Material handling systems are the lifeblood of any efficient warehouse, manufacturing plant, or distribution center. In today’s fast-paced industrial landscape, optimizing these systems isn’t just beneficial—it’s essential. Efficient material handling leads to increased productivity, reduced operational costs, and a safer work environment. Mismanaged systems, on the other hand, can result in bottlenecks, increased labor costs, and heightened risk of workplace accidents.
At Universal Package, we understand the critical role these systems play in your operations. With the right strategies, you can transform your material handling processes to meet the demands of modern supply chains.
In this article, we’ll explore four powerful tips that can revolutionize your material handling systems, providing practical solutions you can implement to enhance efficiency, safety, and overall operational success.
1. Assess and Optimize Your Warehouse Layout
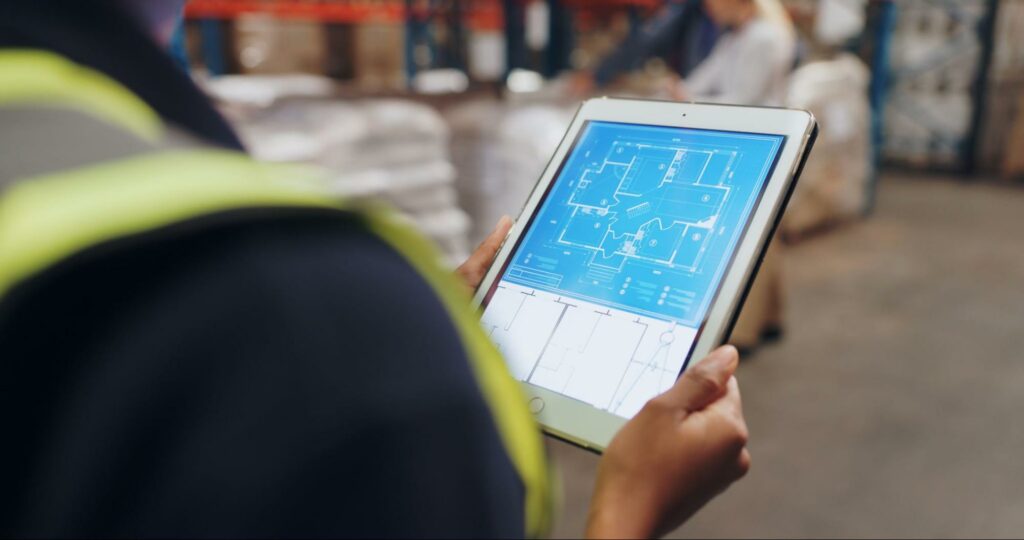
An optimized warehouse layout is the foundation of efficient material handling systems. Over time, warehouses can become cluttered and disorganized, leading to inefficiencies that hamper productivity. By assessing and reorganizing your space, you can enhance workflow, maximize storage capacity, and boost overall efficiency.
Analyze Current Operations
Begin by conducting a comprehensive analysis of your current warehouse operations:
- Observe Workflow Patterns: Track how materials move through your facility. Identify areas where delays or congestion occur.
- Employee Input: Consult with staff members who interact daily with the systems. Their insights can reveal practical issues and potential solutions.
- Use Analytical Tools: Implement time-motion studies, value stream mapping, and process flow analysis to quantify inefficiencies.
Are your employees spending excessive time walking between stations? Do certain areas consistently experience traffic bottlenecks?
By answering these questions, you can pinpoint specific problem areas that require attention.
Optimize Space Utilization
Effective space utilization is crucial for improving material handling efficiency:
- Vertical Storage Solutions: Implement pallet racking systems, mezzanines, or automated storage and retrieval systems (AS/RS) to capitalize on unused vertical space. This approach increases storage capacity without expanding your facility’s footprint, freeing up valuable floor space for movement and operations.
- Optimized Aisle Widths: Carefully consider aisle widths to balance storage density with accessibility. Narrow aisles increase storage capacity but may require specialized equipment. Wider aisles facilitate easy movement of forklifts and reduce the risk of accidents, enhancing safety and operational flow.
- Strategic Placement: Arrange inventory based on demand frequency. Position high-turnover items closer to shipping and receiving areas to reduce picking time. Utilize ABC analysis to categorize inventory and optimize placement accordingly.
According to the Warehouse Education and Research Council (WERC), optimizing warehouse layouts can improve efficiency by up to 30%. This significant enhancement underscores the value of strategic space utilization.
Leverage Technology for Layout Planning
Modern technology offers sophisticated tools for warehouse layout optimization:
- Software Solutions: Utilize programs like AutoCAD, SketchUp, or specialized warehouse layout software that allow for precise floor planning. These tools enable you to model different configurations and simulate workflow changes before implementing them physically.
- Simulation Modeling: Perform scenario analysis to predict the impact of layout changes on operations. This method helps in making data-driven decisions that minimize disruptions.
Implement Lean Principles
Adopting lean methodologies focuses on eliminating waste and enhancing processes:
- 5S Methodology: Implement Sort, Set in order, Shine, Standardize, and Sustain to maintain an organized and efficient warehouse. This systematic approach ensures cleanliness, organization, and adherence to best practices.
- Continuous Improvement (Kaizen): Encourage a culture where employees are engaged in ongoing improvements. Small, incremental changes can lead to substantial efficiency gains over time.
By continuously evaluating and refining your processes, you create a culture of efficiency that permeates all levels of your organization.
Enhance Safety Through Layout Design
An optimized layout also improves safety:
- Clear Aisles and Pathways: Ensure that aisles are free from obstructions to prevent accidents.
- Designated Zones: Separate pedestrian walkways from vehicle paths using barriers and clear signage.
- Proper Lighting: Enhance visibility in all areas to reduce the risk of accidents.
A safe warehouse not only protects your employees but also minimizes downtime due to incidents.
2. Implement Advanced Material Handling Equipment
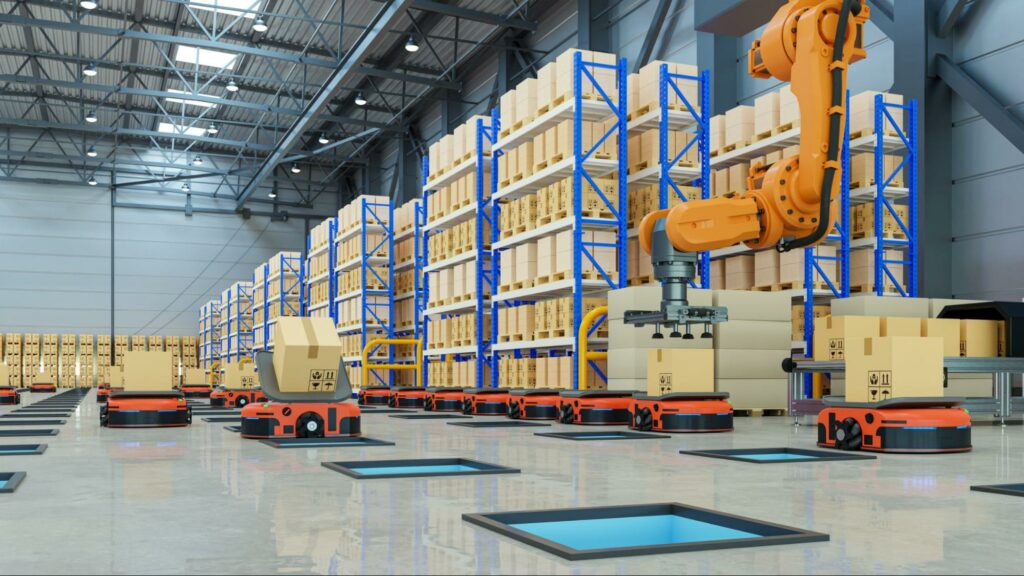
Investing in advanced equipment is crucial for modernizing your material handling systems. Upgrading machinery and embracing automation can significantly enhance operational efficiency and position your company at the forefront of industry advancements.
Embrace Automation
Automation technologies can revolutionize your operations:
- Automated Guided Vehicles (AGVs): Driverless vehicles that transport materials within the warehouse, improving efficiency and reducing labor costs.
- Conveyor Systems: Automated conveyors streamline the movement of goods, reducing manual handling and the potential for human error.
- Robotic Pickers: Robots equipped with advanced sensors and software can handle repetitive tasks with precision, increasing picking speed and accuracy.
Automation also enables businesses to scale operations without proportional increases in labor. “Automated and efficient warehouses in the survey were 76% more likely to boost inventory accuracy to 99% or higher, 36% more likely to have reduced labor costs an average of 3% per year, and 40% more likely to consistently ship within one day of an order’s placement,” according to Robotics Business Review.
Integrate Advanced Technologies
Beyond automation, integrating advanced technologies can further enhance your material handling systems:
- Internet of Things (IoT): Equip devices and equipment with sensors that communicate data in real-time, allowing for proactive adjustments and maintenance.
- Artificial Intelligence (AI) and Machine Learning: Use AI algorithms to predict demand, optimize routing, and improve decision-making processes.
Upgrade Existing Equipment
Modernizing equipment enhances performance and safety:
- Energy-Efficient Machines: Newer models consume less power, reducing operational costs and environmental impact.
- Enhanced Safety Features: Equipment with the latest safety technology protects workers and reduces liability.
- Retrofitting: Update existing machinery with modern components to extend lifespan and improve functionality.
Invest in Ergonomic Solutions
Ergonomic equipment is vital for worker health and productivity:
- Adjustable Workstations: Allow customization to individual worker needs, reducing strain.
- Ergonomic Tools: Tools designed to minimize repetitive stress injuries contribute to long-term employee well-being.
A study by the Journal of Occupational and Environmental Medicine found that ergonomic interventions can lead to a 25% reduction in musculoskeletal disorders, highlighting their importance in a material handling context.
Implement Predictive Maintenance
Predictive maintenance keeps your equipment running smoothly:
- Condition Monitoring: Use sensors to monitor equipment health indicators like vibration, temperature, and lubricants.
- Data Analysis: Analyze collected data to predict failures before they occur, allowing for scheduled maintenance that minimizes downtime.
Implementing predictive maintenance can reduce maintenance costs by 25% and eliminate breakdowns by up to 75%, according to a study by the U.S. Department of Energy.
3. Enhance Inventory Management Practices
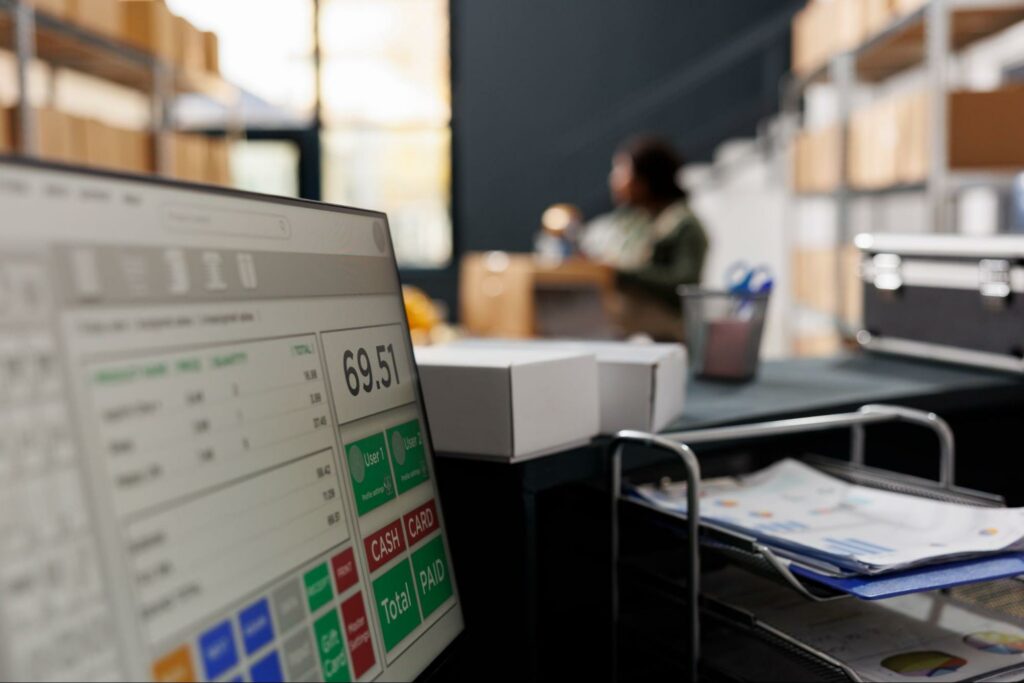
Efficient inventory management is vital for smooth material handling systems. Implementing advanced strategies can reduce costs, improve service levels, and enhance customer satisfaction.
Adopt Just-In-Time Inventory Systems
Just-In-Time (JIT) inventory aligns stock levels with production schedules:
- Reduces Excess Stock: Minimizes storage costs and waste by ordering inventory only as needed.
- Improves Cash Flow: Less capital is tied up in unused stock, freeing resources for other operational needs.
However, JIT requires:
- Accurate Forecasting: Use historical data and market trends to predict demand accurately.
- Reliable Suppliers: Establish strong relationships with suppliers to ensure timely deliveries.
Utilize Technology for Inventory Tracking
Implementing technology enhances accuracy and visibility:
- Barcode Scanning and RFID: Automate data capture for real-time tracking of inventory movement, reducing manual errors.
- Inventory Management Systems (IMS): Software solutions provide comprehensive management of inventory levels, orders, and shipments.
A study by GS1 found that companies using RFID technology saw inventory accuracy rates of 99%, significantly reducing the cost associated with inventory errors.
Implement Regular Inventory Audits
Regular audits maintain inventory accuracy:
- Cycle Counting: Regularly count subsets of inventory to identify discrepancies early without disrupting operations.
- Full Physical Inventories: Conduct comprehensive counts periodically to reset and validate inventory records.
Maintaining accurate inventory records enhances decision-making and customer satisfaction by ensuring product availability.
Optimize Inventory Levels
Balancing inventory levels is critical:
- Economic Order Quantity (EOQ): Calculate the optimal order quantity that minimizes total holding and ordering costs.
- Safety Stock Management: Determine appropriate safety stock levels to protect against demand variability and supply delays.
- ABC Analysis: Categorize inventory based on value and turnover rate to prioritize items that require more attention.
Maintaining optimal inventory levels ensures reduced costs and improved customer satisfaction.
Implement Demand Forecasting Techniques
Accurate demand forecasting is essential:
- Statistical Methods: Use time series analysis, regression models, and machine learning algorithms to predict future demand.
- Collaborative Planning: Work with suppliers and customers to share information and improve forecast accuracy.
Improved forecasting reduces stockouts and overstock situations, enhancing customer satisfaction and reducing costs.
4. Train and Empower Your Workforce
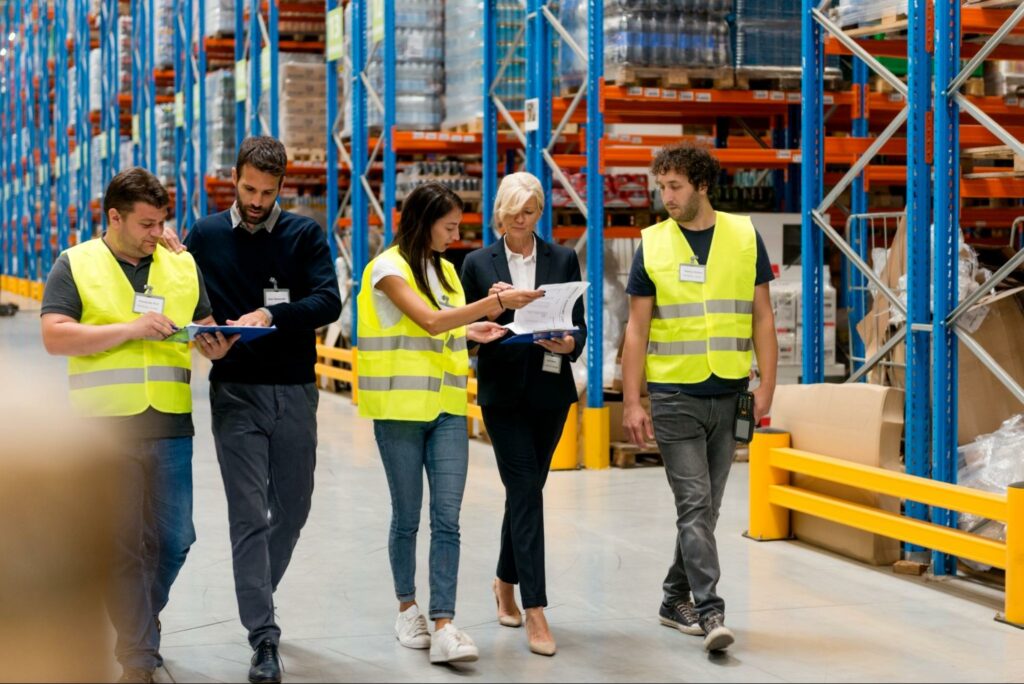
Your employees are the backbone of your material handling systems. Investing in their development leads to a more efficient, motivated, and innovative workforce.
Provide Comprehensive Training Programs
Effective training ensures employees:
- Operate Equipment Safely and Efficiently: Proper use reduces accidents and prolongs equipment life.
- Understand Processes and Protocols: Increases productivity and consistency across operations.
Consider various training methods:
- On-the-Job Training: Hands-on experience under supervision.
- Classroom Instruction: Provides theoretical knowledge and safety protocols.
- E-Learning Modules: Flexible learning opportunities accessible at any time.
Regularly update training programs to reflect new technologies, equipment, and industry best practices.
Encourage Continuous Learning and Skill Development
Promote a culture of continuous improvement:
- Cross-Training: Educate employees in multiple roles to increase flexibility and understanding of the overall operation.
- Professional Development: Offer certifications and advanced training programs to foster career growth.
- Mentorship Programs: Pair less experienced employees with seasoned staff to facilitate knowledge transfer.
By investing in your employees’ growth, you enhance their engagement and retention.
Foster a Safety-First Culture
Safety is paramount in material handling environments:
- Develop Comprehensive Safety Programs: Include regular training, clear policies, and accessible resources.
- Engage Employees: Involve staff in safety committees and encourage reporting of hazards.
- Monitor and Reward: Track safety metrics and recognize teams or individuals who exemplify safe practices.
According to the Occupational Safety and Health Administration (OSHA), companies with strong safety cultures experience fewer accidents, resulting in less downtime and lower insurance costs.
Empower Employees Through Inclusion
Involving employees in decision-making fosters ownership and innovation:
- Suggestion Programs: Implement structured systems for employees to submit ideas for improvements.
- Open Communication Channels: Encourage regular feedback and hold meetings where employees can voice concerns and suggestions.
Encouraging employee involvement not only leads to practical improvements but also enhances employee satisfaction and retention.
Recognize and Reward Performance
Acknowledging employee contributions boosts morale:
- Performance Incentives: Offer bonuses or other rewards for meeting or exceeding targets.
- Public Recognition: Highlight achievements in company communications or meetings.
Recognition programs reinforce desired behaviors and encourage a high-performance culture.
Maximize Operational Success with Strategic Material Handling Enhancements
Transforming your material handling systems is a multifaceted endeavor that can lead to significant benefits:
- Optimized Warehouse Layout: Enhances flow, maximizes space, and improves safety.
- Advanced Equipment and Technology: Increases efficiency, reduces costs, and positions your operation at the industry’s cutting edge.
- Efficient Inventory Management: Reduces holding costs, improves accuracy, and enhances customer satisfaction.
- Empowered Workforce: Drives productivity, fosters innovation, and strengthens organizational culture.
By implementing these powerful tips, you can unlock the full potential of your material handling systems, positioning your operations for greater success in a competitive marketplace.
Ready to revolutionize your material handling systems? At Universal Package, we’re committed to providing customized packaging and material handling solutions tailored to your specific needs. Our expertise spans various industries, and our dedication to quality ensures you receive solutions that enhance efficiency and safety.
Contact us today to discover how we can help transform your operations and drive your business forward.