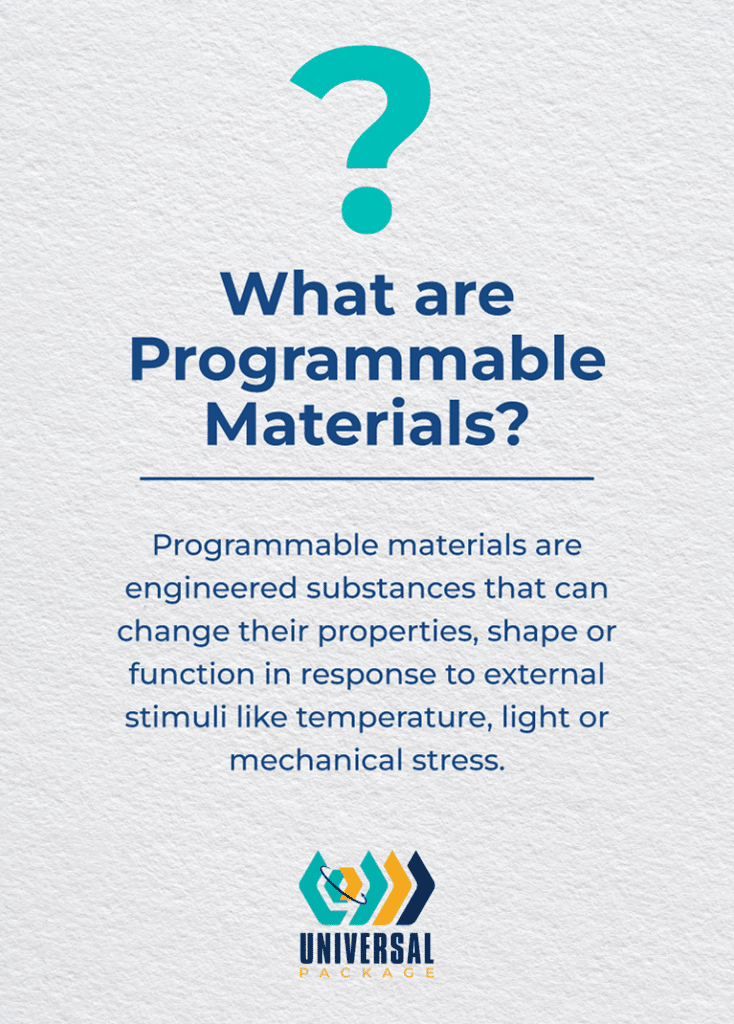
Leveraging Corrugated Plastic Principles in Programmable Material Design
The strategies employed in corrugated plastic offer valuable insights for enhancing programmable materials.
Structural Design: Layering and Ribbing
- Micro-Architectures: By adopting layering and ribbing techniques, engineers can create programmable materials with internal structures that respond dynamically to stimuli. These internal supports distribute forces evenly, enhancing durability and performance.
Enhancing Flexibility and Strength
- Directional Flexibility: Designing materials that flex in specific directions enables applications like flexible electronics, where devices can bend without breaking.
- Impact Absorption: Structures inspired by corrugated designs can absorb energy, providing protection in packaging or protective gear.
Achieving Lightweight yet Durable Structures
- Material Efficiency: Using only the necessary amount of material reduces weight—a principle crucial in aerospace and automotive industries where every gram counts.
- Design Efficiency: Lightweight materials lower transportation costs and reduce energy consumption, contributing to sustainability.
Incorporating Sustainability
- Eco-Friendly Materials: Integrating sustainable practices leads to programmable materials that are both advanced and environmentally responsible, reducing their carbon footprint.
By harnessing these design principles, industries can develop materials that not only meet but exceed modern demands.
Innovative Applications Inspired by Corrugated Plastic
Industries across the globe are discovering transformative uses for programmable materials inspired by the design principles of corrugated plastic. This versatile material provides the blueprint for a wide range of cutting-edge innovations.
Flexible Electronics
One of the most promising applications is in the realm of flexible electronics. With devices becoming increasingly powerful and portable, there is a growing demand for electronics that can withstand the wear and tear of daily use. Inspired by corrugated plastic’s flexibility, companies are developing bendable displays for smartphones and tablets. These advanced screens can not only withstand drops and bends but also enhance the overall user experience by adapting effortlessly to different uses.
Wearable Technology
Similarly, smart textiles have emerged as another application area. By embedding sensors in fabrics, innovators are creating clothing that can monitor health parameters in real-time. These textiles offer comfort and adaptability, making them ideal for everyday use without compromising on monitoring capabilities.
Adaptive Packaging Solutions
The packaging industry is also leveraging the unique properties of corrugated plastic-inspired materials. Smart packaging solutions that adapt their shape to safeguard various products are becoming more prevalent, minimizing the need for different packaging types. Furthermore, temperature-responsive materials are revolutionizing the transportation of perishable goods. By reacting to temperature fluctuations, these materials reduce spoilage and ensure product quality from manufacturer to consumer.
Medical Devices and Biomedical Engineering
In the healthcare sector, the potential of corrugated plastic-inspired materials is profoundly significant. Imagine responsive implants that adjust to bodily changes, offering enhanced comfort and effectiveness to patients. Developments in controlled drug delivery systems are also underway, where biomaterials release medication in response to specific biological signals, allowing for targeted and effective treatment regimens.
Automotive and Aerospace Components
In transportation, programmable materials are paving the way for innovative automotive and aerospace solutions. Morphing structures, inspired by the ribbed design of corrugated plastics, enhance aerodynamics and fuel efficiency by adjusting shape as needed. Additionally, materials engineered to dampen vibrations are enhancing comfort and noise reduction in vehicles and aircraft, contributing to safer and more pleasant transportation experiences.
Each of these applications underscores how principles derived from the simple structure of corrugated plastic are leading to trailblazing developments across diverse sectors. This ingenuity not only meets but often exceeds the modern demands faced by industries today.
Solving Real-World Design Challenges
The fusion of corrugated plastic design with programmable materials presents an array of solutions to complex real-world design challenges, particularly in transportation, storage efficiency, material handling, and product safety. Through innovative use of structure and material properties, industries can create more adaptive, cost-effective, and efficient solutions.
Addressing Transportation and Storage Efficiency
In the realm of transportation and storage, materials exhibiting flexibility and adaptability can be game-changers. By using programmable materials that possess the ability to flatten or expand as required, companies can dramatically improve their storage and shipping protocols. Such materials help optimize space, reducing costs associated with wide-scale storage and transportation logistics. Furthermore, these materials can dynamically manage loads during transit, adapting their properties to prevent damage. As a result, products reach their destinations in pristine condition, enhancing reliability and reducing costs linked to shipping damages.
Improving Material Handling and Reducing Costs
The benefits of programmable materials extend significantly into material handling and cost reduction. Simplifying the assembly process is a pivotal advantage. Programmable materials that adjust shape on demand can minimize or even eliminate the need for complex assembly, ultimately saving both time and labor. The strategic use of such materials reduces unnecessary material wastage and fulfills sustainability goals by enhancing material efficiency. Consequently, businesses witness substantial cost savings, making them more competitive in the market.
Enhancing Product Protection and Safety
Programmable materials also play a crucial role in enhancing the protection and safety of products. These materials offer adaptive protection by hardening upon impact, ensuring superior safeguarding without the constant rigidity seen in traditional materials. Such dynamic properties are particularly beneficial in safety equipment, protective packaging, and applications where impact resistance is crucial. Using this technology, industries can push boundaries in protection standards while retaining flexibility and adaptability.
Facilitating Customization and Scalability
Finally, the versatility of programmable materials supports customization and scalability, which are vital for catering to unique client demands in a fast-paced market environment. The ability to manufacture materials on demand, tailored to specific needs, not only accelerates the production process but also allows businesses to provide customized solutions swiftly and efficiently. This adaptability offers businesses a significant edge, allowing them to scale operations as needed and meet varied consumer requirements. Leveraging these programmable properties enhances the overall capability of companies to innovate while addressing real-world challenges efficiently.
Challenges in Implementing Programmable Materials
Implementing programmable materials into everyday applications, while innovative, is not without its challenges. These obstacles can be broadly categorized into technical limitations and economic factors that, if not addressed, may hinder the broad adoption and implementation of such advanced materials.
Technical Limitations
One of the primary technical challenges in deploying programmable materials is the complexity of manufacturing processes. These advanced materials often require intricate production techniques that are not only costly but also time-consuming. For instance, developing 4D printed objects, which can change shape or function over time, demands highly specialized equipment and knowledge, making widespread manufacturing a daunting task for many companies.
Another significant hurdle is the issue of material longevity. Ensuring that programmable materials perform consistently and reliably under a variety of conditions is essential. For example, while self-healing polymers are engineered to repair damage over time, maintaining their functionality under continuous use poses a challenge. Achieving long-term durability without costly maintenance requires continual advancements in material science.
Economic Factors
Economic concerns also play a critical role in the adoption of programmable materials. Development costs are notably high, often necessitating significant initial investments that can be prohibitive for smaller companies or startups. The costs associated with research, development, and scaling production can be substantial, potentially limiting accessibility to only larger, well-funded organizations.
Moreover, market adoption presents its own set of challenges. Convincing industries to transition to new material technologies requires more than highlighting potential benefits; it necessitates demonstrating a clear return on investment. Companies must be assured that the performance advancements gained from programmable materials justify the expense, both in terms of cost and risk. For instance, transitioning from traditional materials to shape-memory alloys or other smart materials means re-evaluating existing processes and potentially investing in new equipment and training.
Potential Solutions
Addressing these challenges demands strategic approaches. Investing heavily in research and development (R&D) is crucial for overcoming technical barriers and reducing production costs over time. Advancements in automation and materials science can make complex manufacturing processes more efficient and less expensive.
Collaboration serves as another effective strategy to facilitate the adoption of programmable materials. Partnerships between academia, industry, and government can speed up innovation and reduce barriers to market entry. Universities can provide vital research and development support, while governmental incentives can lower financial risks associated with adopting new technologies.
Through these combined efforts, the challenges of implementing programmable materials can be systematically addressed, paving the way for transformational innovations across various sectors.
Benefits of Integrating Corrugated Plastic Design Principles into Programmable Materials
Integrating the design principles of corrugated plastic into the development of programmable materials offers a range of benefits across various industries.
Sustainability
Sustainability is at the forefront of material design, and the principles of corrugated plastic enable the creation of eco-friendly, durable materials. The use of recyclable plastics and material efficiency reduces waste and promotes resource conservation. Programmable materials that can adapt and perform multiple functions also contribute to sustainability by reducing the need for multiple materials or products.
Cost Savings
The design principles of corrugated plastic also offer cost savings across the board. The lightweight yet durable nature of programmable materials reduces transport costs and energy usage. Furthermore, the ability to customize materials on demand and reduce wastage ensures material efficiency, leading to cost savings during production.
Enhanced Performance
Materials that adapt and respond to external stimuli offer advanced performance capabilities. By incorporating the principles of corrugated plastic into programmable materials, industries can develop products that are more resilient, flexible, and efficient.
Improved Safety and Protection
The structural ingenuity of corrugated plastic can enhance the protective features of materials. By incorporating these properties into programmable materials, companies can develop products that sense and respond to impact, providing superior safety and protection to both products and consumers.
Enhanced Efficiency and Convenience
Materials that can adapt to specific conditions or functions offer unparalleled convenience and efficiency. Programmable materials that change shape, respond to temperature, or adjust to specific needs are revolutionizing industries like transportation, packaging, and construction. These materials not only enhance efficiency but also provide convenience for everyday use.
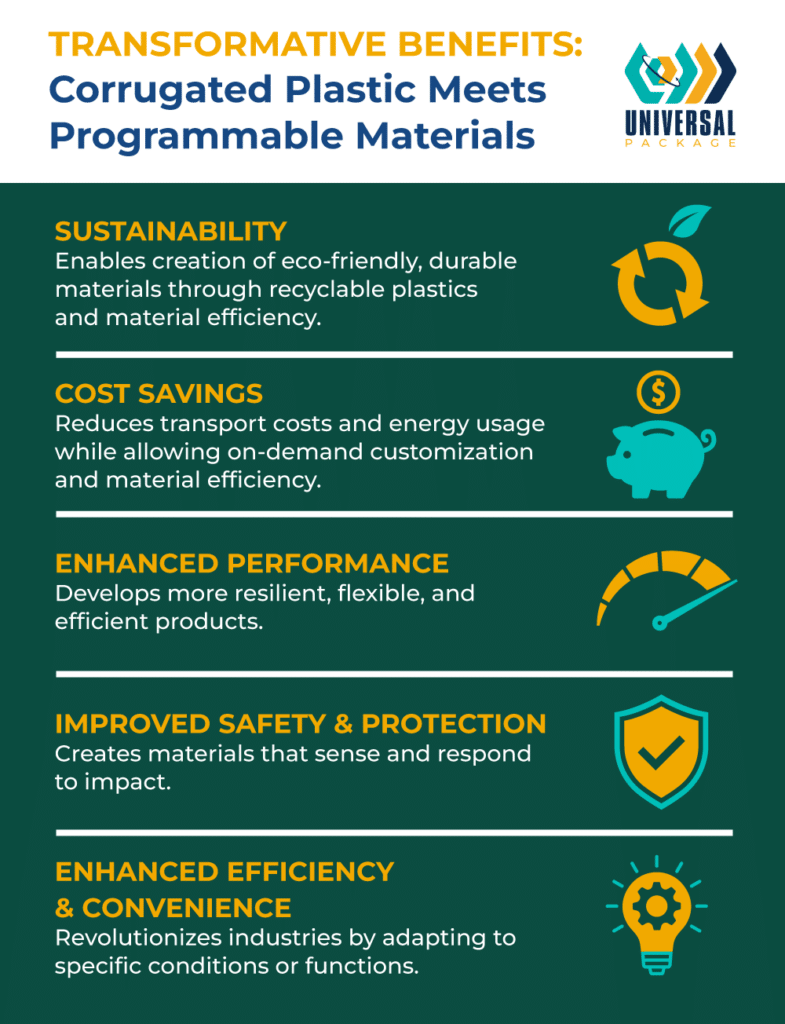
Ready to Pioneer the Material Revolution?
The transformative potential of corrugated plastic-inspired innovations is setting a new standard in the future of programmable materials. By leveraging the structural efficiencies and versatility derived from these materials, industries can achieve unprecedented advancements in sustainability, cost-effectiveness, and performance. This breakthrough extends beyond theory into practical applications that redefine market standards across diverse sectors such as electronics, healthcare, and aerospace.
At the heart of these advancements lies the ability to engineer materials that adapt seamlessly to ever-changing environments. From developing lighter, yet more robust automotive components to creating more efficient packaging solutions, the principles inspired by corrugated plastic are propelling industries toward a more adaptive future.
Universal Package stands at the intersection of this innovation. By offering expertise in custom packaging solutions, we empower businesses to harness the benefits of programmable materials tailored to exact specifications and unique industry needs. Our sustainable and customizable design approaches ensure that every packaging solution not only meets functional demands but also supports environmental stewardship.
Explore how Universal Package can be your partner in integrating cutting-edge materials into your next project. Contact us today to discover how our innovative packaging solutions can transform your industry dynamics. Let’s pioneer the material revolution together, transforming possibilities into realities that forge a path toward a smarter, more adaptable world.