Throughout the supply chain, products face significant risks during handling, storage, and transit. To safeguard them, businesses rely on packaging solutions that provide maximum protection while minimizing costs. Foam dunnage is a popular choice for its ability to secure products of different shapes and sizes, making it a staple in industries such as automotive, electronics, and medical.
This guide will explore everything you need to know about foam dunnage, including its properties, applications, foam types, customization options, and why you should choose Universal Package for your foam dunnage needs.
Understanding Foam Properties
Foam is a versatile material favored in industrial packaging for its ability to disperse energy and its adaptability to different shapes. It is available in two main types:
- Open-Cell Foam: This type features interconnected pores that give it a softer texture and excellent cushioning—ideal for delicate items.
- Closed-Cell Foam: With individual air pockets, this foam is denser and more rigid, offering superior resistance to moisture and chemicals.
Both types offer several essential benefits, including:
- Excellent shock absorption and vibration reduction.
- Lightweight construction that can help lower shipping costs.
- Resistance to moisture and chemicals (especially in closed-cell configurations).
- Flexibility that allows foam to be customized to fit specific shapes and sizes.
Foam dunnage meets a variety of industry challenges through these characteristics, remaining a cornerstone of secure packaging solutions.
Applications of Foam in Industrial Packaging
Foam dunnage safeguards products at every stage of the supply chain. Its benefits vary across industries:
- Automotive: Foam stabilizes and cushions components, minimizing movement and damage during transit.
- Electronics: Sensitive devices, like circuit boards, benefit from foam that absorbs shocks and helps minimize the risk of static discharge.
- Medical: Custom foam protects equipment of various sizes and shapes, with closed-cell options offering extra resistance against moisture.
- Military: In high-impact environments, foam protects critical equipment and supplies by absorbing shocks and contributing to overall durability.
- Construction: Foam is used to secure fragile building components and precision-engineered parts, helping to prevent breakage during transport.
Regardless of the industry, using foam helps reduce breakages, increasing supply chain efficiency, and customer satisfaction.
Detailed Breakdown of Foam Types
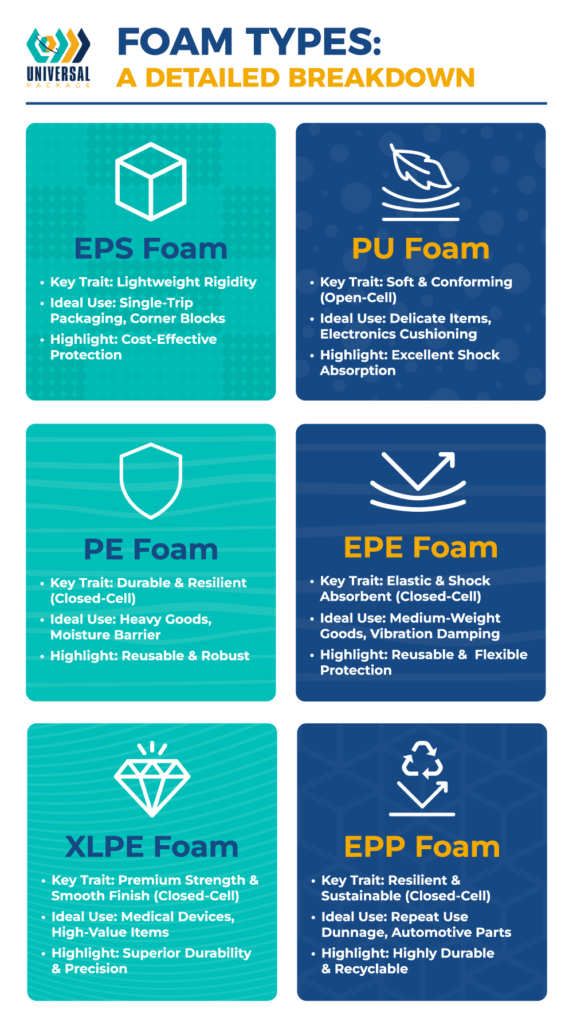
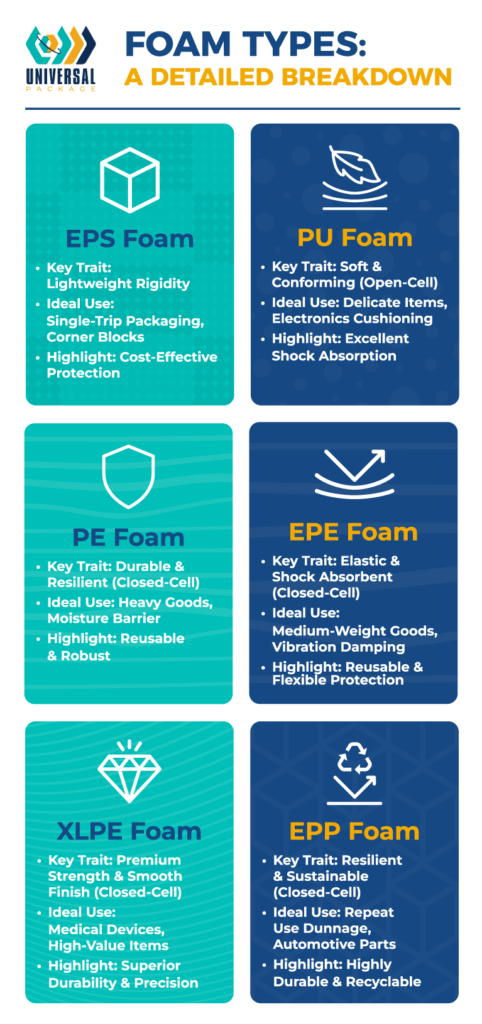
Choosing the right foam depends on your product’s needs and industry standards. Here is an overview of the most common foam types:
Expanded Polystyrene (EPS) Foam
- Characteristics: A lightweight, rigid foam made from expanded polystyrene beads.
- Applications: Commonly used in disposable packaging, end caps, and corner protectors.
- Pros & Cons: It is economical and effective for short-term protection. While EPS may exhibit brittleness if not produced with optimal manufacturing practices, adjustments such as improved bead-fusion techniques can enhance its structural integrity. Consequently, its suitability for repeated or high-impact applications may be more limited compared to denser foam types.
Polyurethane (PU) Foam
- Characteristics: An open-cell foam known for its soft and compressible quality.
- Applications: Ideal for cushioning delicate electronics and small industrial parts.
- Pros & Cons: PU offers excellent shock absorption and flexibility, making it a popular choice for protecting sensitive items. However, its long-term performance under very heavy loads or in high-humidity environments depends on its specific formulation; some PU variations may experience slight degradation over time under extreme conditions.
Polyethylene (PE) Foam
- Characteristics: A dense, closed-cell foam that balances firmness with lightness.
- Applications: Used for protecting heavy products and industrial equipment.
- Pros & Cons: PE provides durable protection and moisture resistance, although its higher cost is usually justified by its long-term reusability. While PE is available in various densities, it is not quite as lightweight as other materials like EPS.
Expanded Polyethylene (EPE) Foam
- Characteristics: Similar to PE but with improved elasticity.
- Applications: Suitable for medium-weight goods and vibration-sensitive devices.
- Pros & Cons: EPE is reusable and shock absorbent, though it is slightly less rigid compared to standard PE foam.
Crosslinked Polyethylene (XLPE) Foam
- Characteristics: A premium closed-cell foam with enhanced strength and a smooth finish.
- Applications: Ideal for high-precision requirements such as medical devices and military equipment.
- Pros & Cons: XLPE offers superior durability and is well suited for precision cutting, though its higher cost makes it best for high-value applications.
Expanded Polypropylene (EPP) Foam
- Characteristics: An eco-friendly, recyclable closed-cell foam known for its resilience and support of environment-friendly packaging practices.
- Applications: Often used for automotive dunnage and industrial reuse setups.
- Pros & Cons: Expanded Polypropylene is highly durable under repeated stress and supports sustainable practices, though it entails a higher initial investment.
Each foam type, with its unique characteristics and advantages, enhances supply chain resilience by reducing breakages and ensuring products arrive in pristine condition. Selecting the appropriate foam dunnage type boosts both product safety and operational efficiency, making it a wise investment for sustainable and effective packaging strategies.
Factors to Consider When Choosing Foam
Selecting the right foam dunnage involves several important factors:
- Product Fragility and Weight: Heavy or delicate items require different foam properties. Automotive parts might benefit from denser materials like PE or XLPE, while sensitive electronics perform better with the cushioning offered by PU or EPE.
- Shipping Conditions: Consider the transit environment. Closed-cell foams are preferable in conditions where moisture, chemicals, or extended transit times might be of concern. Proper classification and compliance with National Motor Freight Classification guidelines can also influence your foam selection and packaging design.
- Budget and Lifecycle Costs: Materials like EPS might offer lower upfront costs but can incur higher replacement expenses. In contrast, foams like XLPE and EPP, though initially costlier, can offer longer-term savings.
- Environmental Impact: Sustainable options such as EPP support eco-friendly practices by being recyclable and reducing waste.
- Industry-Specific Requirements: Some sectors have unique standards that may necessitate additional features, such as anti-static properties or enhanced chemical resistance.
By carefully weighing these factors, businesses can choose the foam that best meets both performance and budgetary needs, ensuring reliable material handling solutions.
Customization and Design in Foam Dunnage
Modern packaging strategies often employ industrial packaging solutions to ensure a protective, custom fit. The true power of foam dunnage lies in its adaptability. Tailoring foam to fit your specific product not only minimizes movement during transit but also enhances protection. Customization methods include:
CNC Cutting
Computer Numerical Control (CNC) machines enable highly precise cuts tailored to the contours of equipment or irregularly shaped items. This method ensures a consistent protective fit every time.
Molding and Fabrication
Foam can be molded and fabricated into customized shapes for non-standard product dimensions. This process allows for layered or composite structures that provide targeted cushioning and support.
Advanced Design Software
CAD tools play an essential role in the customization process by allowing designers to create detailed digital models of foam dunnage. These tools help optimize the design for efficient material use and adaptability while ensuring that the foam fits the product precisely. Although CAD systems are widely recognized for their support in optimizing material usage, claims regarding specific simulations of load distributions and direct reductions in shipping costs are broader benefits inferred from enhanced design efficiency rather than direct outcomes.
These customization strategies not only improve product safety but also streamline packing processes and reduce overall operational costs, ultimately delivering effective custom packaging solutions.
Why Choose Universal Package for Your Foam Dunnage Needs?
Universal Package has over twenty years of experience in designing and manufacturing custom foam packaging for a diverse range of industries. Our commitment to quality, innovation, and sustainability has made us a leading supplier of packaging solutions for businesses worldwide. When you choose Universal Package, you benefit from:
- Expertise: Our team of engineers and designers have extensive experience in foam fabrication, allowing us to deliver high-quality, tailored solutions that meet your unique requirements.
- Industry Knowledge: We possess deep insights into the distinct requirements of sectors such as automotive, electronics, medical, military, and construction.
- Material Variety: Our comprehensive range of foam options allows us to tailor solutions to suit various products and conditions, providing truly Secure Packaging Solutions.
- Tailored Customization: Leveraging precision tools like CNC cutting and sophisticated CAD design, we shape foam packaging to fit your products perfectly.
- Sustainability: We are committed to using reusable and recyclable materials, aligning our packaging solutions with principles advocated by the Sustainable Packaging Coalition for Environment-Friendly Packaging.
- Customer Support: From material selection to design implementation, our expert team supports you every step of the way, ensuring that your packaging enhances supply chain efficiency and product protection.
At Universal Package, we understand the importance of effective packaging in ensuring product safety and operational efficiency. By combining our industry-specific knowledge with our commitment to quality and sustainability, we provide businesses with reliable and customized foam dunnage solutions that support their unique requirements.
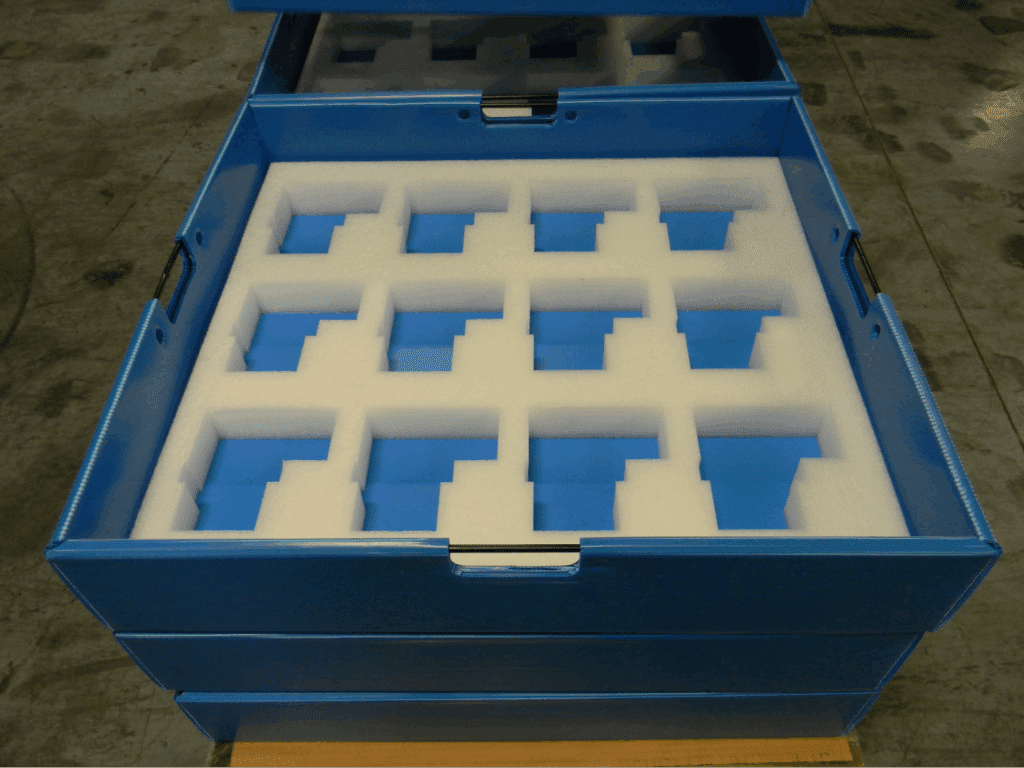
Optimize Your Packaging with Custom Foam Dunnage for Enhanced Protection and Efficiency
Foam dunnage is an indispensable solution for businesses aiming to protect their products during transit and storage. Its unique blend of shock absorption, lightweight construction, and customizability meets the complex needs of industries ranging from automotive to electronics. By considering factors such as product fragility, shipping conditions, budget, environmental impact, and industry standards, you can select the optimal foam type—whether it’s cost-effective EPS, adaptable PU, durable PE, versatile EPE, premium XLPE, or eco-friendly EPP.
Ultimately, investing in reusable dunnage is a smart approach to reducing damage and enhancing cost efficiency. Ready to transform your packaging solutions? Reach out to Universal Package today and discover how our custom foam dunnage solutions can optimize your supply chain, protect your products, and support your business goals.