In today’s industrial marketplace, businesses are constantly seeking ways to streamline operations, reduce waste, and protect their goods during transit or storage. Corrugated plastic containers have emerged as a popular choice for companies looking to balance efficiency, durability, and overall sustainability in their packaging solutions. This article explores the many advantages of corrugated plastic containers, highlighting how they can ease material handling challenges across industries such as automotive, electronics, construction, and medical.
By understanding how these containers function and why they excel in different scenarios, decision-makers can make more informed choices about whether corrugated plastic is the right fit for their operations. From discussing design attributes to sharing practical adoption tips, this overview provides actionable insights to help organizations optimize their packaging strategies.
Benefits of Corrugated Plastic Containers
Corrugated plastic containers are created by bonding thin layers of plastic into a fluted arrangement sandwiched between smooth outer sheets. This combination forms a lightweight solution that maintains structural strength. Compared to single-layer plastics, their fluted structure helps disperse impacts, providing extra cushioning for items during transport or storage.
Because they are inherently moisture-resistant, corrugated plastic containers are often favored over fiberboard in settings where humidity or contact with liquids is a concern. The outer plastic layers help guard against dust, dirt, and potential exposure to contaminants, making these containers suitable for environments with stricter cleanliness standards, including certain medical and pharmaceutical processes. Companies that need tailored packaging can also rely on custom packaging capabilities offered by specialized providers. Such customization ensures containers can be adapted to meet precise operational needs, whether it’s adding compartments, secure lids, or specialized labeling.
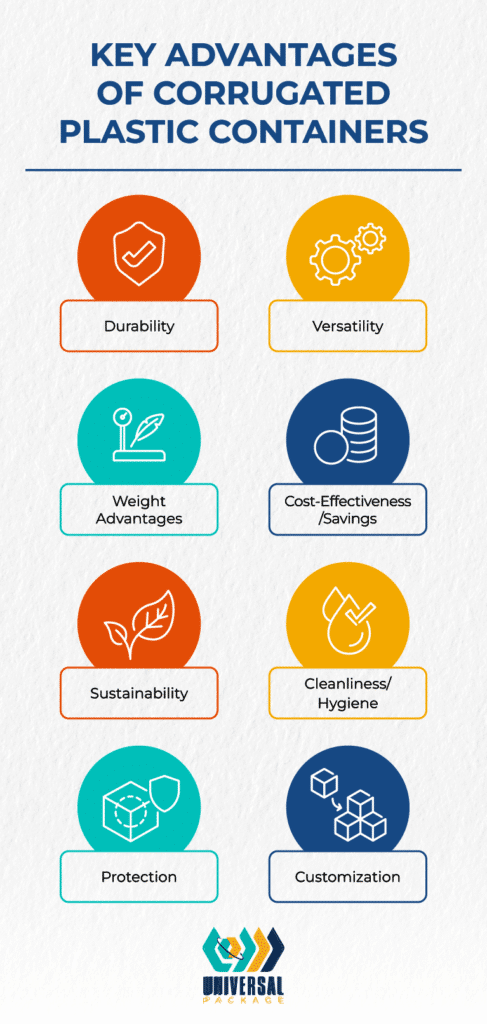
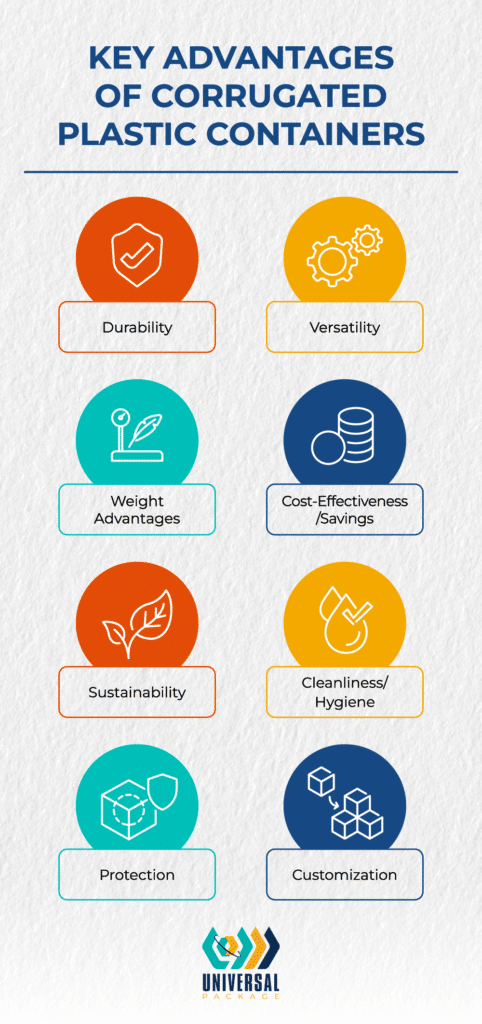
1. Durability: A Prime Consideration
Durability is one of the major selling points of corrugated plastic containers. By design, these containers can withstand rough handling, heavier loads, and repeated use cycles. Many standard solutions prone to tearing or water damage (such as traditional cardboard boxes) lack the resilience that plastic fluting provides. For businesses that frequently transport goods over long distances, rugged packaging can reduce product damage rates and lower the cost of replacements or repairs.
While robust construction can demand a higher upfront investment, the extended lifespan often offsets initial expenses. With thoughtful reuse, companies can avoid purchasing large quantities of disposable boxes over time. For additional perspectives on the benefits of reusable packaging models, consult this overview of benefits of reusable packaging.
2. Versatility for Varied Applications
Another key benefit of corrugated plastic containers is their adaptability. Because they can be manufactured in different sizes, shapes, and configurations, they integrate seamlessly across a broad spectrum of industries. Below are a few scenarios in which their versatility proves particularly valuable:
- Automotive parts shipping: Large or oddly shaped components can be padded with inserts to prevent shifting or breakage.
- Electronics handling: The moisture-resistance qualities of corrugated plastic help safeguard sensitive circuitry.
- Construction site storage: Tools and materials often require organized compartments to reduce on-site clutter and protect expensive equipment.
- Medical and pharmaceutical settings: For applications requiring a hygienic environment, sealed edges and easy-to-clean surfaces help maintain product integrity.
- Trade show exhibits: Reusable, stackable containers allow frequent setup and teardown, reducing overall logistics costs for events.
The ability to customize internal compartments or add protective foam further broadens the scope of what corrugated plastic containers can handle. As an example, some companies rely on different types of custom corrugated containers to tackle oddly shaped items or fragile components. In situations where even greater rigidity is needed, options like cut and weld custom totes further enhance protection.
3. Weight Advantages for Logistics Efficiency
Despite being capable of supporting heavy loads, corrugated plastic containers tend to be lighter than many other sturdy packaging materials, such as solid plastic crates or metal racks. Their reduced weight can yield benefits throughout the supply chain:
- Lower shipping costs: Lighter packaging can mean lower freight fees, especially for large shipments traveling frequently.
- Better fuel efficiency: In high-volume transport operations, shaving off even a small amount of weight can accumulate significant fuel savings over time.
- Easier manual handling: Warehouse workers often appreciate packaging that is both sturdy and simple to lift, improving workplace ergonomics.
These factors contribute to faster loading and unloading processes. Minimizing the strain on workers can reduce on-site injuries and help maintain overall productivity. Additionally, light-yet-durable containers prove helpful when integrating automated systems, as they are typically easier for mechanized equipment to manage.
4. Cost-Effectiveness and Potential Savings
Although corrugated plastic containers can cost more initially than single-use packaging alternatives, the total cost of ownership often becomes more favorable as time passes. Each reusable container replaces multiple throwaway boxes, leading to fewer recurring purchases. Moreover, the high durability of corrugated plastic helps reduce the likelihood of product damage, potentially saving even more money.
For organizations dealing with delicate or high-value items, the risk of shipping damage is an ever-present concern. Investments in packaging that protects against moisture, impacts, and other hazards can pay for themselves by helping prevent losses.
When analyzing cost-effectiveness, it’s also worthwhile to account for disposal expenses. Many disposable boxes must be broken down, compacted, or paid for as waste. By contrast, reusables integrate into a circular system where containers are returned, inspected, and redistributed.
5. Sustainability as a Key Driver
For companies focused on environmental stewardship, corrugated plastic containers can align with broader sustainability initiatives. Several aspects make them an appealing approach:
- Reduced waste generation: Since they are used multiple times, these containers minimize the volume of single-use packaging materials entering landfills.
- Recyclability: Most corrugated plastic can be reprocessed at the end of its life. Check local recycling programs to ensure materials are accepted.
- Lower carbon footprint over time: By lowering the frequency of replacements, resource consumption goes down. Their light weight can also translate into lower greenhouse gas emissions during transport.
As sustainability has become more central to supply chain decision-making, corrugated plastic packaging fits well within evolving corporate strategies. When paired with returnable packaging strategies that enable containers to circulate back to warehouses or distribution centers, businesses can create a closed-loop system with minimum waste.
6. Cleanliness and Hygiene Benefits
In certain industries—most notably medical, pharmaceutical, and food processing—strict sanitation measures are non-negotiable. Corrugated plastic containers have a smooth, non-porous surface that can be cleaned more easily than cardboard alternatives, which may harbor bacteria in damp conditions.
Even in less strictly regulated environments, cleanliness can be an advantage when preventing cross-contamination between different product categories. Whether it’s electronics, food items, or sensitive materials, the ability to wipe down containers quickly helps ensure safe operations.
7. Protecting Goods in Transit and Storage
Maintaining product integrity is central to any packaging strategy. Corrugated plastic containers often come with features that help mitigate the risks of shock, vibration, or moisture infiltration during transit. Their fluted core can act as a cushion, and reinforced corners add extra stability. This protective design can extend to storing goods in environments with fluctuating climate conditions.
In warehousing, stackability is another perk. Many corrugated plastic designs nest together securely, reducing the likelihood of tipping or collapsing as products shift. By avoiding potential damage through better stacking, companies can keep their goods safer and reorder fewer items. For more data on minimizing losses from poor packaging, see the hidden costs of shipping damage.
8. Customization: A Critical Factor for Specific Needs
Across industries, product shapes, sizes, and fragility levels can vary tremendously. Corrugated plastic containers can be modified with dividers, specialized foam inserts, or lids fitted with locking mechanisms to accommodate these diverse requirements. Below are examples of customizations:
- Protective padding: Highly breakable items may need foam inserts or other forms of interior dunnage that conform closely to the product’s contours. Consider exploring foam assemblies designed to protect delicate components.
- Tamper-evident features: Security seals or locking mechanisms can be integrated for extra protection in transit.
- Easy-carry handles: Ergonomic designs make containers simpler to carry, particularly in manual handling environments.
- Label holders: Insertable pockets or surfaces that allow barcode labels, shipping tags, or instructions to be attached securely without damaging the container.
Implementation Tips for Adopting Corrugated Plastic Containers
Transitioning to a new packaging system begins with analyzing current challenges. Are damage rates high due to subpar protective materials? Are costs for disposable boxes continually affecting the bottom line? By pinpointing these issues, businesses can determine whether corrugated plastic is a relevant solution.
Below are a few suggestions for a smoother adoption process:
- Conduct a pilot phase: Test small batches of corrugated plastic containers on selected products or shipping routes to gather real-world data.
- Collaborate with specialists: Engaging a knowledgeable partner helps ensure that container designs meet all relevant specifications and that processes are integrated properly.
- Train employees: Provide guidelines on handling, cleaning, and identifying containers that need repairs or replacements to maximize container lifespan.
- Evaluate ROI: Track metrics such as damage reduction, packaging reuse rate, and disposal costs to quantify the impact.
An organized roll-out, supported by proper training and consistent evaluation, generally leads to higher adoption success and immediate realization of benefits.
Addressing Potential Concerns
While corrugated plastic offers many strengths, businesses may still have concerns regarding:
- Initial investment costs: The upfront expense can be higher than alternatives. However, if paired with a thoughtful reuse strategy, corrugated plastic containers often prove more economical over time.
- Recyclability programs: Although plastic is recyclable, it is essential to ensure that local facilities accept the specific material type.
- Maintenance and cleaning: Reusable containers should be cleaned periodically. Companies must establish quality checks to ensure all reusable packaging remains in good condition.
Weighing these considerations against the potential long-term gains can help organizations decide whether corrugated plastic aligns with current corporate strategies and budgets.
Future Outlook in Industrial Packaging
The industrial packaging landscape is evolving, with innovations spanning tracking technology, more efficient materials, and automated handling solutions. Corrugated plastic containers are well-positioned to integrate with these advancements. As automation in warehouses grows, the precise dimensions and consistent shapes of corrugated plastic often facilitate compatibility with robotic systems. Over time, seamless integration of smart tracking chips or sensors could help organizations gather data on container use and product safety conditions throughout transit.
Continued research into composite materials may also yield next-generation plastics that further enhance durability while minimizing environmental impact. Ultimately, businesses that remain adaptable, informed, and open to continual improvement are likely to stay ahead in a competitive market.
Optimizing Your Supply Chain with Corrugated Plastic
Corrugated plastic containers stand apart as a flexible, durable, and often cost-effective option for industries that require reliable packaging. Their design resists moisture, shock, and everyday wear, making them well-suited for repeated use. By emphasizing reusability and often supporting recycling, they help companies align with sustainability initiatives while also reducing waste management expenses.
If you’re ready to learn how such solutions can optimize your own supply chain, explore corrugated plastic containers solutions from a leader in the industry. You can also contact the Universal Package team to discuss custom configurations tailored to your industry’s needs. Whether it’s maximizing protection, reducing shipping costs, or meeting green objectives, corrugated plastic containers can be a worthwhile addition to your overall packaging strategy.