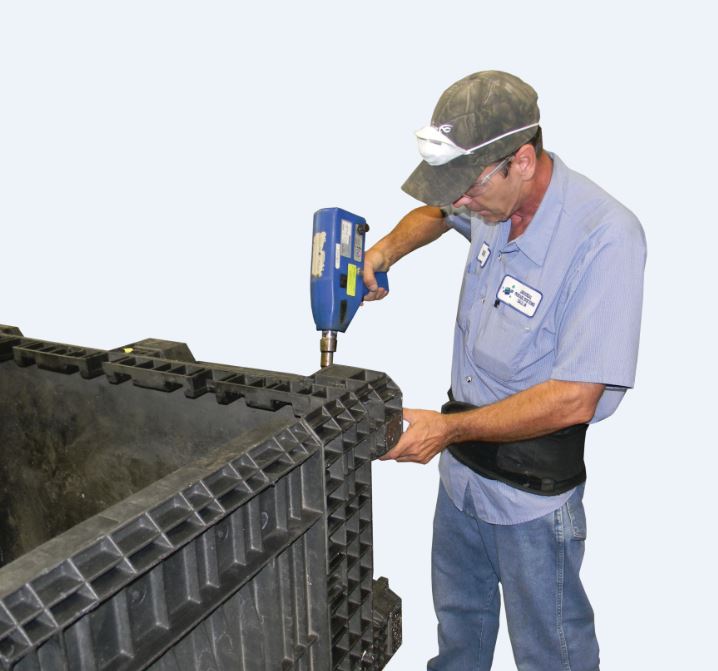
We understand reusable plastic packaging containers and steel racks take a beating while in transit and at your facility. After months and years of daily wear and tear, you and your customers know these containers need attention.
Before you place another order for new replacement containers, you should have your material handling systems evaluated for container repair.
With our understanding of container and steel rack functionality, there’s a good chance repairs can be made to existing containers and racks. Using the proper equipment and expertise, we get your units back in your system at a much lower cost than buying new units.
Why consider taking advantage of container repair services?
Increased cost savings, help the environment, and keep your lot cleaned up, organized and away from the attention of the Fire Marshall. Perception of a facility goes a long way.
Container Repair Process
When your containers arrive in our facility they are put through a rigorous inspection process. The containers are sorted and during inspection, usable parts begin to be matched with other usable parts.
For instance, a solid or repairable base goes with a wall from a unit that has a base that cannot be repaired. This is the least costly repair method and will quickly save you money.
Units having minor cracks and non-structural damage are sent to our plastic welding facility. All holes and cracks are welded and reinforced. Any unit with less than 3 runners (fork truck safety straps) missing is considered repairable.
While evaluating steel racks and containers, we mainly look at the interior dunnage, curtains and frames. Typically we don’t repair container frames that are completely bent, however we will cut and reinsert a frame post if possible. It all depends on the complexity of the rack we receive.
Steel rack and plastic bulk container interior dunnage part replacement is our specialty. We have the capability to die cut plastic corrugated replacement parts, water jet foam parts and can machine any plastic component replacement part.
For low volume replacements we have the ability to eliminate die costs and use our CAD table to cut plastic corrugated and foam components. For any job we can’t reproduce the part, we reach out to the previous vendor for replacement parts, this helps keep all repairs in one place and eliminates the customers’ management time.
Once the inspection process is complete and inventoried (repairable or rejected), along with parts required, a quote is submitted to our customer to show the evaluation of each item and cost to get the units back in working condition.
Cost Savings
Based on workload and number of containers to be repaired, container repair services greatly reduce the lead-time to get the units back in the system, versus purchasing new units. Usually new units are needed at a lower volume than original purchased quantity. That factor drives the cost of new replacement units to a much higher level than the original build.
In this instance, container repair not only reduces cost, but also gets containers back in action where you need them most.
Another opportunity for cost savings is when a product run is over and racks or containers need to be eliminated. In this scenario, we try and retrofit the racks for future projects so there is a greater cost savings to the customer by repurposing existing containers.
Eco Friendly
Repair services provide you with the opportunity to get the most out of any Returnable Packaging System. Recycling containers to be put back in your system and recycling non-repairable parts and container materials greatly benefits the environment.
All plastic bulk containers that are not repairable are recycled. There is a return to the customer for materials that get recycled. The return is usually lower for these materials because of the costs incurred during container inspection. For example, if we receive 100 units and can repair 60% of them, the recycled value is set at a rate about 1/3 of what a recycler might pay. The value gained is in the repaired units.
Any unit that is very complex and needs to be disassembled before recycling has little value in recycled materials. In some cases, to eliminate these units, we charge labor to break them down and get them to a recyclable point.
Look at the back lots at your facilities. We can help clean these up and improve the overall safety, quality and perception of your business and facilities. Perception and cost savings is everything! Let’s get the containers back in working order and keep your products moving.
Contact us to evaluate your packaging units, get them repaired and back in your system saving you money.